Struggling to get custom PCBs for your prototype due to long lead times? Traditional PCB manufacturing is often too slow and costly for one-off or low-volume designs, which can delay your entire development process.
3D printed circuit boards (PCBs) are created using additive manufacturing to build the board substrate and conductive traces layer-by-layer, enabling rapid, single-step fabrication of custom electronic circuits.

3D printing caught my interest when I needed a quicker way to test circuit layouts without waiting weeks for factory-made boards. I saw how the process gave me control and speed. In this article, I’ll walk you through what 3D printed PCBs are, how they work, and what tools and materials you need. If you’re a mechanical engineer, a product designer, or just someone curious about innovation in electronics, you’ll find practical insights here.
What is a PCB? What is PCB printing?
Before diving into 3D printing, what is a traditional PCB? How does the concept of "printing" a circuit board change with new additive technologies?
A traditional PCB (Printed Circuit Board) is a rigid or flexible board made from fiberglass and copper layers. It electrically connects and supports electronic components through copper traces. While PCB printing originally referred to chemical etching of copper, it now also includes advanced methods like 3D printing.
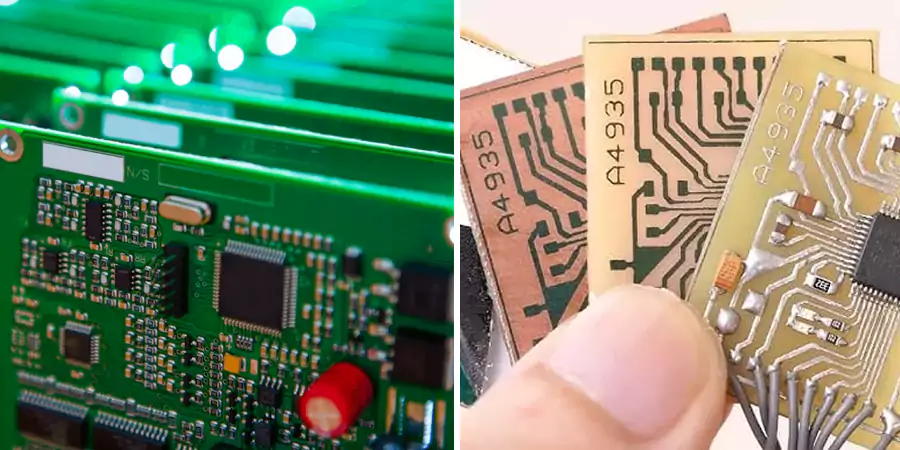
Understanding PCBs starts with their core function: replacing messy wires with organized copper pathways. Traditional manufacturing uses chemical etching or CNC milling to remove unwanted copper from a laminated board. This works for mass production but has drawbacks.
3D printing revolutionizes this process:
- Material Deposition: Conductive inks1 or pastes are extruded precisely onto substrates.
- Layer-by-Layer Construction: Insulating and conductive layers alternate.
- Direct Digital Fabrication2: CAD models drive printing without physical masks or tooling.
Key Differences in Printing Methods:
Method | Materials Used | Best For | Speed |
---|---|---|---|
Inkjet Printing | Conductive nano-silver ink | High-detail prototypes | Moderate |
Aerosol Jet | Suspended metal particles | Complex 3D geometries | Slower |
Extrusion | Conductive thermoplastics | Low-cost functional boards | Fastest |
This shift enables unprecedented flexibility. I’ve printed curved PCBs for robotics clients – impossible with flat-board techniques. The elimination of chemical baths also makes workshop integration safer and cleaner.
What Is the 3D Printed Circuit Board Process?
How do you go from a digital file to a physical, functional 3D printed PCB? What are the key steps involved in this additive manufacturing workflow?
The process involves creating a circuit design in EDA software, exporting it to a multi-material 3D printer, and additively manufacturing the board by depositing layers of substrate and conductive ink or filament.
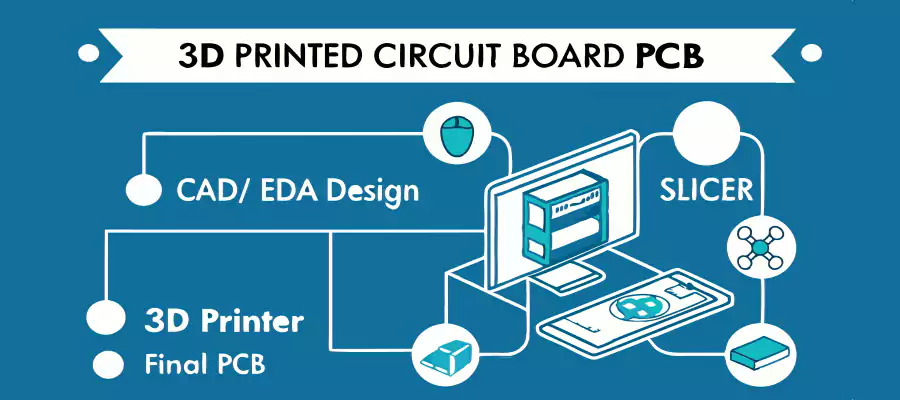
Breaking down the 3D PCB process in steps
Here is a step-by-step breakdown of how a 3D printed PCB is made:
Step 1: Design
You create a layout using CAD software that supports both mechanical and electrical paths. The files are exported in STL or similar formats.
Step 2: Material Selection
Use two kinds of filaments—one for structure (PLA, PETG), one for conductivity (graphene, carbon-based, or metal-filled filament).
Step 3: Printing
Using a dual-extrusion 3D printer, the board is printed layer by layer. The machine pauses to allow component insertion if needed.
Step 4: Post-processing
Once printed, the board may need soldering, testing, or reinforcing with conductive paste3 to improve connection quality.
Step | Tools Needed | Notes |
---|---|---|
Design | CAD software (Fusion 360) | Must export with accuracy |
Materials | PLA + Conductive Filament | Conductive filament is the bottleneck |
Printing | Dual-extrusion 3D printer | Needs calibration for accuracy |
Assembly | Manual insertion + testing | Simple for low-voltage applications |
This entire workflow can often be completed in a matter of hours, rather than the days or weeks required for traditional PCB fabrication.
What Design Tools Are Used for 3D-Printed Circuit Boards?
To create a 3D printed circuit board, what kind of software do engineers use? Is it standard CAD software, or are specialized tools required?
Engineers use standard EDA (Electronic Design Automation) software like Altium, Eagle, or KiCad to design the circuit, then export the file to specialized slicer software provided with multi-material 3D printers.
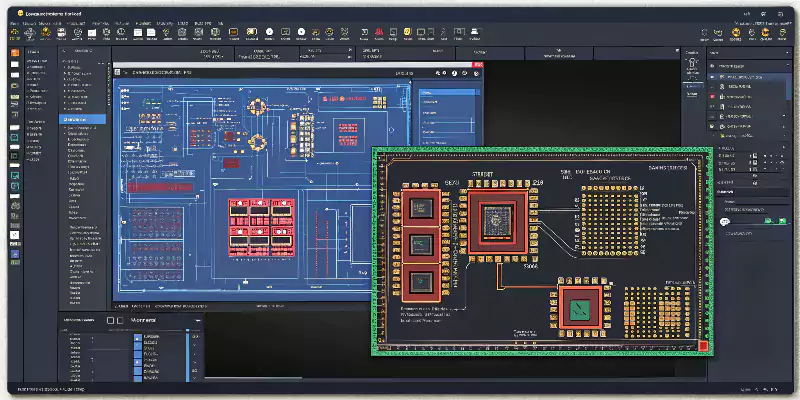
Going Deeper: What Software Do You Need for 3D Printed PCBs?
Designing 3D printed PCBs combines tools you're already familiar with and new ones for 3D printing. The good part is, you can start your design using standard electronic design software.
1. EDA Software – The Starting Point for Every PCB
All PCB designs begin with Electronic Design Automation (EDA) software4. This is where you design the circuit and prepare the board layout.
Step | What You Do |
---|---|
Schematic Design | Draw the logic diagram and show how parts connect. |
PCB Layout | Place components on a virtual board and connect them with copper traces. |
File Export | Save the layout in formats like Gerber or STEP. |
Popular EDA Tools:
Tool | Key Features |
---|---|
Altium Designer | Used in professional settings, offers advanced features. |
Autodesk Eagle | Good for both hobbyists and pros, links with Fusion 360. |
KiCad | Open-source, improving quickly, great for flexible use. |
2. Slicer and Printer Software – Turning Your Design into a 3D Print
This step is where the 3D printing part begins. You use slicing software to prepare the print.
Step | What Happens |
---|---|
File Import | Load your PCB design file into the printer’s software. |
Slicing | The software slices the model into layers. |
Toolpath Generation | Creates paths for both plastic and conductive materials. |
Print Settings & Preview | Adjust settings and check the preview before printing. |
Examples of Printer Software:
Printers from Nano Dimension or Voltera often come with their own software. These tools handle dual-material printing and support precise setup for conductive inks and substrates.
The smooth link between your EDA software and the printer’s slicer is what makes fast PCB prototyping possible. You stay in control from design to finished board, all without waiting for a factory.
Can I use filament in a 3D printer?
Standard printer filament creates plastic toys. Electronics demand conductive paths. Special filaments now enable real circuits from desktop machines.
Yes, conductive filaments like Proto-pasta or Multi3D Electrifi work in standard FDM printers. They contain copper/carbon particles. Print traces first, then switch to insulating filament for structural layers. Dual-extruder printers simplify this.
Using filament for circuits requires understanding material limitations. Standard PLA won’t conduct electricity. Conductive filaments mix thermoplastics with metal/particles, creating pathways. But performance varies dramatically:
Filament Types & Properties:
Filament Brand | Conductive Filler5 | Resistivity (Ω·cm) | Best Use Case |
---|---|---|---|
Proto-pasta | Carbon black | 15 Ω·cm | Low-power sensors |
Electrifi | Copper alloy | 0.006 Ω·cm | Arduino shields |
BlackMagic | Graphene | 0.5 Ω·cm | Flexible wearables |
Printing Process Essentials:
- Nozzle Selection: Use hardened steel nozzles (abrasive particles wear brass)
- Print Settings: Slow speeds (<30mm/s) ensure consistent trace density
- Layer Adhesion: Print bed at 60°C prevents warping
- Multi-Material Printing: Requires dual extruders (one conductive, one insulating)
Limitations to Accept:
- Conductivity is 10-100x worse than pure copper
- Max current limited to ~500mA
- Not suitable for high-frequency circuits
For a university lab, we printed drone motor controllers using Electrifi. They handled 12V/2A loads successfully. Desktop printing works for proof-of-concepts but not flight hardware.
Can electronic components be 3D printed?
We can 3D print the board and the wires. Can this technology also print the actual components like microchips, resistors, or capacitors?
Some basic passive components (resistors, capacitors, antennas) can be fully printed. Active components (ICs, processors) cannot – they must be mounted later. Hybrid approaches combine printed traces with placed components.
Not all components are printable today. Understanding this prevents project stalls. At Allied Metal, we categorize printable electronics by complexity:
Fully Printable Components:
- Resistors: Carbon-infused traces with controlled resistance
- Capacitors: Overlapping conductive layers separated by dielectric
- Antennas: Precise spiral traces optimized for frequency
- Connectors: Plastic housings with printed conductive pins
Components Requiring Mounting:
- Semiconductors: Diodes, transistors, ICs
- High-Power Parts: >1W resistors/chips needing heat dissipation
- Precision Devices: Crystal oscillators, MEMS sensors
Material-Driven Limitations:
Component | Printable Material | Performance Gap |
---|---|---|
Resistor | Carbon-laden polymer | ±20% tolerance (vs ±1% SMD) |
Capacitor | Conductive/insulating inks | Max 10nF capacitance |
Battery | Zinc-air chemistry | Very low energy density |
We printed strain gauges for a factory robot client. Combined with mounted amplifiers, they cut part costs 40%. But microcontrollers still came from Samsung. Strategic printing delivers value without overpromising.
What are the advantages and disadvantages of 3D printed circuit boards?
Is a 3D printed PCB always the better choice? What are the key pros and cons of this technology compared to traditional PCB manufacturing methods?
The main advantages are speed for prototyping, design freedom for complex shapes, and cost-effectiveness for single units. Disadvantages include lower conductivity, limited material options, and higher cost for mass production.
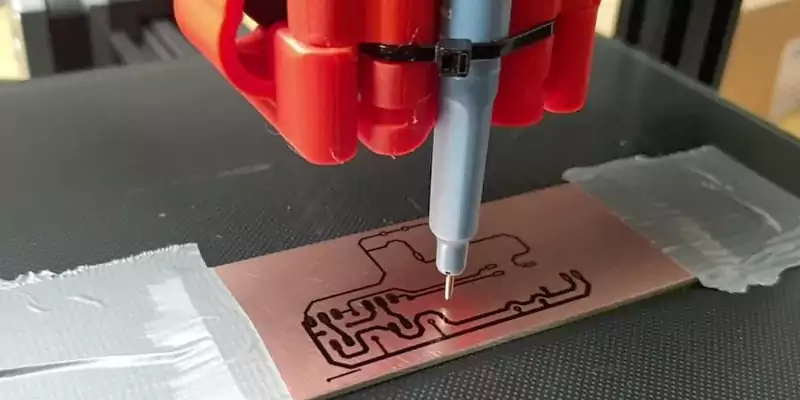
Weighing the Pros and Cons of 3D Printed PCBs
3D printed PCBs open up new possibilities, especially for prototyping and custom builds. But they’re not meant to replace traditional PCBs in every case. It’s important to understand both sides.
Pros | Cons |
---|---|
Fast Prototyping | High Cost for Large Batches |
Print a working board in hours, not days. Speeds up early development. | Not cost-effective when producing hundreds or thousands of units. |
More Design Flexibility | Lower Electrical Performance |
Create complex, curved, or 3D-shaped boards that fit product housings. | Conductive materials used have higher resistance than copper. Not ideal for high-power or RF use. |
On-Demand, Chemical-Free Production | Limited Material and Component Options |
No need for etching or waste. Print only what you need, when you need it. | Material choices depend on the printer. Some parts may not solder well. |
Great for One-Offs or Small Runs | Weaker and Less Heat-Resistant |
No setup costs or tooling fees. Perfect for early prototypes. | Printed boards may not match the strength or heat resistance of FR-4 boards. |
My take? 3D printed PCBs are a game-changer for quick testing and custom shapes. They save time, reduce waste, and unlock creative freedom. But for high volumes or demanding electrical needs, traditional PCBs are still the better choice.
How does Allied Metal 3D print PCBs?
How does a company like Allied Metal leverage this technology? What kind of 3D printed PCB services can you provide for an engineer developing a new product?
At Allied Metal, we use advanced multi-material 3D printers to offer rapid prototyping of 3D printed PCBs. We help engineers quickly fabricate and test complex, custom circuit board designs.
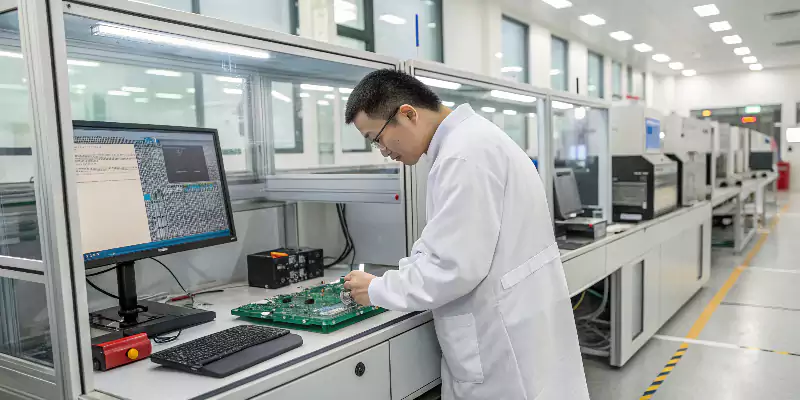
Inside Allied Metal’s 3D PCB Capabilities
At Allied Metal, we help engineers like David speed up product development with fast and flexible 3D printed PCB solutions. Our service tackles common challenges like long lead times and rigid design limitations.
🔧 Advanced Technology
We use high-end multi-material 3D printers designed for electronics—not regular desktop printers.
Our machines print:
- Durable polymers as the board base (strong and heat-resistant)
- Silver-based conductive ink for precise circuit paths
This lets us create multi-layer, complex PCBs in one automated step—fast and accurate.
🔄 Easy Process
We make it simple for engineers to prototype and iterate:
-
Send Your Design
David sends us his PCB file. We check if it fits our 3D printing specs. -
Fast Prototyping (24–48 hours)
We print and deliver a ready-to-test board—fast. -
Quick Iteration
If changes are needed, just send a new file—we reprint right away. -
Support for 3D Shapes
We can print curved and non-flat PCBs for tight spaces, ideal for robotics and custom enclosures.
✅ Why Choose Us
Our 3D PCB service gives you:
- Faster development cycles
- Easy design updates
- Compact, customized board designs
With Allied Metal, turning ideas into real, testable hardware has never been easier.
Conclusion
For rapid prototyping, 3D printed PCBs offer incredible speed and design freedom. While traditional methods rule mass production, 3D printing is the key to faster innovation.
-
Learn about conductive inks, their applications, and how they enhance the capabilities of modern electronics. ↩
-
Discover the advantages of Direct Digital Fabrication in manufacturing processes, including speed and customization. ↩
-
Discover the importance of conductive paste in electronics, its applications, and how it enhances the performance of printed circuit boards. ↩
-
Explore this link to understand the fundamentals of EDA software and its importance in PCB design. ↩
-
Explore this link to discover various conductive fillers that enhance 3D printing performance and applications. ↩