Aerospace parts manufacturing
Customized machining services for aerospace parts
- Source Factory
- No minimum order
- Custom Finishes
- Quick Turnaround
- Long after-sales service
Market Overview of Aerospace Parts Machining
As the global aerospace industry grows exponentially, the need for advanced materials, precision manufacturing techniques and customized designs continues to rise.
Customers such as aircraft manufacturers, spacecraft developers, and defense contractors need to provide customized parts for all types of aerospace equipment to ensure long-term reliable operation in extreme environments such as high temperatures, high pressures, and severe vibrations.
Custom machining has become an integral part of the aerospace parts supply chain.In the future, with the development of high-end manufacturing, the customization of industrial machinery parts will be more diverse and technical requirements.
AlliedMetal is always committed to providing customers with the highest quality customized aerospace parts services, helping the global aerospace industry to continue to innovate and develop.
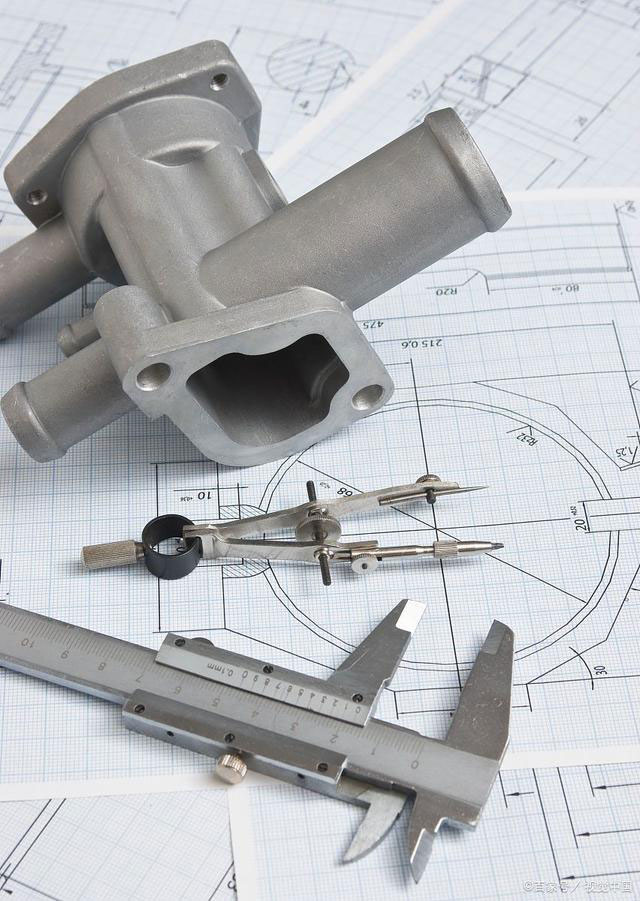
Why Customize Aerospace Parts?
Extreme Environmental Requirements
Aerospace equipment operates under extreme conditions such as high temperatures, strong pressures, and vacuums, so parts must be highly resistant and reliable.
High Precision Requirements
Aerospace parts need to be designed and manufactured with extreme precision to ensure error-free operation in complex environments.
Personalization and Material Selection
Customized parts allow the design to be adapted to specific needs and the selection of the right material to meet different environmental challenges, such as weight reduction, corrosion resistance or tolerance to extreme temperatures.
Performance Optimization
Through customization, part performance can be optimized for specific functions, such as reducing weight or increasing structural strength, which is often not possible with standard parts.
Beyond the limitations of generic parts
While generic parts are often unable to meet the stringent requirements of aerospace equipment, customized parts can provide precise solutions for specific mission needs.
What aerospace parts can be customized?
Such as blades, turbines, bearings, integral lobe disk structures and magazines.
Small, medium and large aircraft structural parts for wings, fuselage, tail, landing gear and aero-engines, and other core critical parts. Such as frames, housings, fasteners.
For example: aviation controller bracket, display housing bracket, machine instrument panel, navigation bracket, etc.
Including processor, gyroscope, barometer, geomagnetometer, GPS, etc.
Includes aerospace parts such as front wheels, struts, dampers, steering gears, swing reducers, brakes, retracts and guards, steering gears, and more.
Such as airline seats and cabin fittings, – Navigation and communication equipment housings, etc.
Benefits of customized aerospace parts
- Highly accurate:
Custom machining ensures that the shape, size and performance of the part meets strict aerospace standards. - Material Optimization:
Optimal materials are selected for specific usage scenarios, such as high temperature, corrosion resistance or lightweight materials. - Increased functionality:
Custom designs can optimize the functionality of a part for more efficient performance. - Compliance with special specifications:
Compliant production for industry standards in different countries and regions. - Design Flexibility:
Reduce product development time and costs with rapid iteration and prototype testing based on design requirements.
Materials Commonly Used for Aerospace Parts Processing
Name | Features | Strength | Corrosion Resistance | Weight | Main Applications |
Titanium Alloys | High Strength, High Temperature, Corrosion Resistant | High | High | Light | Body, engine components, fasteners |
Aluminum Alloys | Lightweight, easy to machine, corrosion-resistant | Medium | Medium | Light | Structural Components, Electronic Equipment Housings |
Stainless Steel | High Strength, Abrasion Resistant, Corrosion Resistant | High | High | Heavy | Landing gear, fuel system components |
Nickel-based alloys | Ultra-high temperature and corrosion resistance | Extremely high | High | Heavy | Turbines, engine combustion chambers |
Carbon fiber composites | Ultra-light, high strength, corrosion resistant | High | Medium | Extremely light | Wing, cabin structure |
Common Machining Methods for Aerospace Parts
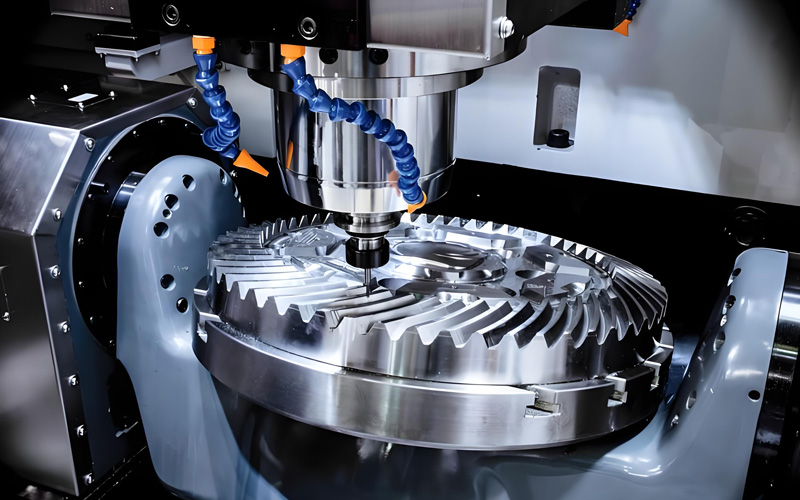
Through precise control, CNC machining can realize the processing of complex shapes and high-precision parts, which is suitable for critical parts such as aero-engine components.
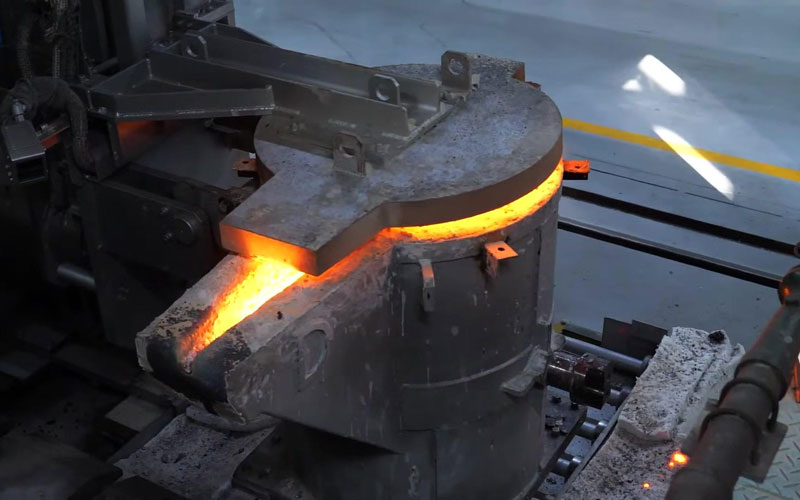
Casting technology is suitable for mass production, capable of molding complex shapes in one go, and is usually used to produce large or structurally complex aerospace components.
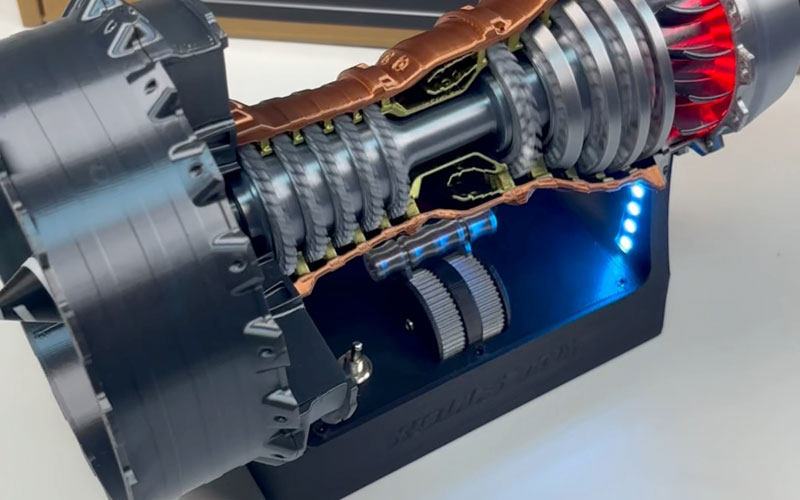
Additive Manufacturing (3D Printing) enables the rapid manufacture of complex prototypes or low volume production parts, suitable for lightweight and complex shaped components.
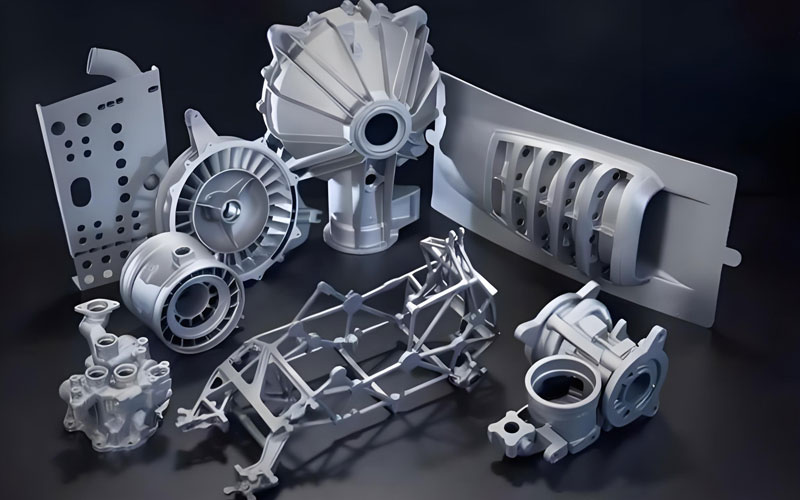
Rapid prototyping technology shortens the development cycle and enables rapid production of high-precision prototype parts during the design verification stage, facilitating design iteration.
Why choose AlliedMetal for custom aerospace parts?
Extensive Experience
AlliedMetal has years of experience in custom machining of aerospace parts and is capable of handling complex, high-precision projects.
Advanced Equipment
We use state-of-the-art CNC machining, 3D printing and rapid prototyping equipment to ensure efficient production and consistent quality.
Professional Team
AlliedMetal has a professional team of engineers and technicians who can provide full-process technical support according to customer needs.
Global Service
We provide customized services to our global customers, strictly adhering to aerospace standards and regulations everywhere.
Manufacturing Quality and Compliance Assurance
AlliedMetal strictly adheres to international aerospace standards (e.g. AS9100, ISO 9001) during the part manufacturing process and has passed several quality certifications to ensure that each part meets the stringent requirements of the aerospace industry.
At the same time, our production process is monitored from start to finish to ensure optimal quality at every stage, from design to delivery.
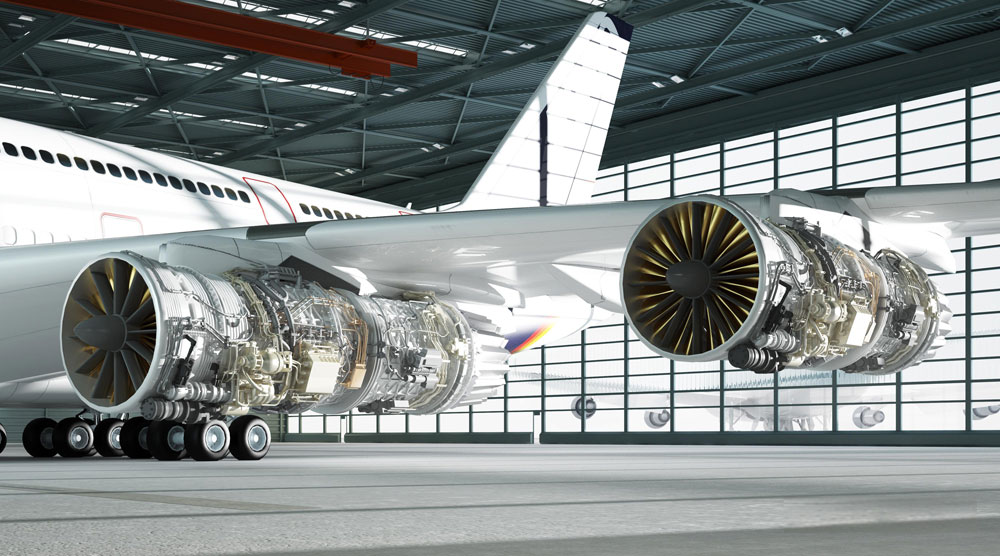
Examples of aerospace parts we've done
We have customized high-strength titanium alloy turbine blades and produced lightweight carbon fiber wing parts for an internationally renowned aero-engine manufacturer. We have also developed high-precision aluminum alloy frames and structural components for military drones.
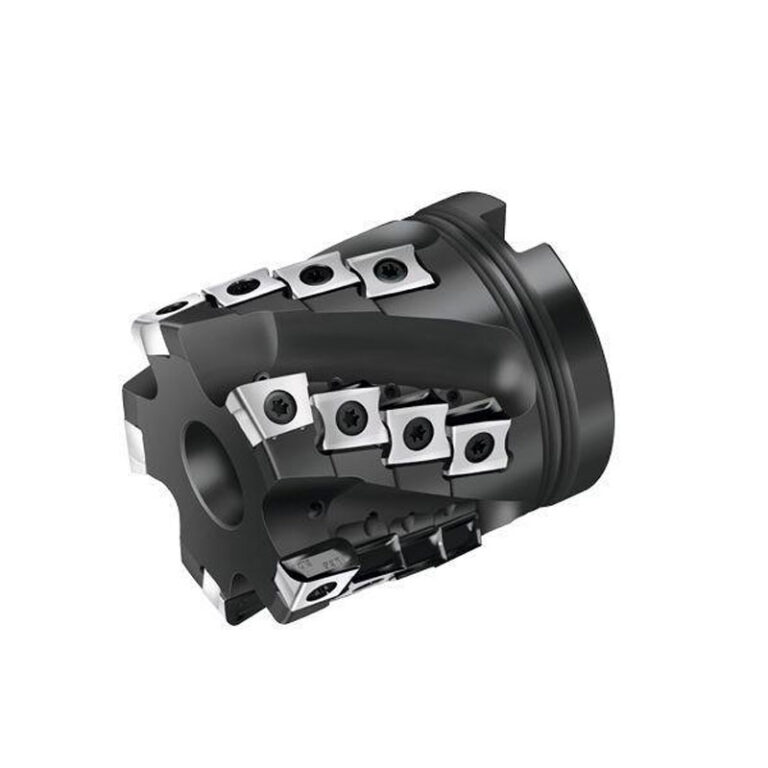
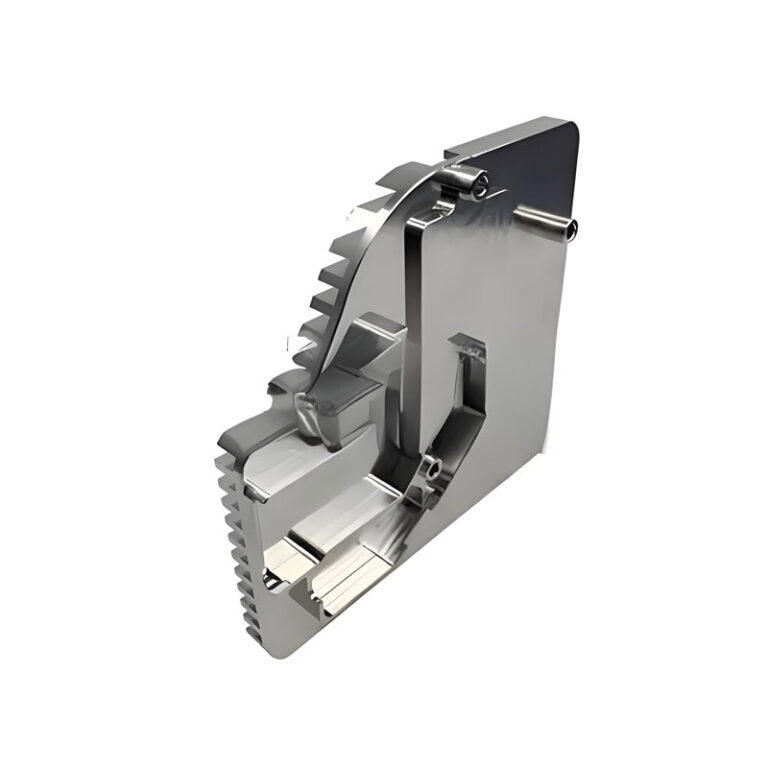

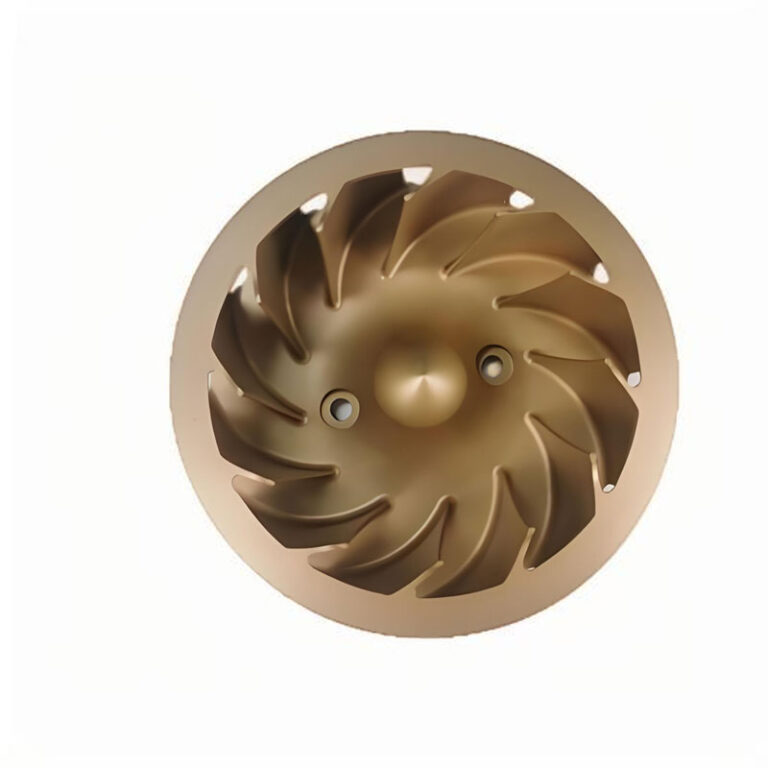
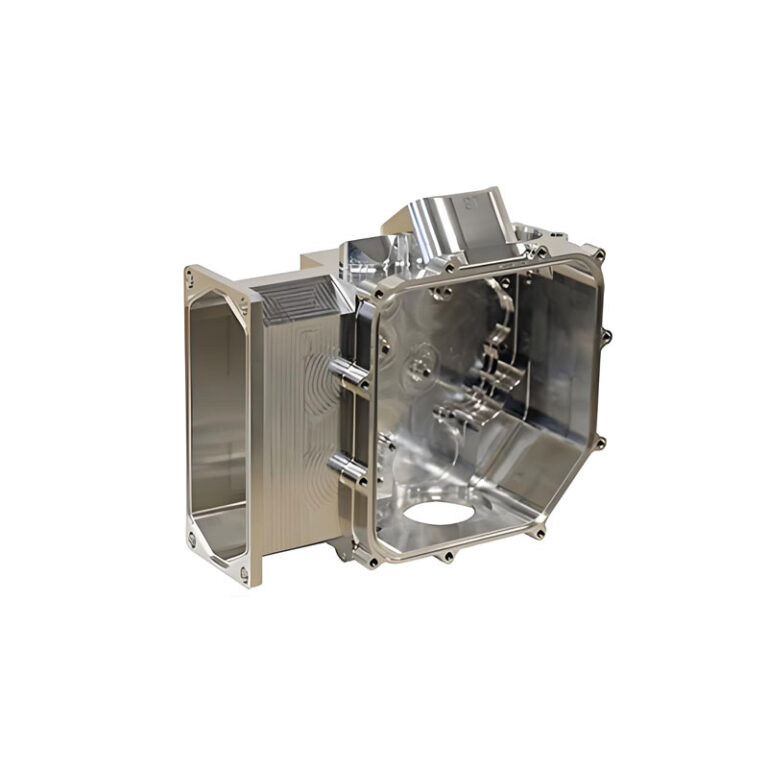

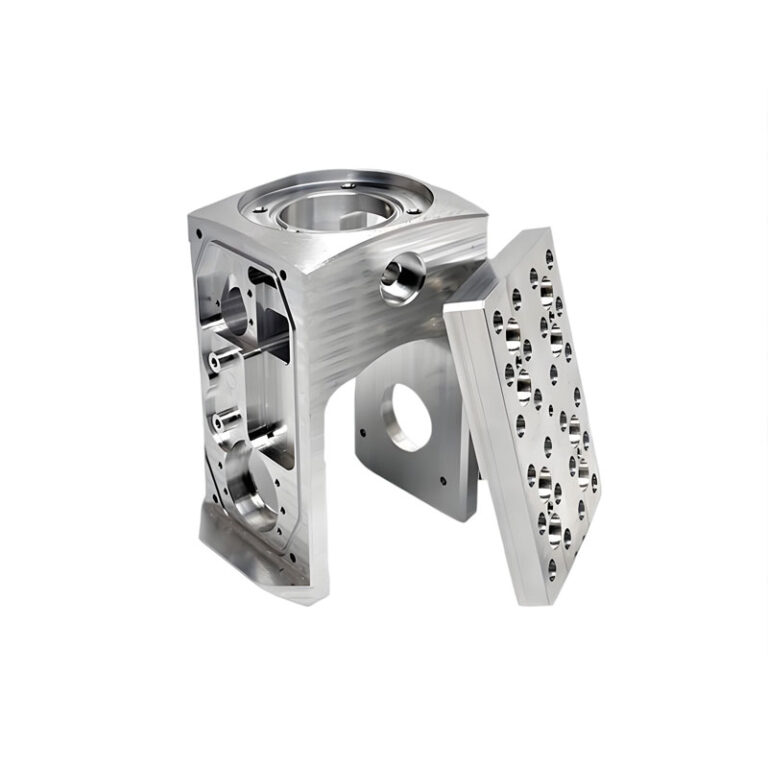
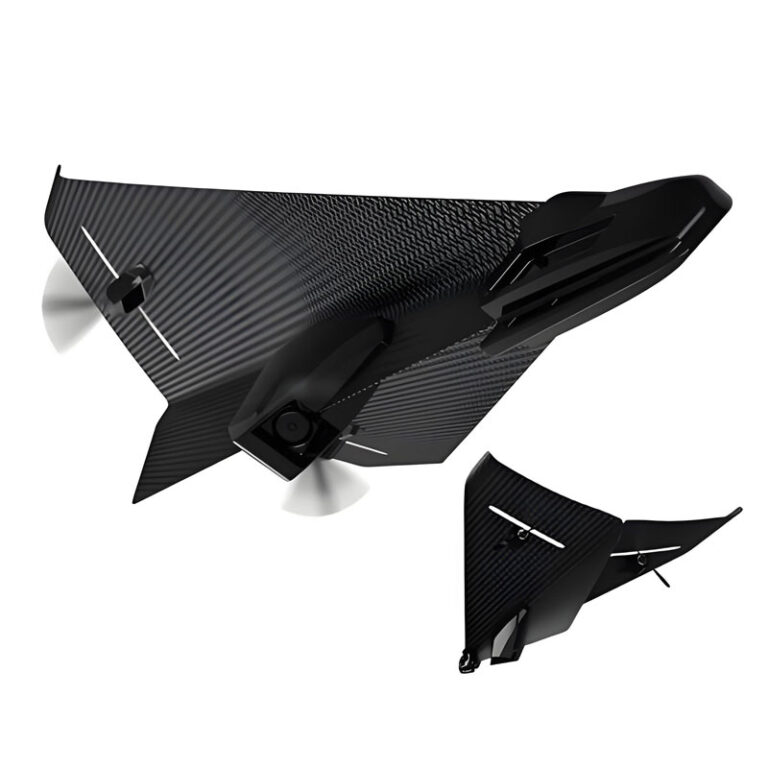
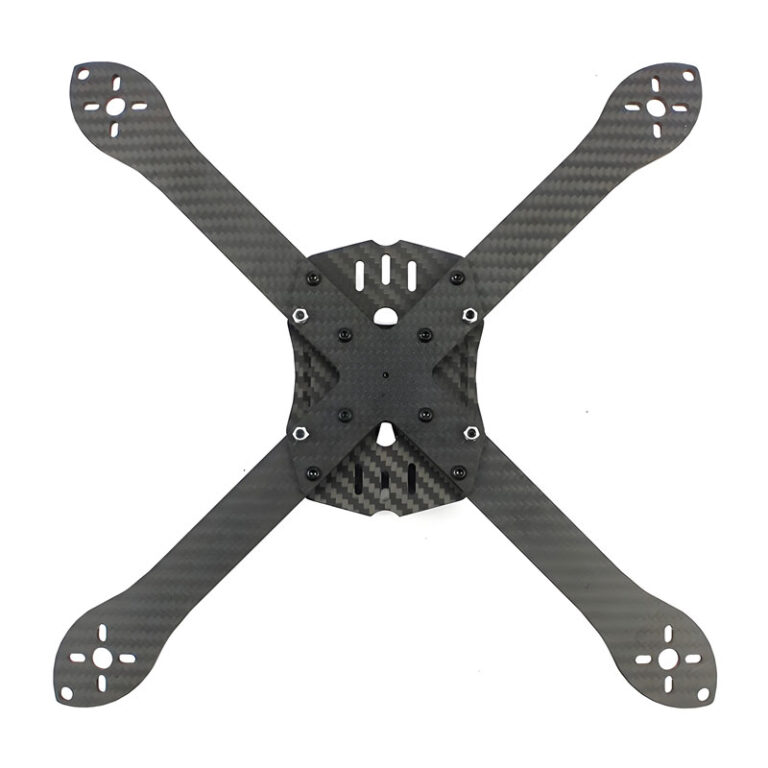


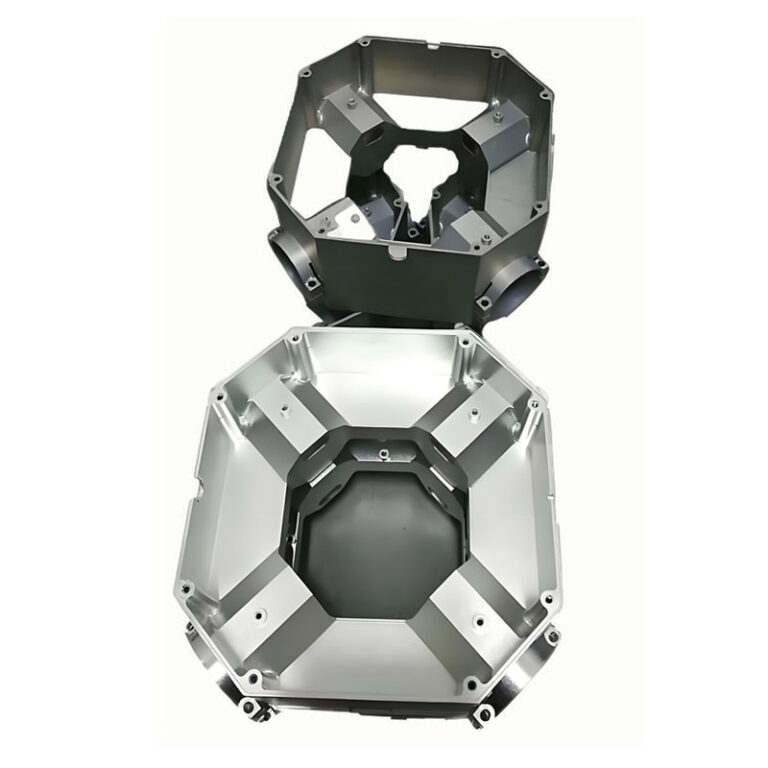
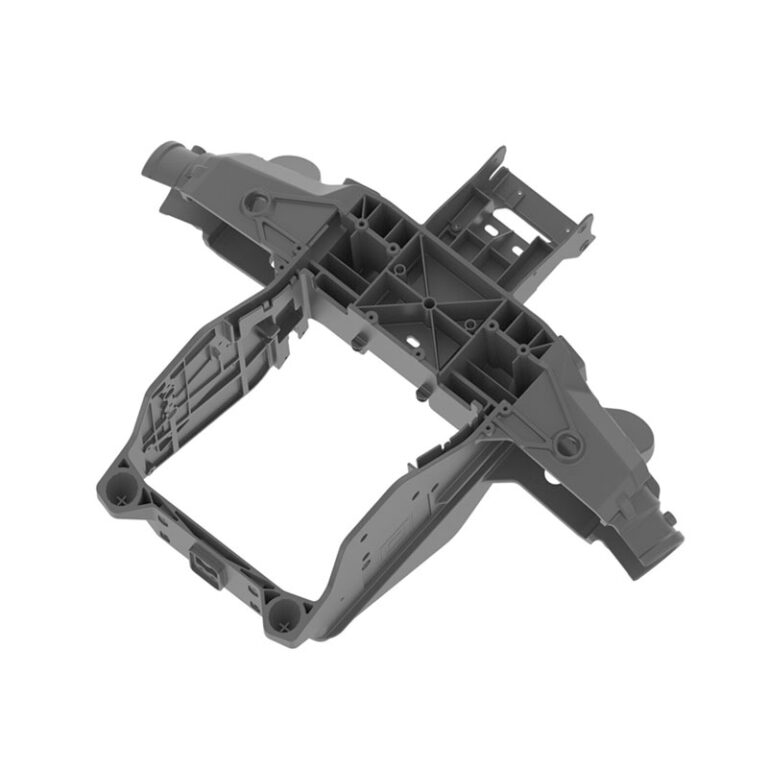
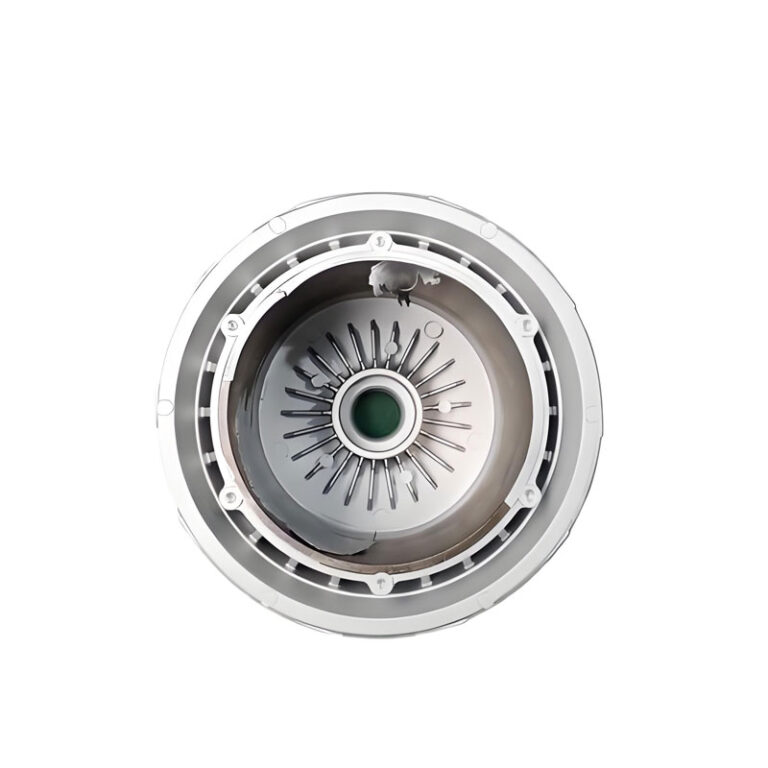
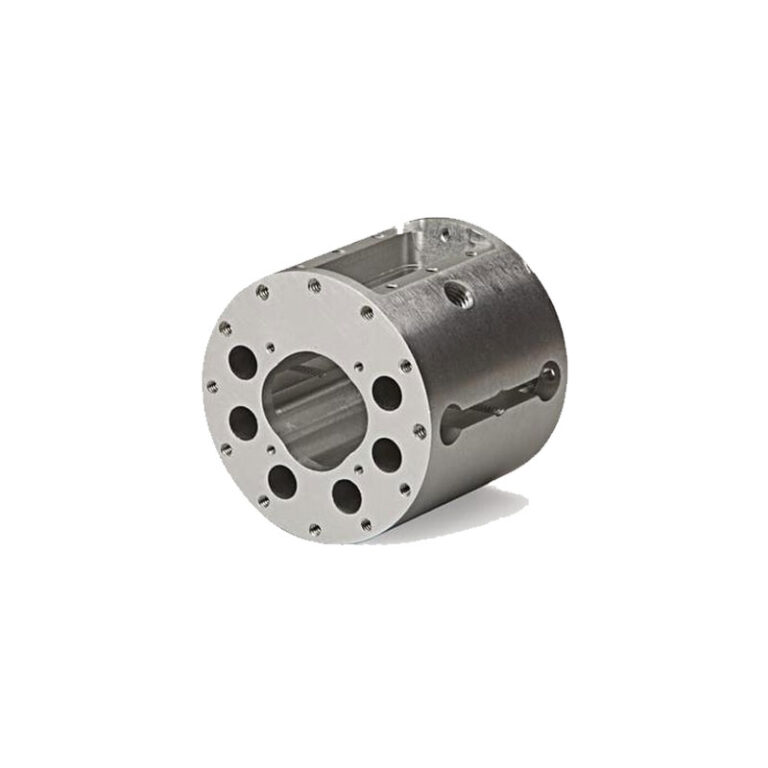


Future trends in aerospace parts manufacturing
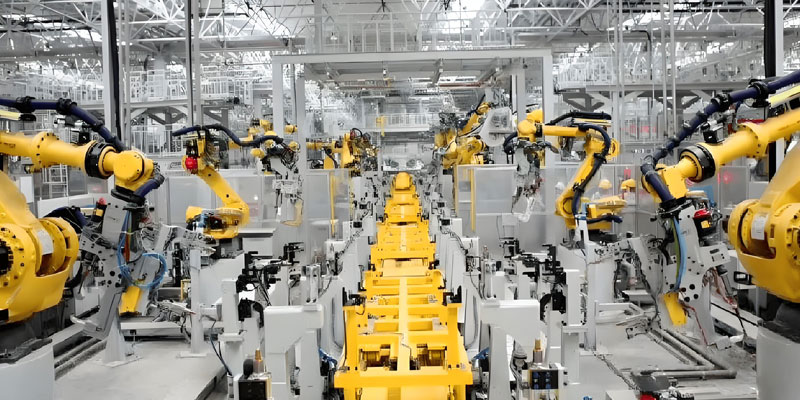
Intelligent Manufacturing
In the future, there will be greater reliance on automation and intelligent technologies to improve production efficiency and quality control.
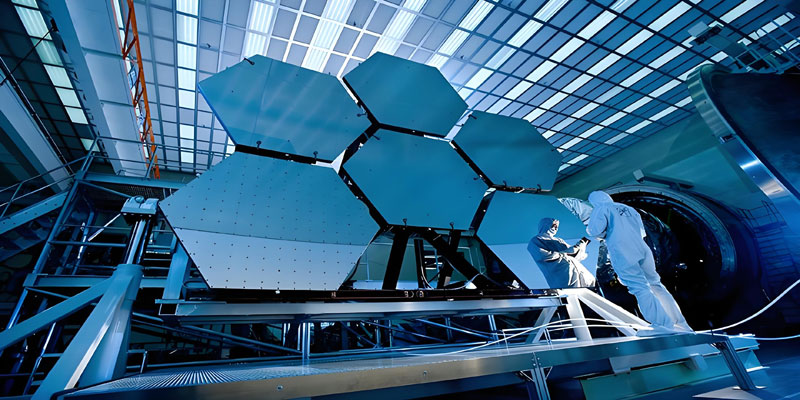
New Material Application
New materials that are lightweight and ultra-high temperature resistant will further enhance the performance and energy efficiency of aircraft.
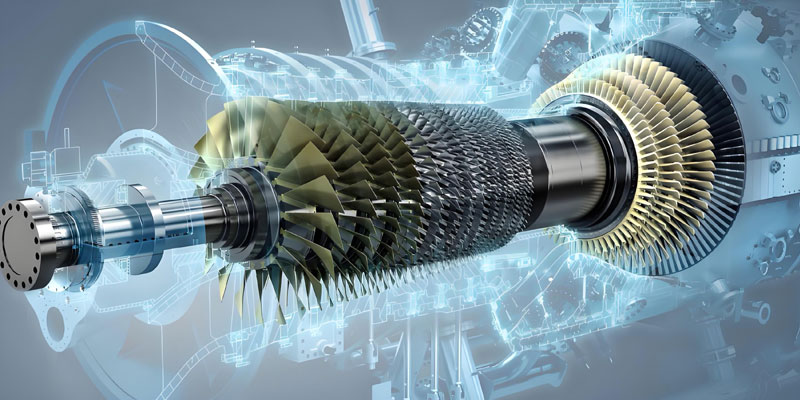
Additive Manufacturing
The application of 3D printing technology will continue to expand, enabling rapid manufacturing and customized production of complex parts.
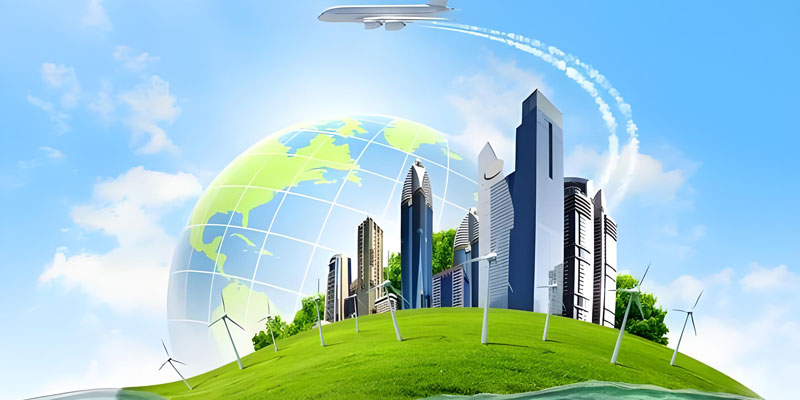
Green Sustainability
In the future, more emphasis will be placed on environmentally friendly materials and green processes to reduce pollution and resource consumption.
FAQ
Delivery time depends on project complexity and batch size. Typically, the lead time after design confirmation is 4-8 weeks.
Yes, we support different needs from single-piece prototypes to high-volume production.
Yes, we can use specific materials according to customer needs and provide relevant material testing reports.
We use advanced CNC equipment and inspection tools to ensure that parts meet design tolerances and comply with international aviation standards.