HOME << BLOG
Common Surface Treatment Processes
Surface treatment process is one of the processes we often encounter in the CNC machining process, today’s article will talk to you about what is the surface treatment, as well as in the machining of parts in the common types of surface treatment.
Ⅰ: What is surface treatment?
Surface treatment also named Surface finishing. It is a process of artificially forming a surface layer on top of a substrate material with mechanical, physical and chemical properties different from those of the substrate. The purpose is to meet the corrosion resistance, abrasion resistance, decoration or other special functional requirements of the product.
For metal casting products, we commonly used surface treatment methods are: mechanical grinding, chemical treatment, surface heat treatment, spray surface, surface treatment is the surface of the workpiece cleaning, sweeping, deburring, de-greasing, de-oxidizing and so on.
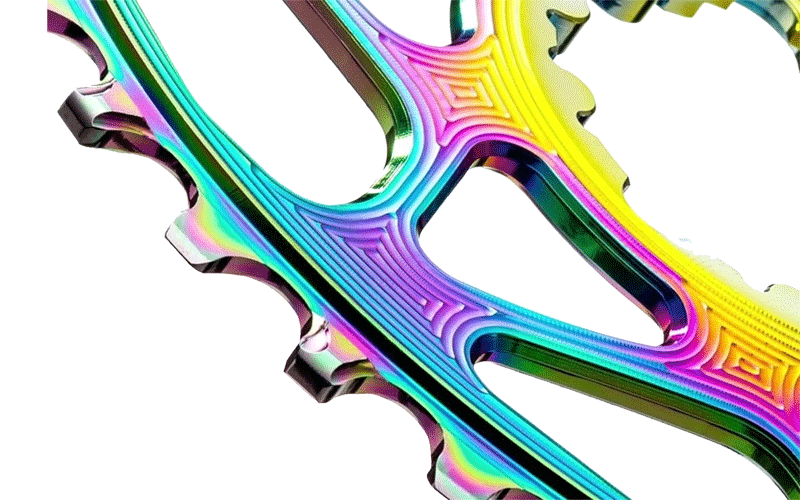
Ⅱ:6 common types of surface treatments that we often see in CNC machining:
1.Vacuum Metalizing
Vacuum Metalizing also calld Vacuum plating,Vacuum plating is a physical deposition phenomenon. That is, in a vacuum state injected argon, argon impact target, target separation into molecules by the conductive goods adsorption to form a layer of uniform and smooth imitation of the metal surface layer.
Applicable materials: metal, hard and soft plastics, composite materials, ceramics and glass. The most common surface treatment used for electroplating is aluminum, followed by silver and copper.
Process Costs: During vacuum plating, workpieces need to be coated, loaded,unloaded
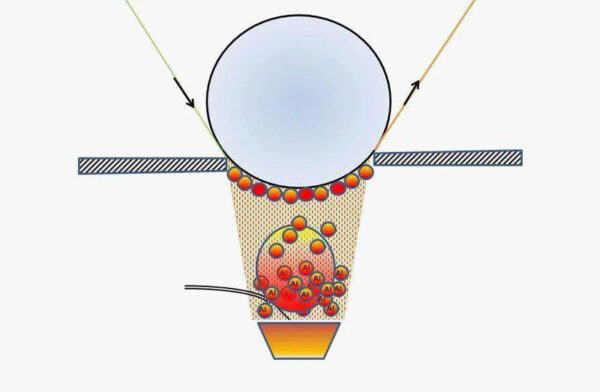
and re-coated, so labor costs are quite high, but also depend on the complexity and number of workpieces.
Environmental impact: Vacuum plating has very little environmental pollution, similar to the impact of spraying on the environment.
2.Electropolishing
Electropolishing is an electrochemical process in which the atoms of the workpiece submerged in an electrolyte are converted into ions and removed from the surface due to the passage of electric current, thus achieving the effect of removing fine burrs and increasing the brightness of the workpiece surface.
Applicable materials: most metals can be electrolytic polishing, which is most commonly used in stainless steel surface polishing (especially for austenitic nuclear grade stainless steel).
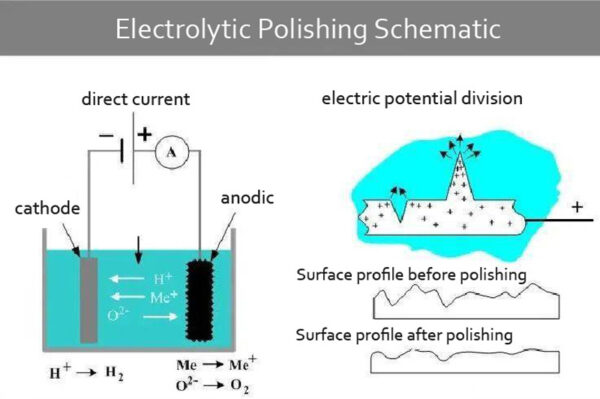
Process Cost: The whole process of electrolytic polishing is basically completed by automation, so the labor cost is very low.Environmental impact: electrolytic polishing using less harmful chemicals, the whole process requires a small amount of water and simple operation, in addition to extend the properties of stainless steel, stainless steel to delay the role of corrosion.
3.Galvanizing process
The surface of steel alloy material is coated with a layer of zinc in order to play the role of beauty, rust prevention and other surface treatment technology, the surface of the zinc layer is a kind of electrochemical protection layer, which can prevent the metal from decaying, the main methods are hot-dip galvanizing and electro-galvanizing.
Applicable :Since the galvanizing process relies on metallurgical bonding technology, it is only suitable for surface treatment of steel and iron.
Process costs: no tooling costs, short cycle time / medium labor costs, as the surface quality of the workpiece depends largely on the manual surface treatment prior to galvanizing.
Environmental impact: Since the galvanizing process increases the service life of steel
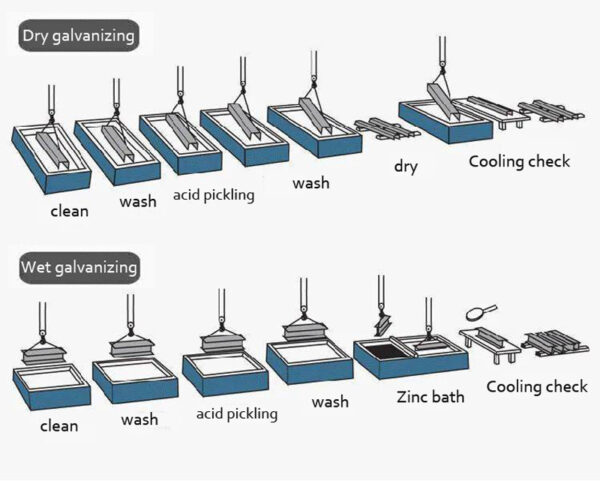
and iron parts by 40-100 years and prevents rust and decay of the workpieces very well, it has a positive effect on the protection of the bad environment. In addition, zinc-coated workpieces can be returned to the galvanizing bath after their service life has expired, and the repeated use of liquid zinc produces no chemical or physical waste.
4. Electroplating process
The use of electrolysis to make the surface of the parts attached to a layer of metal film process, thus playing a role in preventing metal oxidation, improve wear resistance, electrical conductivity, reflectivity, corrosion resistance and enhance the role of aesthetics, etc., many of the outer layer of the coin is also plated.
Applicable materials: Most metals can be plated, but different metals have different levels of purity and plating efficiency.
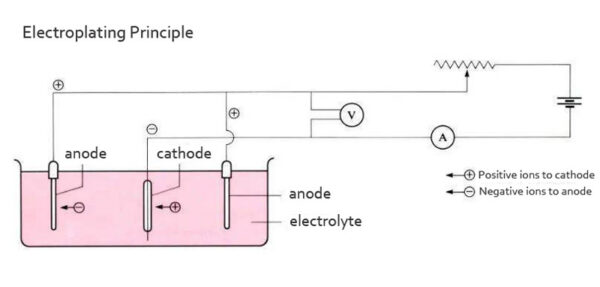
The most common are: tin, chromium, nickel, silver, gold and rhodium (nickel cannot be used for plating products that come into contact with the skin because nickel is irritating and toxic to the skin).
Process Costs: No tooling costs, but jigs are required to hold the parts in place / Time costs depend on the temperature and type of metal / Labor costs (medium-high) depending on the specific type of plated part, e.g. plating of silverware and jewelry requires an extremely high level of skilled labor to operate because of the high demand for appearance and durability.
Environmental impact: A large number of toxic substances are used in the plating process, so specialized triage and extraction is required to ensure minimal environmental impact.
5.Anodization Anodic Oxidation
Anodization is also called Anodic, OxidationAnodic oxidation, mainly of aluminum, is the use of electrochemical principles to generate a layer of Al2O3 (aluminum oxide) film on the surface of aluminum and aluminum alloys. This oxide film has special characteristics such as protective, decorative, insulating and wear-resistant.
Applicable materials: aluminum, aluminum alloy and other aluminum products
Process Costs: The consumption of water and electricity during the production process is quite large, especially in the oxidizing process. The heat consumption of the machine itself, which needs to be cooled down constantly with circulating water, often consumes about 1000 degrees per ton of electricity.
Environmental impact: Anodizing is not considered to be outstanding in terms of energy efficiency, while in aluminum electrolysis production, the anode effect also produces gases that have a damaging side effect on the ozone layer of the atmosphere.
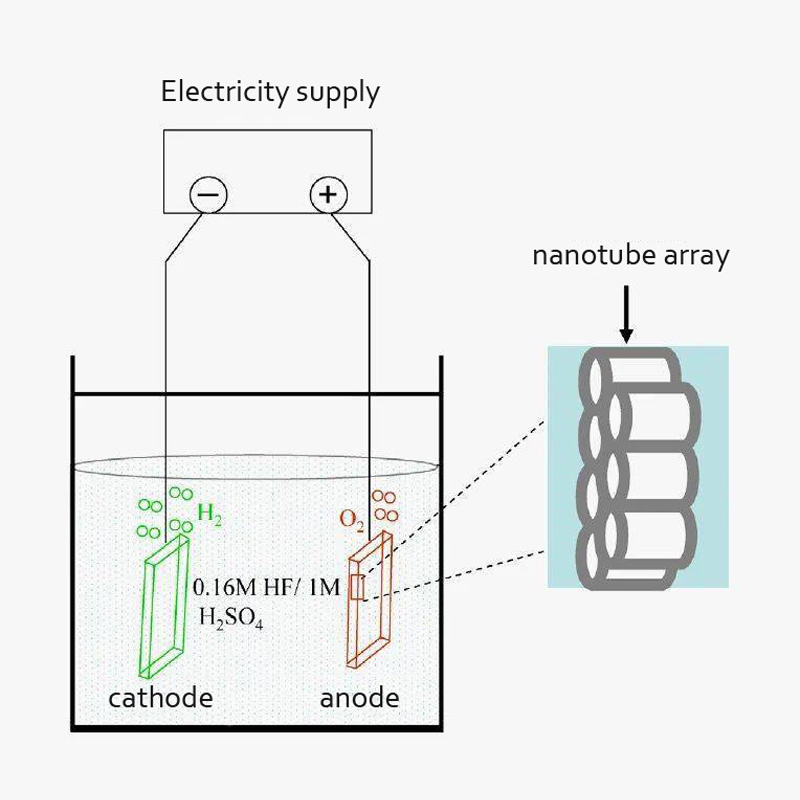
6.Spray
Spray is through the spray gun or disc atomizer, with the help of pressure or centrifugal force, dispersed into uniform and fine droplets, applied to the surface of the coating method. General spraying is divided into two processes, shot blasting and sand blasting, shot blasting that is, the use of pellets bombard the surface of the workpiece and implant residual compressive stress, to enhance the fatigue strength of the workpiece cold process.
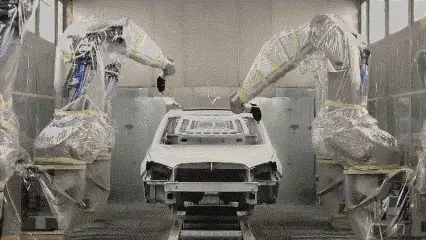
Sandblasting is the use of high-speed sand flow impact cleaning and roughening the surface of the substrate process, that is, the use of compressed air as a driving force to form a high-speed jet beam will be sprayed (copper ore, quartz sand, emery, iron sand, Hainan sand) high-speed jet to the need to deal with the surface of the workpiece, so that the surface of the workpiece surface of the outer surface of the exterior surface or the shape of the change.
Ⅲ:Summarize
In addition to the 6 surface treatment processes frequently encountered in CNC machining introduced in this article, in fact, there are many kinds of surface treatment processes, such as electrophoresis, micro-arc oxidation, PVD vacuum plating, metal brushing, laser engraving and so on.
