Common CNC Toolpath Types and Their Application Scenarios
- March 14, 2025
- Tony
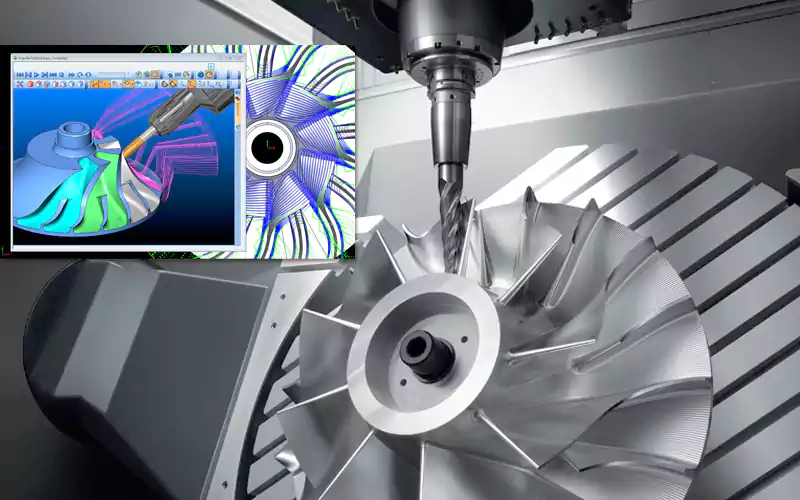
1. Overview of CNC Toolpath
CNC Toolpath Definition and Role
A CNC toolpath refers to the predefined route that the CNC tool follows during machining. The choice of toolpath directly impacts machining quality, production time, and cost.
Why Is Choosing the Right CNC Toolpath Critical?
Selecting the appropriate toolpath has a direct influence on CNC machining quality, efficiency, and cost:
- Ensure Machining Accuracy: Correct path planning reduces dimensional errors, ensuring the part stays within tolerance.
- Enhance Machining Efficiency: Optimized toolpaths minimize unnecessary tool movement, reduce load, and speed up cutting.
- Reduce Production Costs: Efficient cutting strategies reduce material waste, extend tool life, and lower tool replacement costs.
By carefully planning the toolpath, you can not only improve machining quality but also enhance overall production efficiency.
2. Classification and Characteristics of CNC Toolpath
CNC toolpaths can be categorized based on machining methods or goals.
Classification by Machining Method:

Milling Paths: 2D milling, 3D milling, multi-axis milling.
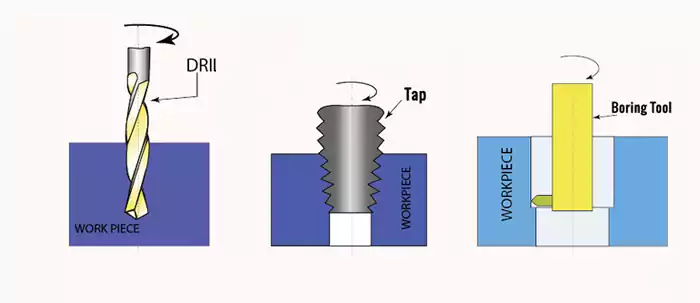
Drilling Paths: Drilling, tapping, boring.
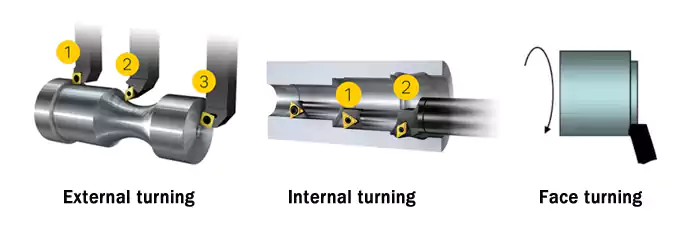
Turning Paths: External diameter turning, internal hole turning, and face turning.
Classification by Machining Objective:
- Roughing Paths: Prioritize fast material removal to increase productivity.
- Semi-finishing Paths: Balance between accuracy and efficiency, preparing for finishing operations.
- Finishing Paths: Focus on achieving high surface quality and dimensional accuracy.
3. Common CNC Milling Toolpath Types
Milling is one of the most common processes in CNC machining, used for cutting flat surfaces, cavities, curved surfaces, and external contours. Toolpaths in milling affect machining efficiency, surface quality, and tool longevity. Here are some of the most common milling toolpaths:
3.1 Contour Machining (Contouring)

- Function: Cuts along the boundary of the part to create precise profiles or internal cavity contours.
- Characteristics: Ideal for finish machining, ensuring high-quality surfaces and precise dimensions.
- Applications: Mold manufacturing, aerospace parts, complex curved parts.
3.2 Cavity Machining (Pocketing)

- Function: Removes large amounts of material from the part interior to create cavities or grooves.
- Characteristics: Typically uses layered cutting to reduce cutting load and enhance efficiency.
- Applications: Hollow parts, electronic equipment casings, grooves in mechanical components.
3.3 Plane Milling (Face Milling)
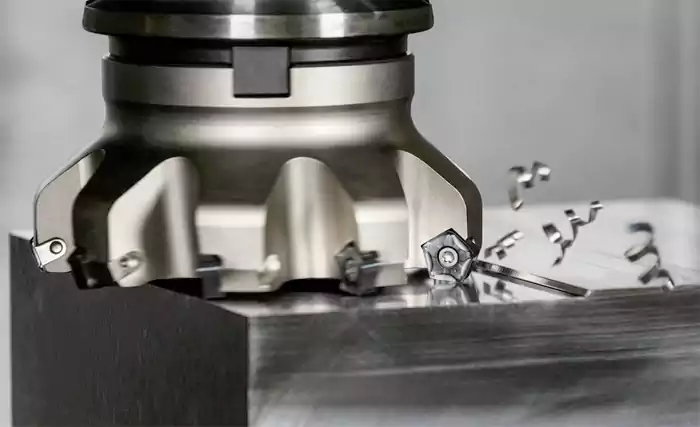
- Function: Efficiently removes material to achieve large surface machining.
- Characteristics: Large-diameter tools are used for rapid surface machining, ensuring flatness.
- Applications: Machine tool tables, jigs and fixtures datum surfaces, flat surfaces of box-type parts.
3.4 Contour Machining (Z-Level Milling)

- Function: Cuts along the Z-axis in layers, ideal for three-dimensional surface machining.
- Characteristics: Maintains a consistent depth of cut, reducing tool load and improving surface quality.
- Applications: Mold cavities, turbine blades, automotive exterior parts.
3.5 Helical Interpolation
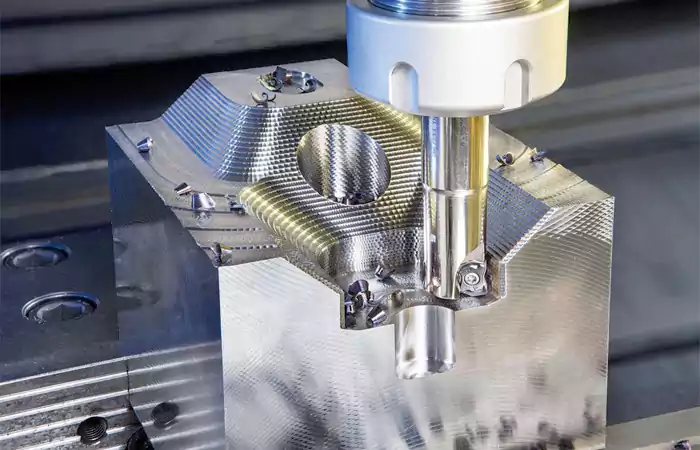
- Function: Tool feeds along a spiral path, resulting in smooth feeding and cutting.
- Characteristics: Reduces cutting impact, minimizes tool wear, and is suitable for hole machining.
- Applications: High-precision hole machining, ramp feed strategies, mold manufacturing.
3.6 High-Efficiency Dynamic Milling (HEM)
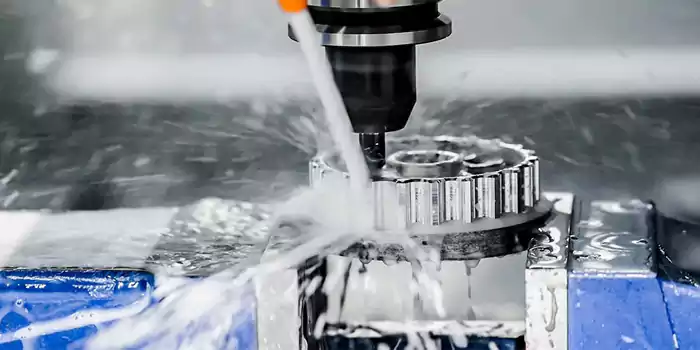
- Function: Optimizes toolpaths to maintain a constant cutting load, improving tool life.
- Characteristics: Reduces heat buildup, optimizes feed rates, and enhances cutting efficiency.
- Applications: Aerospace parts, machining of high-strength materials like titanium and stainless steel.
4. Common CNC Drilling Toolpath Types
Drilling is essential for hole machining in CNC processes. This includes drilling, tapping, and boring. Choosing the right drilling toolpath enhances hole machining accuracy and efficiency, and reduces tool wear.
4.1 Drilling Path
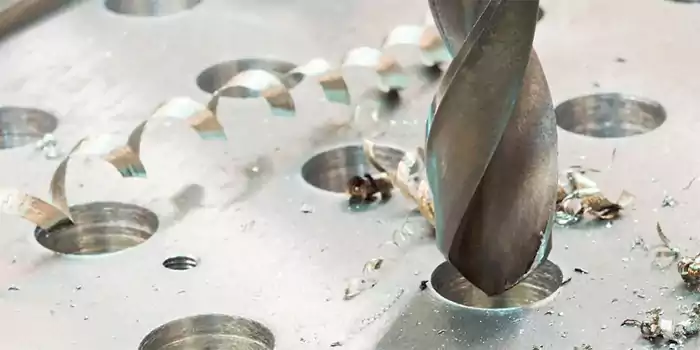
- Function: Used for making through or blind holes, commonly for connecting, assembling, and positioning.
- Characteristics: Axial feeding of the tool, usually with a coolant to minimize heat buildup.
- Applications: Bolt holes, positioning holes, pipe connection holes in mechanical components.
4.2 Tapping Path
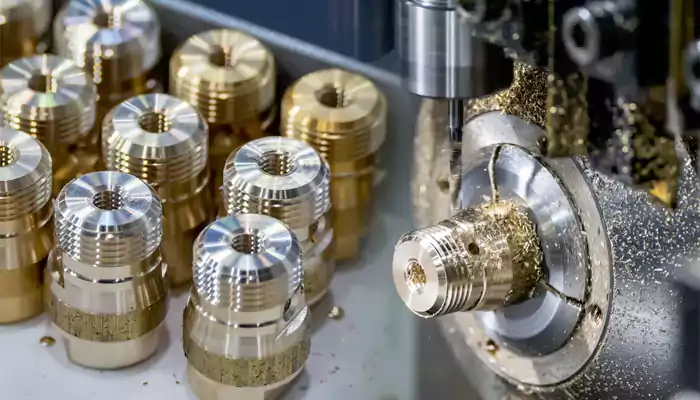
- Function: Used for processing internal threads to ensure accurate fitment for fasteners.
- Characteristics: Requires special tapping tools with feed speeds matching the pitch.
- Applications: Bolt fixing holes, electromechanical equipment connection holes, threaded holes in automotive parts.
4.3 Boring Path
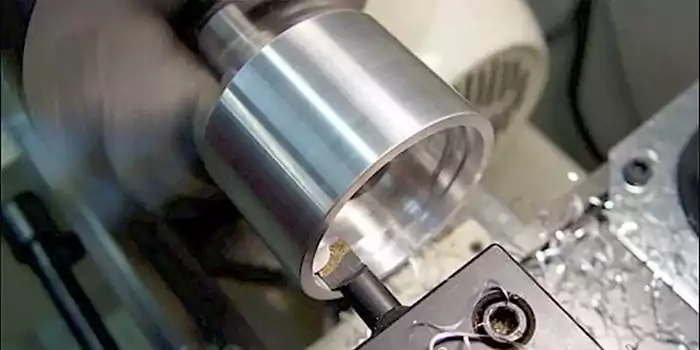
- Function: Refines previously processed holes to enhance dimensional accuracy and surface finish.
- Characteristics: Suitable for high-precision, large-diameter hole processing, effectively eliminating hole diameter deviations.
- Applications: Engine blocks, aerospace precision components, hydraulic cylinders.
5. CNC Turning Toolpath Types (for Lathe Machining)
CNC turning is mainly used for rotationally symmetric parts like shafts and disks. Common turning toolpaths include cylindrical turning, face turning, and inner hole turning.
5.1 Cylindrical Turning (Outer Diameter Turning)
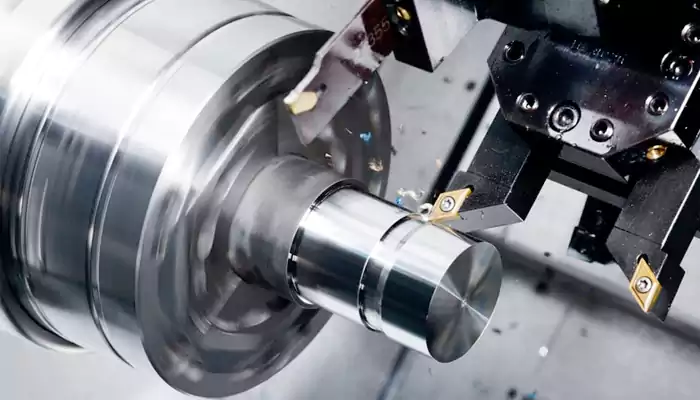
- Function: Removes material from the part’s outer diameter to achieve the desired shape and size.
- Characteristics: The tool cuts along the outer surface of the workpiece, suitable for both roughing and finishing.
- Applications: Shaft parts, transmission shafts, rollers, and cylindrical components.
5.2 Face Turning (Facing)

- Function: Processes the end face of parts to ensure flatness and dimensional accuracy.
- Characteristics: The tool feeds radially, typically used for initial shaping or final trimming of parts.
- Applications: Flanges, disc-shaped parts.
5.3 Inner Hole Turning (Inner Diameter Turning)
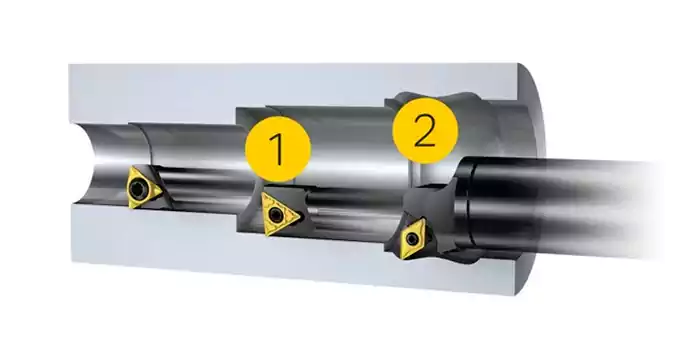
- Function: Processes internal hole diameters to ensure dimensional accuracy and surface quality.
- Characteristics: Suitable for thin-walled parts and high-precision internal hole machining, often refined with boring tools.
- Applications: Bushings, bearing housings, hydraulic cylinders.
6. How to Choose the Right CNC Toolpath?
Selecting the correct toolpath enhances machining quality, reduces costs, and boosts productivity. Factors to consider include the following:
6.1 Influence of Machining Materials on CNC Toolpath
Different materials require tailored toolpaths to optimize tool life and cutting performance:
Hard materials (e.g., titanium alloys, stainless steel):
High-Efficiency Dynamic Milling (HEM) is ideal for evenly distributing cutting load and reducing tool wear.
Soft materials (e.g., aluminum alloys, plastics):
High-Speed Machining (HSM) is more suitable to reduce cutting resistance and improve efficiency.
6.2 Path Planning for Complex Geometry
For parts with intricate shapes, selecting appropriate toolpaths is crucial for ensuring both accuracy and efficiency:
Complex 3D surfaces:
Use contour machining (Z-Level Milling) to maintain stable depth of cut and reduce machining errors.
Large flat surfaces:
Face Milling is recommended for rapid material removal and optimal surface finish.
Internal cavities:
Pocketing is used to cut in layers, improving material removal rates and reducing tool wear.
6.3 Balancing Productivity and Machining Accuracy
Striking the right balance between efficiency and precision is essential:
Roughing:
Focus on material removal rate, using high feeds and deep cuts (e.g., Helical Interpolation).
Finishing:
Prioritize surface quality and accuracy with smaller feeds and shallower cuts (e.g., Contouring).
Choosing the right toolpath optimizes machining processes, reduces cycle times, boosts overall productivity, and lowers costs, enhancing competitiveness.
7. Summary
Choosing the right CNC toolpath is key to precision, efficiency, and cost savings. With AI and smart manufacturing, toolpath optimization is becoming more automated, using big data and adaptive algorithms.
Many manufacturers now rely on intelligent CAM software to boost productivity, reduce costs, and ensure high-quality results. As technology evolves, optimized toolpaths will further enhance efficiency and innovation in manufacturing.