Engineering Precision Surfaces
Surface Finishes
One-stop parts machining service manufacturer
Make your parts more complete
Surface Finishing
EFFICIENT PROCESSING OPTIONS
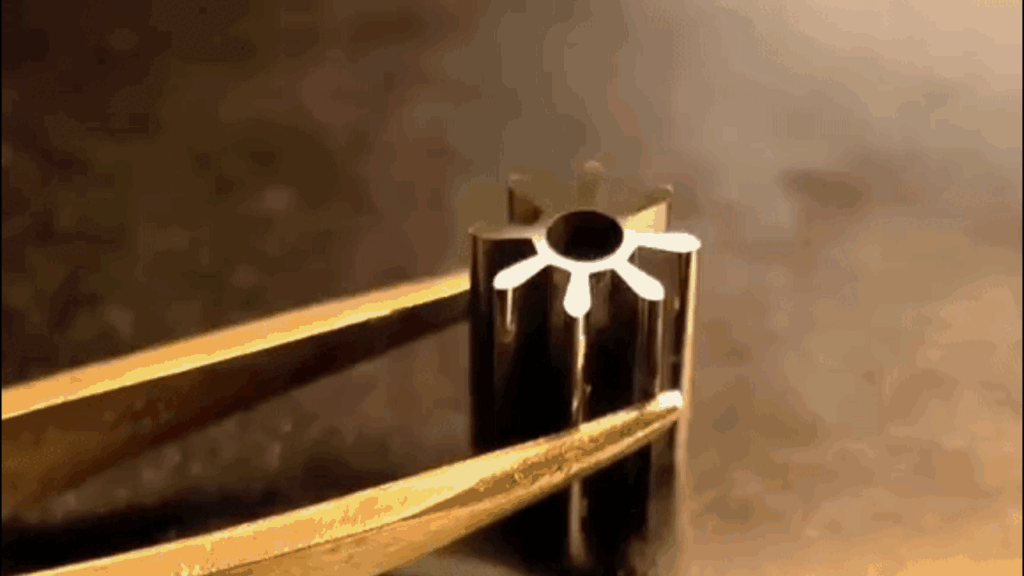
In order to prevent corrosion or simply improve appearance, engineers usually specify additional finishing processes for some or all of the outer surfaces of metal parts after processing or manufacturing, which we call surface finishing.
At Allied, we offer a wide variety of surface finishes for our CNC milled and turned parts, and for components manufactured with EDM wire machining.
From anodization to brushing, powder coating and engraving, we can handle every step of the surface finishing process – simplifying the manufacturing process and providing you with surface finishing.
Common types of surface finishes
There are no limits to the finishing process. Irrespective of the material, innovative Allied technology enables surfaces to be individually finished according to the subsequent area of application and the requirements to be placed on the workpiece. Whether smoothing, polishing, rounding or deburring – the careful combination of process media and corresponding machine technology enables us to produce the results that are just right for you.
To learn more about our surface finishes, just take a look at the page below.
Anodization (Type II & Type III)
Anodization is an electrochemical process used in aluminum, which results in the formation of a durable, corrosion-resistant and strong anodic oxide finish which will never chip and peel.
There are two commonly used types of titanium anodizing: Type II and TypeIII. Type I is far less common, and is used in specialized high-temperature treatments.
Type II anodization results in a relatively thin layer (8-12 μm) of material. It can be used to change the color of a component, and to make it more durable and corrosion-resistant. Type III anodization, often known as “anodizing hardcoat” consists of a thicker layer (50-125 μm) of material, and is used when durability, corrosion and wear resistance are essential.


Electroplating
Electroplating involves bonding a very thin layer of metal to your metal workpiece at a molecular level. The component is placed in a bath containing the dissolved metal. Then, an electric current causes the metal to be deposited onto the component, creating a uniform layer.
Electroplating can be done for purely cosmetic purposes, or to enhance corrosion resistance or other physical properties of a given component, depending on your needs.Electroplating treatment is a commonly used surface treatment method for precision machining of CNC aluminum products. Electroplating treatment is generally divided into different types such as chromium plating, zinc plating, copper plating, etc. Among them, chromium plating can obtain a bright luster, zinc plating can prevent oxidation and corrosion, and copper plating can improve conductivity and heat transfer.
Bead Blasting
Bead blasting is used to create a satin or matte finish with a raised surface texture. This removes tool marks, and is typically done for cosmetic purposes.
A stream of very small glass beads is blasted onto the component, creating this raised finish. The final texture of the finish depends on the size of the beads used to bombard the component.
Bead blasting processing speed is fast, usually only takes 5-10 minutes to complete, and the surface of the processed product is smooth with a uniform matte effect. In addition, Bead blasting is flexible and can be applied to most FDM materials. It can be applied at all stages from product development to manufacturing, from prototype design to production.


Polishing
There are several different methods of polishing, and they all have a similar effect. Electropolishing uses an electrochemical process to remove burrs and cosmetic imperfections, and level out the surface of a metallic workpiece. It also “passivates” the material, adding a micro coating that helps prevent corrosion. Electropolishing is ideal for components that must be both highly polished and corrosion-resistant.
Standard mechanical polishing can also be used to create a very high shine in metal components. A series of decreasing-grit polishers are used on the component until it has a very smooth, mirror-like finish. Note that parts that are polished in this manner cannot have extremely tight tolerance requirements, due to the removal of some material during the mechanical polishing process.
Brushing
It is a kind of surface treatment, rather than surface finishing. It harnesses a metal-wired brush or an abrasive pad to clean the surface and physically throw out all contaminants or particles on the surface of the parts.
Brushing creates a smooth, satin-like finish on the surface of the material. Using a medium-grit polisher, the component is polished in a single direction, creating extremely shallow grooves in the material, and creating an appealing finish and texture
Note that brushing is NOT ideal for components that require high corrosion resistance.

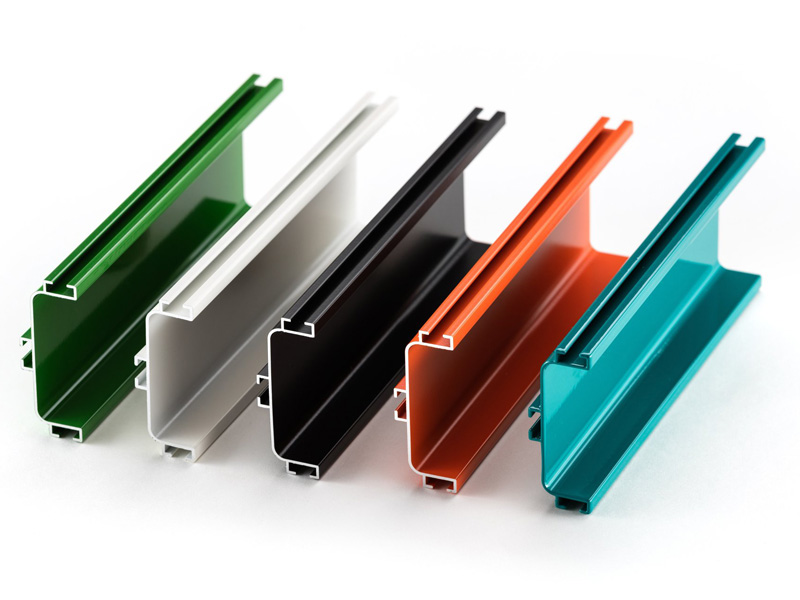
Powder Coating
Powder coating uses a polymer-based paint. The paint and the component that is being painted are charged with opposing electric currents, which attracts a thin, even layer of paint to the surface of the component.
Then, the component is baked and cured to smooth and harden the painted finish. Powder coating is available in a wide variety of colors. It can also help with corrosion and wear resistance, and it creates a very smooth, uniform surface.
Powder coating is a spraying process suitable for many different types of metal, wood, and plastic products.This coating provides excellent wear resistance, corrosion resistance, corrosion resistance, and aesthetic properties. Due to its environmentally friendly, efficient, and high-quality characteristics, this process has been widely used in various industries and application fields.
Laser Engraving
Laser engraving uses a specialized laser tool to remove a very thin layer of material from the work material. It is typically used for decorative purposes, but also may be used to add information to a component or part, such as a part number, serial number, brand name, and other such details
It can usually be used alongside other surface finishes (anodization, polishing, powder coating, etc.) during the finishing process.
Laser engraving is widely used in fields such as automobiles, molds, electronics, medical, military, aerospace, oil and gas, etc. In these industries, laser engraving and laser marking are widely used in daily work.

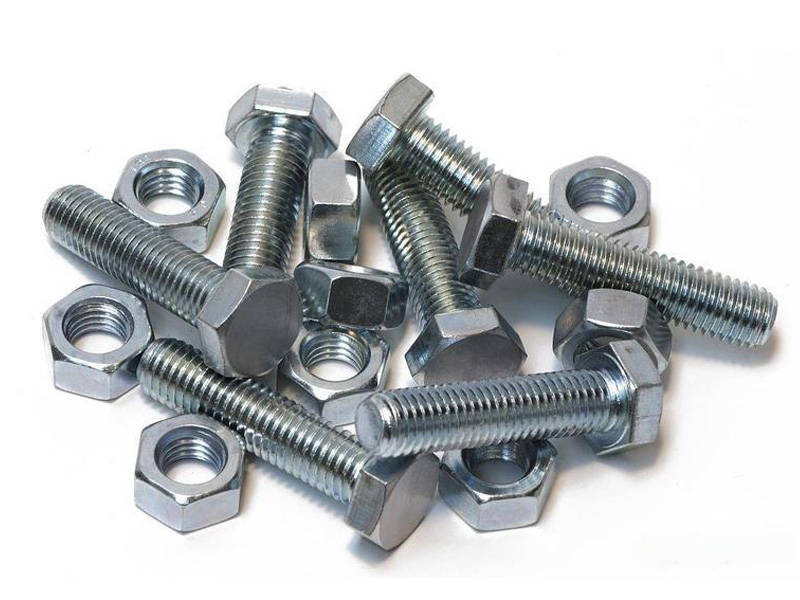
Zinc Plating
Zinc plating is identical to electro-galvanizing in principle because both are electro-deposition processes. However, zinc plating is used on small parts such as fasteners, crank handles, springs and other hardware items ratherthan sheet metal. The zinc is applied as an expendable electrode in a cyanide, alkaline non-cyanide, or acid chloride salt solution. Cyanide baths are the most operationally efficient but can potentially create pollutionand are hazardous.
Zinc plating is typically used for screws and other small fasteners, light switch plates, and various small parts that will be exposed in interior or mildly corrosive conditions. For use in moderate or severe environments,the materials must be chromate-conversion coated for additional corrosion protection.
In conclusion, surface finishes for CNC machined parts are instrumental in achieving the desired quality, functionality, and aesthetics. By utilizing the appropriate surface finishing techniques, manufacturers can enhance the performance, durability, and overall value of their CNC machined components.
If you have any questions or needs about the product, please fill in the following form and we will contact you as soon as possible.
Get In Touch With Us!
Phone
+ 86 1996 3099 511
quote@alliedcn.com
Address
No.5608,Xinhua Road,Weifang,Shandong,China