Precision Medical Parts
Customized machining services for precision medical parts
- Source Factory
- No minimum order
- Custom Finishes
- Quick Turnaround
- Long after-sales service
The Demand and Future of Precision Medical Component Machining
There is a growing demand for precision parts for medical devices, especially for minimally invasive surgery, diagnostic instruments and implants. With the development of technology and the rise of personalized medicine, the demand for customized precision medical parts will continue to climb in the future, driving the evolution of medical devices to higher standards.In the future, with the development of high-end manufacturing, the customization of industrial machinery parts will be more diverse and technical requirements.
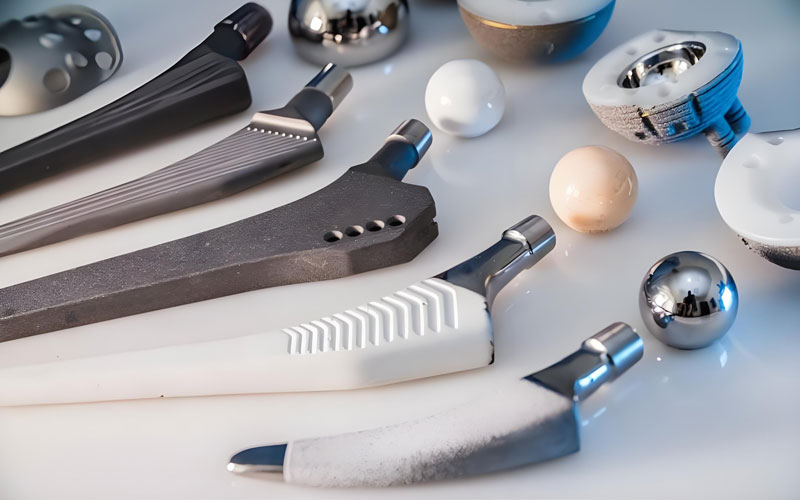
Why customize precision medical parts?
Customized industrial machinery parts are widely used in the following industries:
Special size and shape:
Medical devices are so diverse that standard parts cannot fully meet specific needs.
Higher Precision Requirements
The medical field requires a high degree of precision for equipment parts, and customized processing can ensure the precision and consistency of the parts.
Material Adaptability
Different medical applications require different materials for accessories, and customization can be used to select the most suitable material according to the application.
Demand for innovation
With the innovation of technology, many medical device designs require customized new accessories.
Transportation
The manufacture of automobiles requires a large number of mechanical parts, including engines, drivetrains, brakes and suspension systems. Other modes of transportation such as trains, boats, and motorcycles also rely on custom parts.
What precision medical parts can be customized?
Examples include scalpels, scissors, complex robotic arms, etc.
Including dirty pacemakers, artificial joints (such as hip and knee replacements), dental implants, etc.
CNC machining centers can customize prosthetics and orthotics to a patient’s physical characteristics using 3D scanning and CAD modeling technology, which can ensure perfect fit and functionality.
Like ventilators, ultrasound equipment, medical imaging equipment, and even rehabilitation equipment and lab equipment, customizable parts are not limited to housings, brackets, circuit boards, sensors, and more.
Including but not limited to catheters, guidewires, balloon dilators, stents, hemostats and vascular closure devices.
Types that can be customized include pressure sensors, temperature sensors, and other types of sensors.
Customizable surgical robot end fittings, minimally invasive surgical medical and surgical instrumentation micro parts, as well as gears, bearings, drives, and other parts.
What are the benefits of customized precision medical parts?
- Higher precision and consistency: Ensure that each accessory meets strict medical standards.
- More flexible material selection: suitable materials can be selected according to specific needs, such as titanium, stainless steel and plastic.
- Shorten the R&D cycle: Quickly respond to design changes and speed up product launch.
- Personalized customization: Meet the individual needs of special medical devices or patients.
- Compliance with industry standards: Ensure that each customized accessory meets medical certifications and standards.
Precision medical parts requirements for processing materials
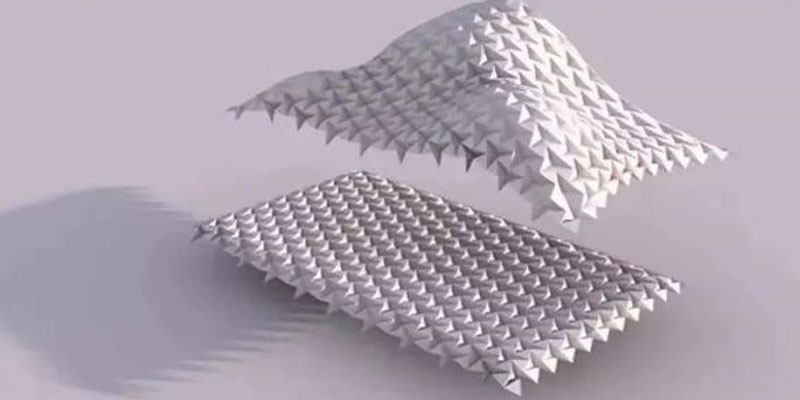
Biocompatibility
The material must be non-toxic, non-irritating and compatible with human tissue.
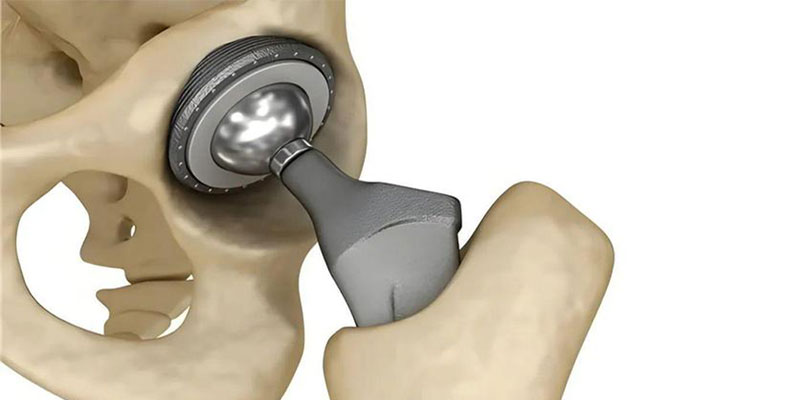
Corrosion resistance
Prevent corrosion in the body or in harsh environments.
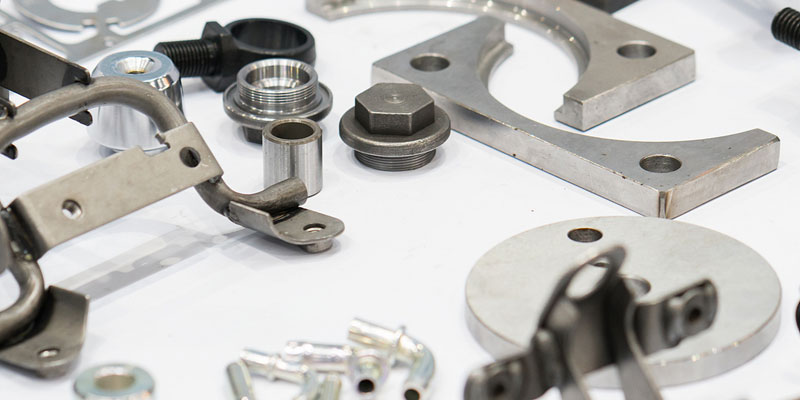
High strength and toughness
Ensure that it will not be damaged or deformed during surgery and use.

Antimicrobial
Reduce the risk of infection, especially in implantable accessories.
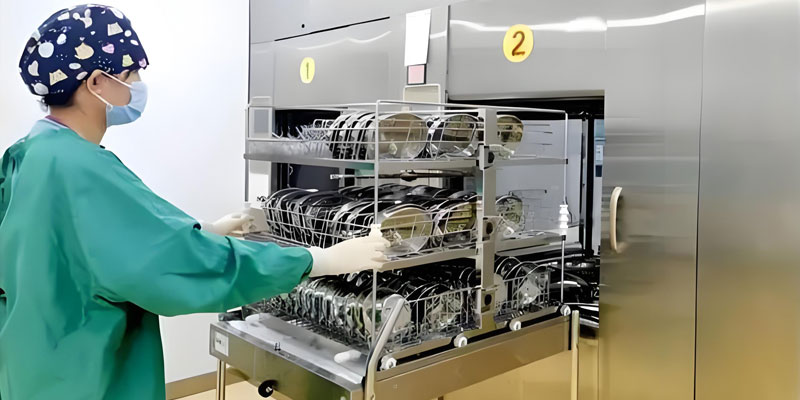
High temperature resistance
Parts that need to be sterilized at high temperatures.
Common Machining Methods for Precision Medical Parts
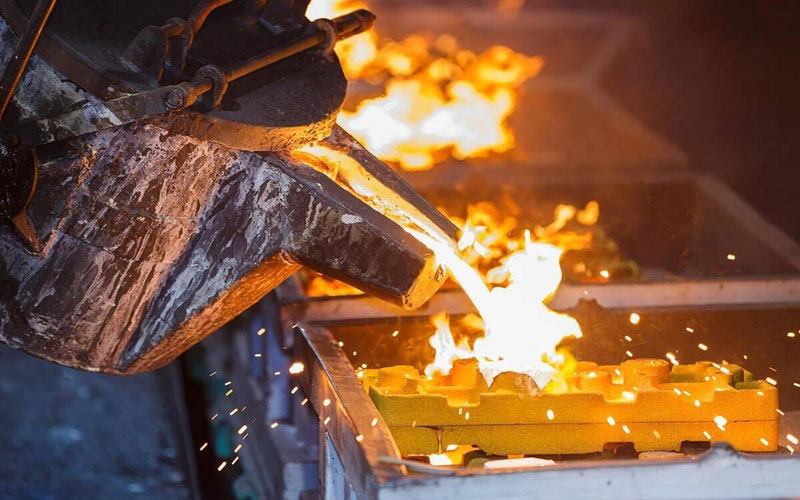
Used to manufacture parts with complex shapes, especially suitable for materials such as titanium.

Rapid production of prototypes or small batches of parts, especially for complex designs.
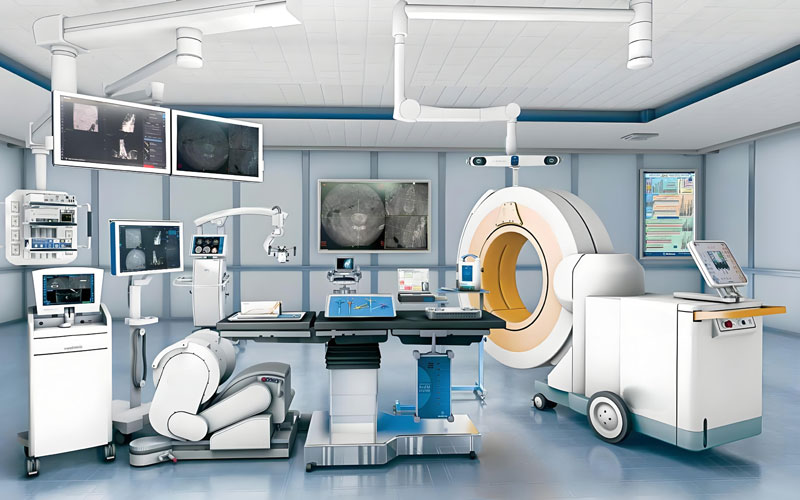
Helps medical device manufacturers quickly validate designs and conduct functional tests.
Why choose AlliedMetal for customized precision medical parts?
Rich industry experience
Years of experience in customizing medical equipment parts, familiar with the special needs of the medical industry.
Machining capabilities
Our state-of-the-art equipment and team are capable of handling demanding medical-grade parts processing.
Diversified Material Selection
Our strong cooperation network can provide a wide range of medical standard compliant materials for your reference.
One-Stop Service
From design to production, we offer complete solutions to ensure efficient and seamless integration.
Strict Quality Control
We are strict at every step to ensure that the quality of our products meets the highest standards.
Precision medical parts cases we have done
We have successfully customized minimally invasive surgical tools, titanium implants, sensor parts for diagnostic equipment, and micro instruments for interventional surgery, etc., and gained good reputation from our partners.
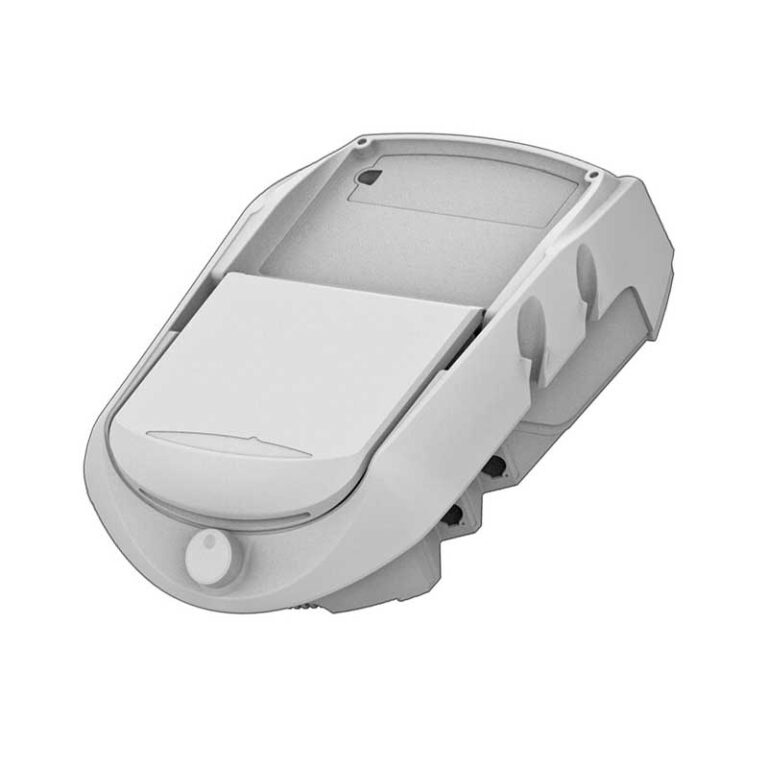

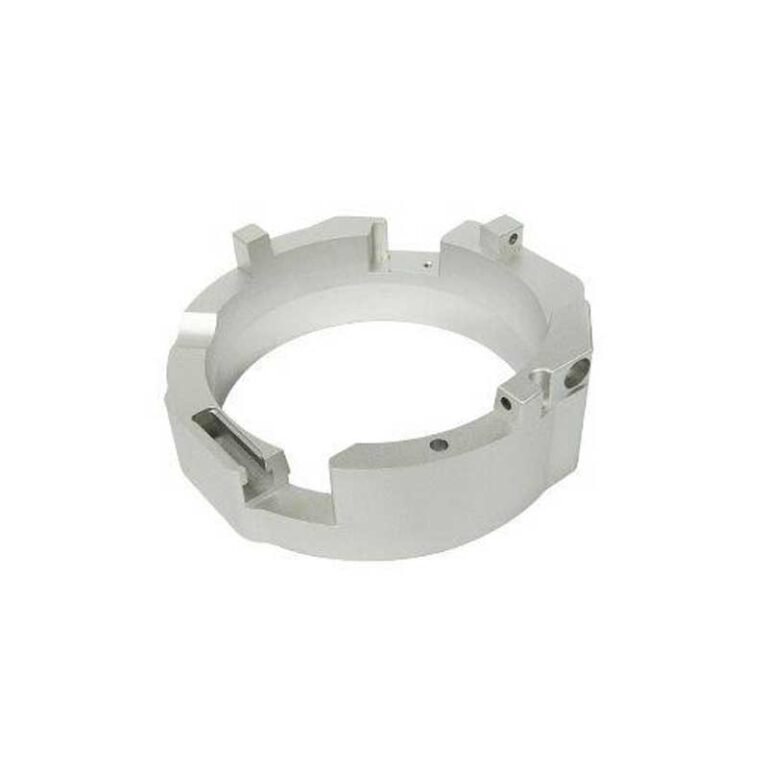
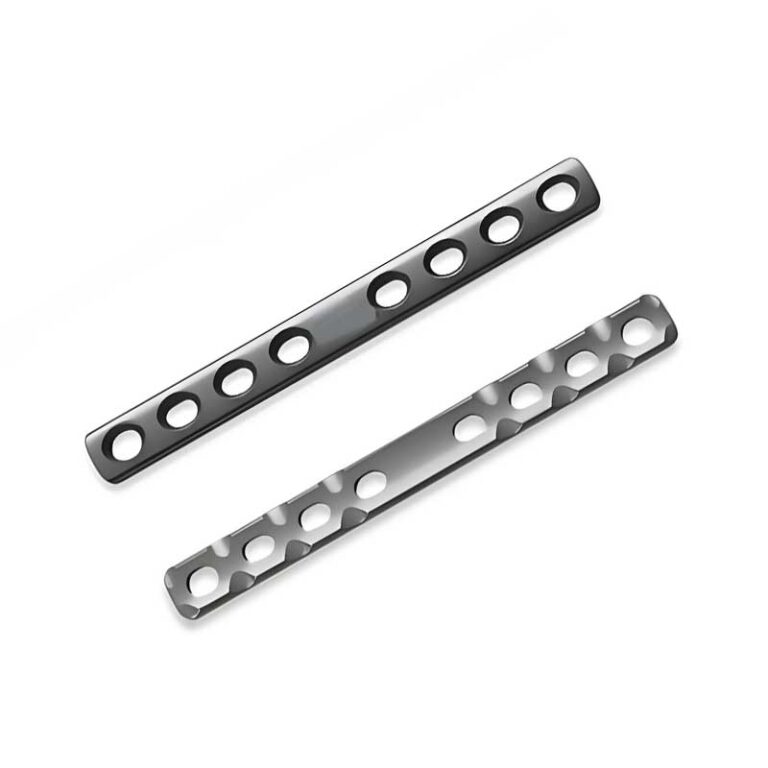
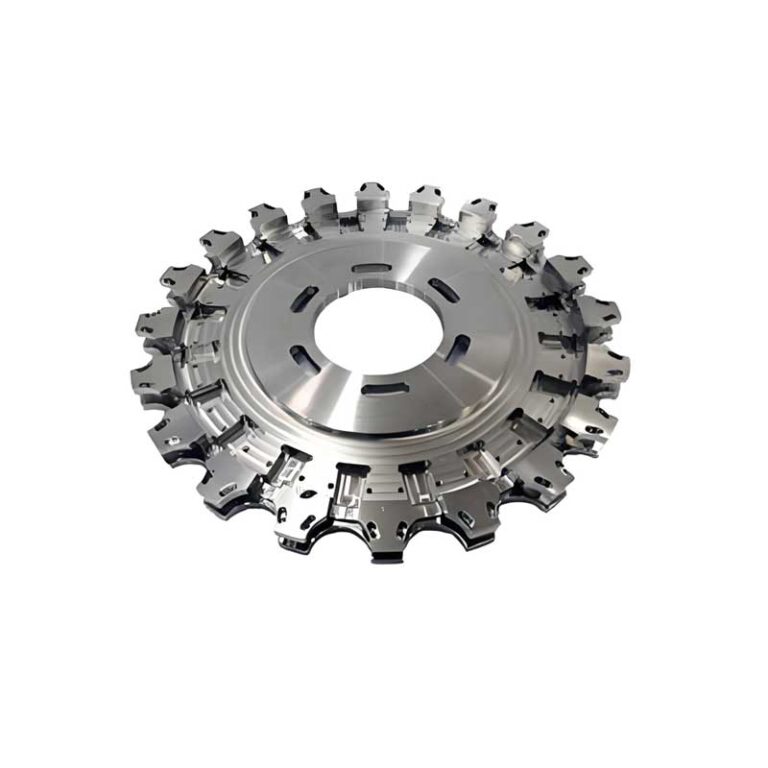

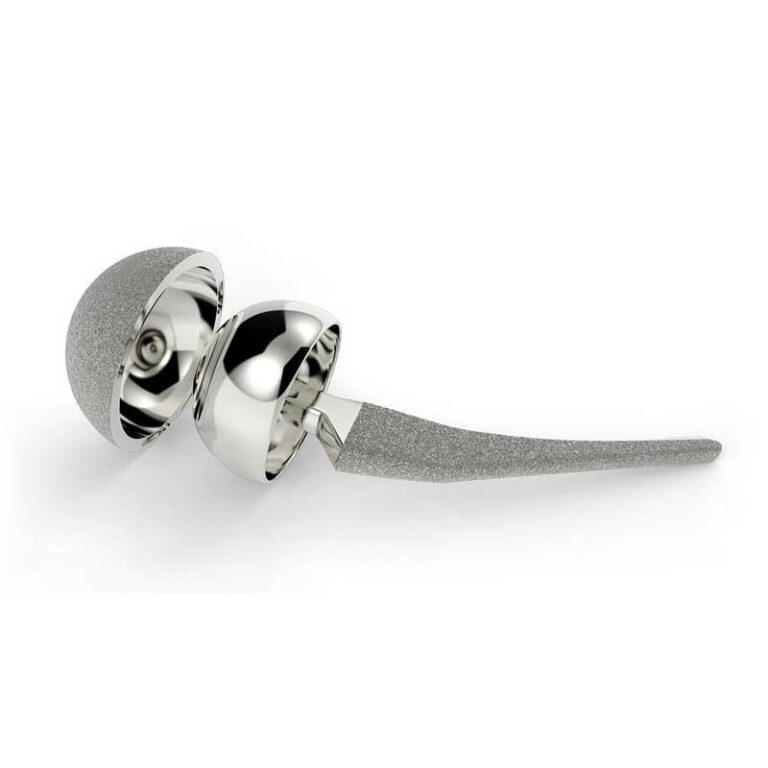
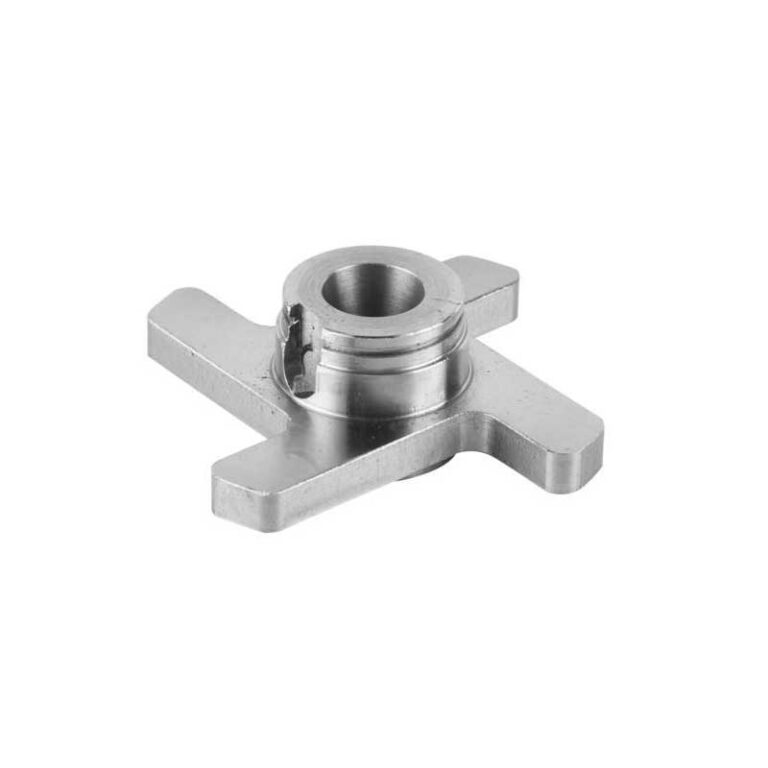
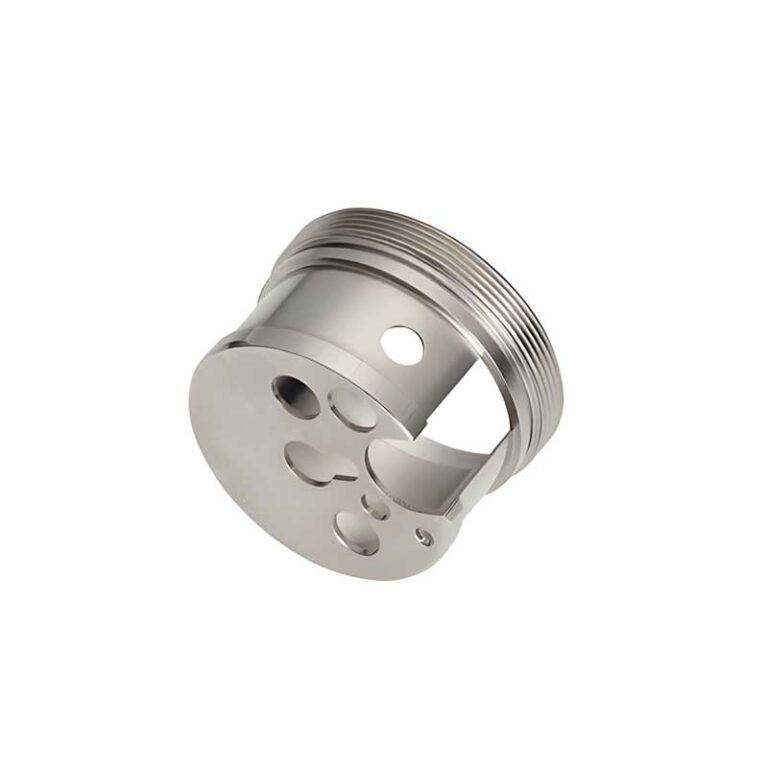


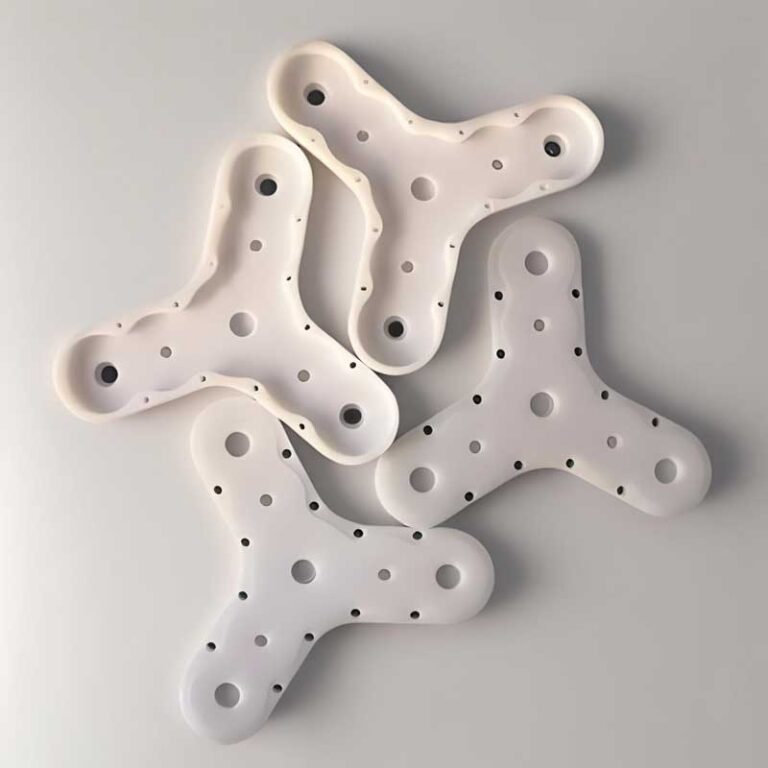
FAQ
Delivery time depends on project complexity and materials required. Usually within 2-6 weeks.
We can process a wide range of materials, including stainless steel, titanium, and plastic, to ensure compliance with medical device requirements.
We strictly follow medical device standards such as ISO 13485, and all parts undergo precision testing and quality control.
Yes, we offer rapid prototyping services to help customers validate design and functionality.