Laser Cutting Service
Laser cutting allows for tighter accuracies on a smaller scale than any other metal cutting method.
Basics Of Laser cutting
Laser cutting is a material-cutting method that uses an intensely focused, coherent stream of light to cut through metals, paper, wood, and acrylics. It is a subtractive process that removes material during the cutting process using vaporization, melting, chemical ablation, or controlled crack propagation. Laser optics controlled by Computer Numerical Control (CNC) can drill holes as small as 5 microns (µ). The process does not produce residual stresses on materials, making it possible to cut fragile and brittle materials.
Laser drilling uses several methods, including single-shot, percussion, trepanning, and helical. Single-shot and percussion laser drilling produce holes at a higher rate than the other processes. Trepanning and helical drilling, produce more accurate, higher-quality holes.
Laser cutting is a non-contact process where cutting is completed without making contact with the cut material. It can shape high-strength, brittle materials such as diamond tools and refractory ceramics. The first production laser cutting was introduced in 1965 and was used to drill holes in diamond dies. It was later used for cutting high strength alloys and metals such as titanium for aerospace applications. Its range of applications covers the cutting of polymers, semiconductors, gems, and metallic alloys.
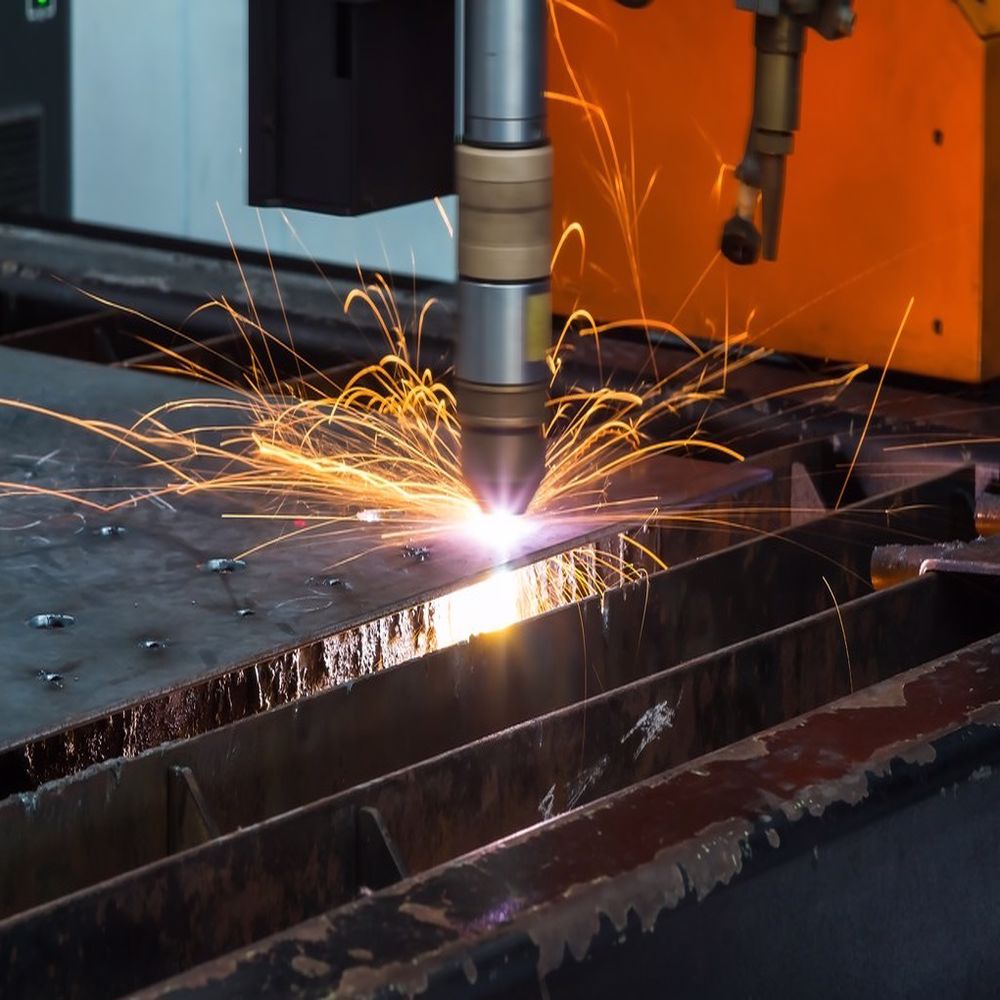
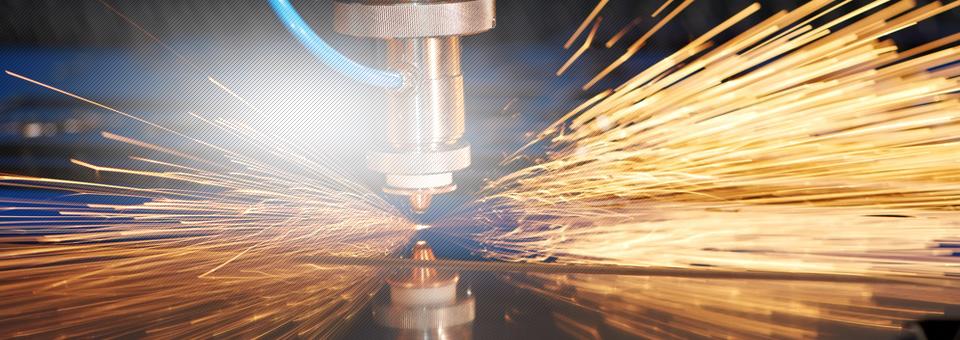
Laser Cutting Theory and Working Principle
Laser stands for “light amplification by stimulated emission of radiation”. Aside from the cutting applications of lasers, they are used for joining, heat treating, inspection, and free form manufacturing. Laser cutting differs from other laser machining processes since it requires higher power densities but shorter interaction times.
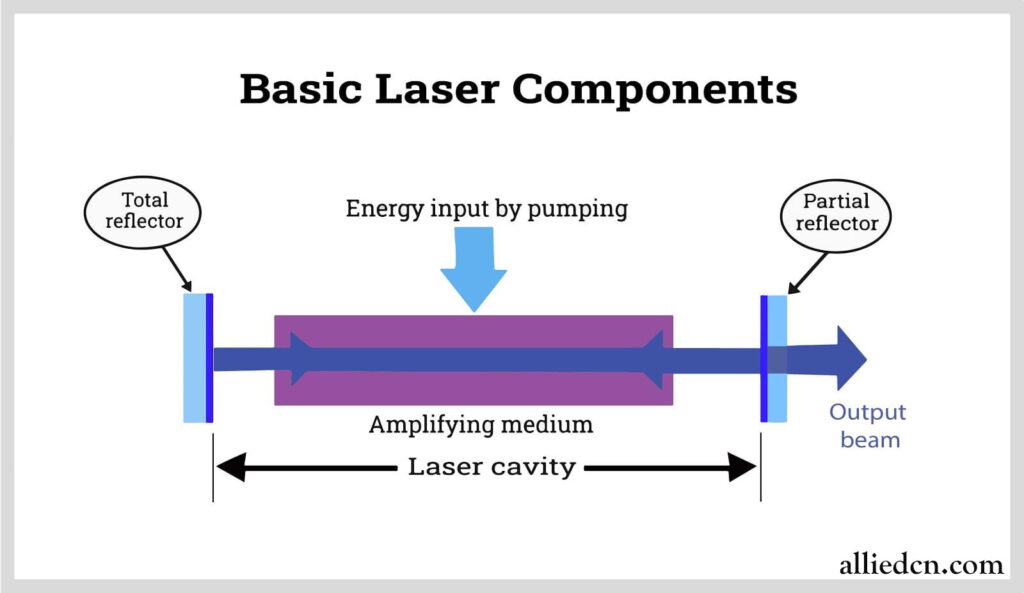
Lasers are generated by a high-intensity light source inside a reflective laser cavity, that contains a laser rod that generates the radiation. The light source stimulates the laser rod’s atoms as they absorb wavelengths of light from the light source. Light is composed of small bundles of photons that strike the lasting media atoms energizes them. The photon’s energized atoms, give off two more photons with the same wavelength, direction, and phase, called stimulated emission. The new photons stimulate other energized atoms producing more photons, causing a cascade of excitations.
The photons move perpendicular to parallel mirrors located on the ends of the laser rod but stay within the laser rod. One mirror is transmissive, enabling the partial escape of light from the cavity. This escaping stream of coherent, monochromatic light is the laser beam used to cut the material. Another set of mirrors or fiber-optics direct light into a lens that focuses the light into the material.
The three main types of lasers used for cutting, are CO₂, Nd-YAG (Neodymium Yttrium-Aluminum-Garnet) lasers, and fiber-optic lasers. They differ in the materials used to generate the laser beam.
Fiber-optic Laser
Fiber-optic lasers are the newest and most popular types of lasers because that they can generate different wavelengths for more precise cutting. They use an optical fiber cable made of silica glass to guide the light. The laser beam produced by fiber-optic lasers is more precise because it is straighter and smaller.
Fiber lasers vary according to their laser source mixture, including ytterbium-doped, thulium-doped, and erbium-doped. The choice of mixture is dependent on the application where they will be used and their wavelengths. For example, erbium generates light in the 1528 nm to 1620 nm range. Ytterbium produces light with wavelengths of 1030 nm, 1064 nm, and 1080 nm.
The two modes of fiber optic lasers are single and multiple with the core diameter of single-mode lasers being between 8 µ to 9 µ while multiple mode lasers have diameters of 50 µ up to 100 µ. Of the two modes, single-mode lasers are more efficient and produce a better quality beam of light.
Fiber-optic lasers are classified as solid-state since their power source is silica glass mixed with rare earth elements. This is contrary to CO₂ lasers that use gas to create their power. An additional difference between the two forms of power is their wavelengths, with fiber-optic lasers producing wavelengths of 780 nm up to 2200 nm while CO₂ lasers have wavelengths of 9600 nm up to 10,600 nm.
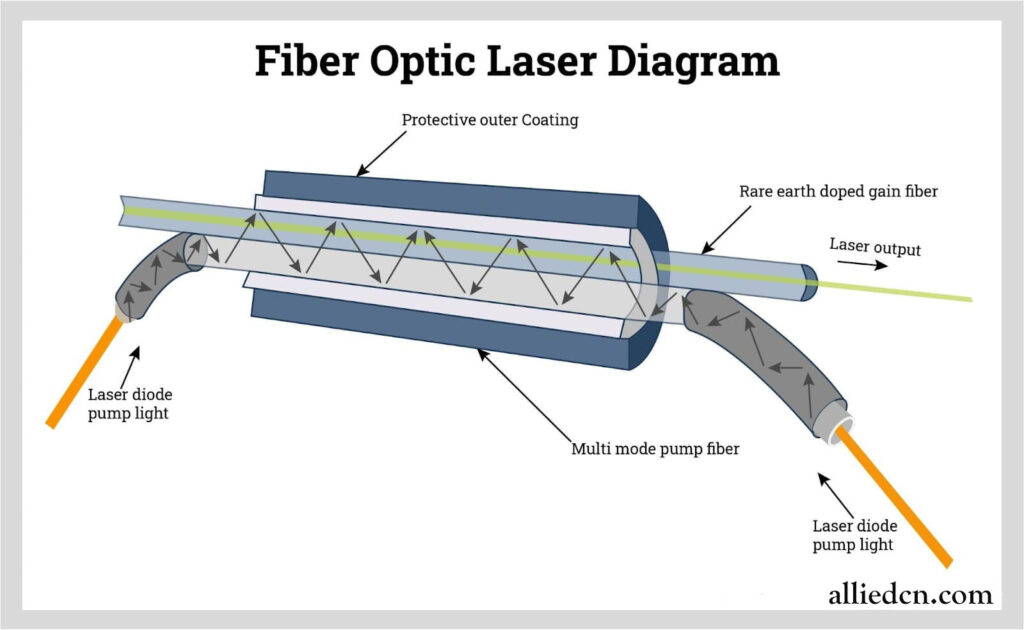
CO₂ Lasers
This type has a gas discharge lasing medium filled with 10 – 20% carbon dioxide, 10 – 20% nitrogen, traces of hydrogen and xenon, and helium for balance. Instead of light, laser pumping is done by discharging an electrical current. When the electrical discharge passes through the lasing medium, nitrogen molecules become excited, bringing it to a higher energy level. Unlike what was described before, these excited nitrogen molecules do not lose their energy by photon emission. Rather, it transfers its vibrational mode energy to CO₂ molecules. This process continues until most of the CO₂ molecules are in a metastable state. The CO₂ molecules then emit infrared light at either 10.6 µm or 9.6 µm, which brings them to lower energy levels. The resonating mirrors are designed to reflect the emitted photons on those wavelengths. One mirror is a partially reflecting mirror allowing the release of the infrared beam that is used for cutting the material. After releasing infrared light, the CO₂ molecules return to the ground state by transferring their remaining energy to the doped helium atoms. The cold helium atoms then become hot which are cooled by the cooling system of the laser. The efficiency of a CO₂ laser is around 30% which is higher than other lasers.
Crystal (Ruby, Nd, and Nd-YAG) Lasers
Unlike the CO₂ laser, this type is a solid-state laser that uses a synthetic crystal as a lasing medium. The most popular is the YAG (Y3Al5O12) crystal doped with 1% ionized neodymium (Nd3+). The Nd ions replace the Y ions in the crystal structure in this crystal. The length of the rod is about 4 inches (10 cm) with a diameter of 2.4 to 3.5 inches (6 to 9 cm). The ends of the YAG rod are polished and coated by highly reflective materials acting as the resonator system.
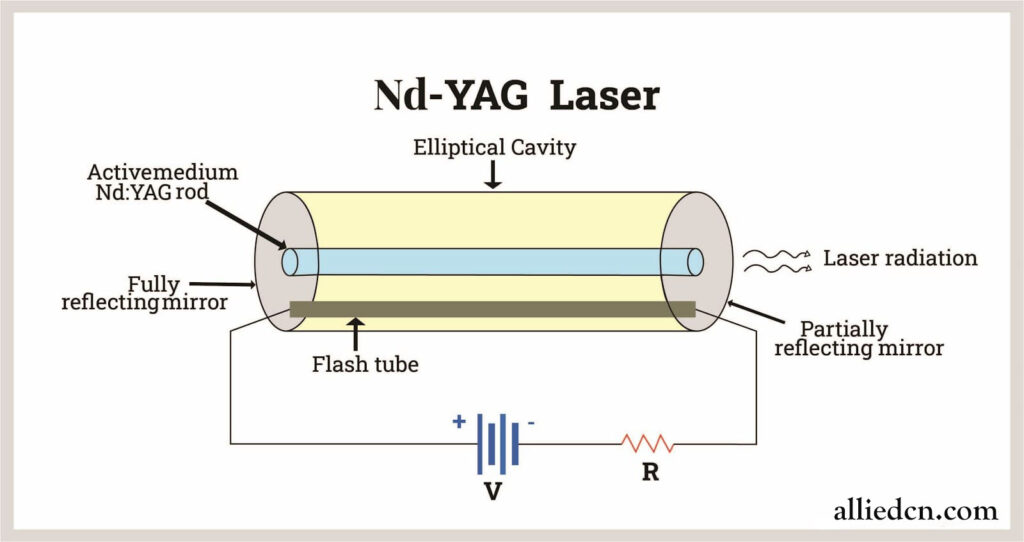
Laser pumping is achieved by krypton flashlamps or laser diodes. This laser pumping excites the Nd ions into higher energy levels. After a short while, the excited Nd ions move into a lower, more stable state, without emitting photons. This process goes on until the medium is populated with excited Nd ions. From its metastable state, the Nd ions release infrared light with a wavelength of 1064 nm.
Fiber-optic Laser
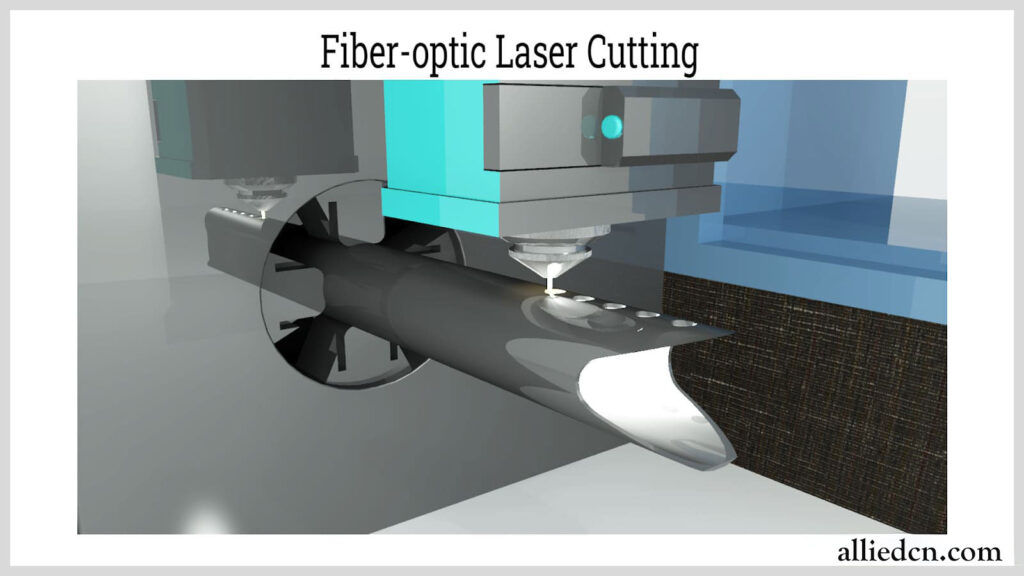
It is known that as light travels through a fiber-optic, it remains inside with minimal energy losses. This makes fiber-optics more stable than other types that require them to be aligned accurately.
Assist Gases
Laser cutting uses assist gasses, such as compressed air, nitrogen, or argon, injected at the nozzle to supplement the cutting process. Assist gasses help start the cutting by using an exothermic reaction, a chemical that releases energy through the use of light or heat. The use of assist gasses helps in a more effective transference of heat than can be created by the beam alone. In cutting metals, assist gasses help remove the molten metal.
Advantages of Laser Cutting
Laser drilling is widely used in aerospace, automotive, electronics, and tool machining. Below are the main advantages of using lasers for drilling.
As mentioned earlier, since the laser drilling process has no cutting tools involved, there is no issue of tool wear or damage. In conventional drilling, drill bits can become dull, making the cutting slower and producing more heat. This can distort the material and change its mechanical properties due to heating.
Since laser beams can be focused, this allows precise drilling of small holes that conventional drilling cannot achieve. The hole depth can be controlled even for micro-scale holes. Moreover, the process is digitally controlled by CNC methods. All parameters can be automatically controlled, producing consistent and repeatable results.
Secondary processes such as deburring are required in manufacturing precision parts to remove surface irregularities, metal spurs, raised edges, slags, and dross. Even the most accurate fabrication techniques such as laser cutting technology, tend to develop dross or thermal burrs. However, in comparison with conventional cutting, laser-cut parts still have superior edge quality. This effectively lessens the cost of secondary processes, particularly deburring, which can be as high as 30% of the operating costs.
This means very deep holes with small diameters can be drilled without issues. Drilling these holes using conventional drills causes the tool to heat up, wobble, and break due to torsional stress. Using a laser creates no frictional resistance and is only limited by the laser generator and the optical systems used.
Lasers can cut and drill different materials that are difficult for conventional machining. Lasers can cut high-strength metals such as titanium and steel superalloys. Aside from these high-strength metals, laser cutting is used for cutting crystals, ceramics, and even diamonds because of its ability to do controlled fracture.
Since there is no required tool positioning against the workpiece, drilling speeds only depend on the configuration of the optical system and the movement of the cutting head. Moreover, the complexity of the profile to be cut has minimal effect on the incremental cost of operating the machine.
Since most of the molten material is blown off by the assist gas, no residual stresses are present along the drilled edges. This results in a clean, mechanically stable cut.
Why Choose Us For Your CNC Machining in China
Comprehensive, all-in-one services
Highest standards of quality
Scalable for projects of any size
We offer machining solutions and surface finishing in a single facility, which helps minimize logistical difficulties and saves you both time and money.
We meet the relevant ISO requirements for quality and process control, and our safe and advanced facility is staffed by experienced technicians to ensure the best possible results.
We offer rapid prototyping for small-batch orders, low-volume production, and manufacturing for batches of 100,000+ components, as well as full-scale manufacturing. No project is too big or too small.
Rapid turnaround times available
Advanced, specialized equipment
Experienced and skilled engineers
Allied offers rush service for select projects, such as urgent prototyping jobs. We can build and send your prototype components anywhere in the world in just a few days.
We use only the most advanced CNC equipment. Not only does this ensure that you get the best possible results, but our focus on automation and efficiency means that you save money.
50+ engineers and designers, the most specialized and highly-skilled, ensure that you can trust our staff to handle your project.
How ALLIED Works
One Stop All Solutions!
Upload a CAD File
To start, simply select a manufacturing process and upload 2D/3D files.
Design Analysis Get lmplemented
We’ll send you design for manufacturability(DFM) analysis and the timing price as long as we receive your CAD file
Manufacturing Begins
Once you have confirmed your quotation and place your order, we will start the manufacturing process,and we also provide some optional finishing services
Parts are shipped on its way to you!
Our advanced CNC equipment allows us get products finished in a short time