Materials
Cast iron parts machining
High-performance CNC machining services for cast iron parts!
- Source Factory
- Reasonable price
- Certified Materials
- Timely delivery
Our Cast Iron Parts Machining Services
With many advantages, we provide our customers with high-precision and high-quality cast iron parts, ensure on-time delivery, and help you improve the competitiveness of your products.
- 20+ years experience:
With more than 20 years experience in cast iron parts machining, we have mature technology and reliable service. - Own Factories & Advanced Equipment:
Two own factories and more than 200 modern equipments ensure efficient and accurate machining. - Full machining capability:
We specialize in processing gray cast iron and ductile cast iron with advanced technology and high precision to meet various needs. - Precise and efficient process:
Optimized machining process ensures precision at every step and smooth transformation from casting to parts. - Fast delivery and professional service:
Provide fast delivery and full support to meet customized and urgent order requirements.
Commonly Machined Cast Iron Parts
Cast iron is commonly used to make the following parts, and is especially suited for components that require high strength, wear resistance, and vibration dampening properties:
- Gears
- Bases
- Pulleys and Bushings
- Engine blocks
- Support frames
- Brake discs
- Pipe connectors
- Others
Characteristics of cast iron
- High strength and hardness:
Cast iron has high strength and hardness and is suitable for bearing mechanical loads. - Wear resistance:
Cast iron is a reliable wear-resistant material, especially suitable for heavy loads and long running parts. - Fast machining:
Cast iron can be machined faster than many steel grades, enabling increased productivity. - Good casting properties:
Cast iron flows well, making it easy to cast complex shapes and suitable for mass production. - Excellent vibration damping:
Cast iron can effectively absorb vibration and reduce noise during equipment operation. - Cost-effectiveness:
Cast iron has a low cost, making it a cost-effective material choice.
Common Cast iron Parts Machining Methods
Cast Iron Parts Finishing
After machining cast iron parts, finishing or surface preparation is often required to enhance the quality, durability and appearance of the part. The following are commonly used finishing methods:
Sandblasting utilizes a high-speed jet of sand to clean the surface of the part, which removes oxides, impurities, and burrs, increases surface roughness, and lays the foundation for subsequent coatings. It not only improves the appearance, but also enhances the coating adhesion and wear resistance.
Spray painting provides corrosion protection and enhances the appearance of cast iron parts. Spray paint provides both rust protection and color, making it ideal for parts where aesthetics and protection are important.
Powder coatings are more durable and environmentally friendly than traditional liquid coatings. They form a strong coating on the surface of the part that protects against corrosion and abrasion, is heat and UV resistant, and is suitable for parts that are exposed to harsh environments.
Electroplating deposits metal ions on the surface of the part by means of electric current, forming a protective layer to enhance corrosion resistance and finish. It is suitable for parts requiring high corrosion resistance and high finish, and is widely used in automobile, machinery, electronics and other fields.
Cast Iron Parts Machining Methods Comparison:
Machining Method | Features | Applications | Tolerances | Surface Finish | Cost |
CNC Turning | Ideal for cylindrical parts, high precision, efficient production | Mechanical parts, automotive components | ±0.01 mm | Smooth (Ra 0.8-1.6 µm) | Medium |
CNC Milling | Multi-axis machining for complex geometries | Aerospace, molds, mechanical components | ±0.01 mm | High quality (Ra 0.8-3.2 µm) | Medium |
3D Printing | Layer-by-layer manufacturing, suitable for prototypes and complex parts | Prototypes, complex geometries | ±0.01 mm | Adjustable, rough to smooth | Low to medium |
Rapid Prototyping | Quick production for testing and prototyping | Design iterations, test samples | ±0.01 mm | Variable | Low |
Sheet Metal Fabrication | Suitable for large, thin parts with bending and cutting | Enclosures, brackets, panels | ±0.5 mm | Variable | Low |
Casting | Mass production of complex shapes, suitable for durable parts | Engine housings, mechanical components | ±0.01 mm | Medium (Ra 6.3-12.5 µm) | Low |
Brief Explanation of Cost Comparison:
- CNC Turning and CNC Milling:
High precision, moderate cost, suitable for high-demand precision machining. - 3D Printing:
Ideal for small batch production and complex parts, low upfront cost but higher for mass production. - Rapid Prototyping:
Lowest cost, ideal for quickly validating design concepts and prototypes. - Sheet Metal Fabrication:
Good for large-sized or thin parts, lower cost, efficient for mass production. - Casting:
Best for large quantities and complex shapes, lowest per-unit cost, though initial tooling can be expensive.
- CNC Turning and CNC Milling:
This comparison helps you choose the most suitable machining method based on your project’s requirements and optimize your costs accordingly.
Materials
100+ materials can be freely selected to meet your customized processing needs!
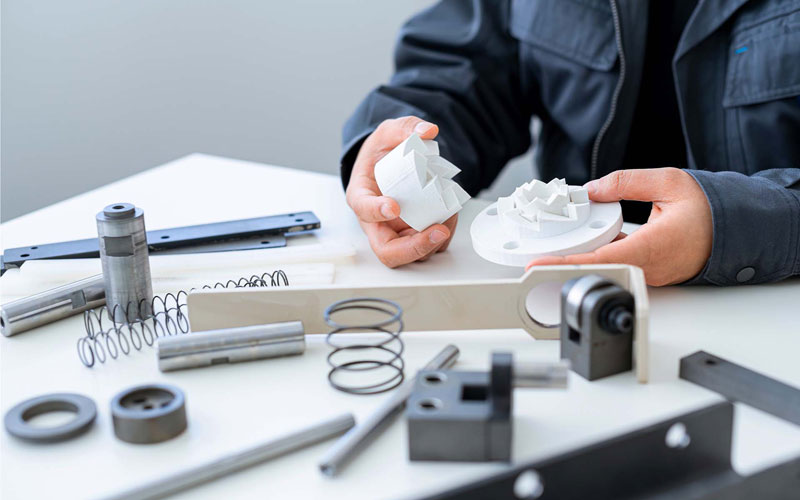
Metals
Metallic materials are rugged and offer excellent strength and durability.
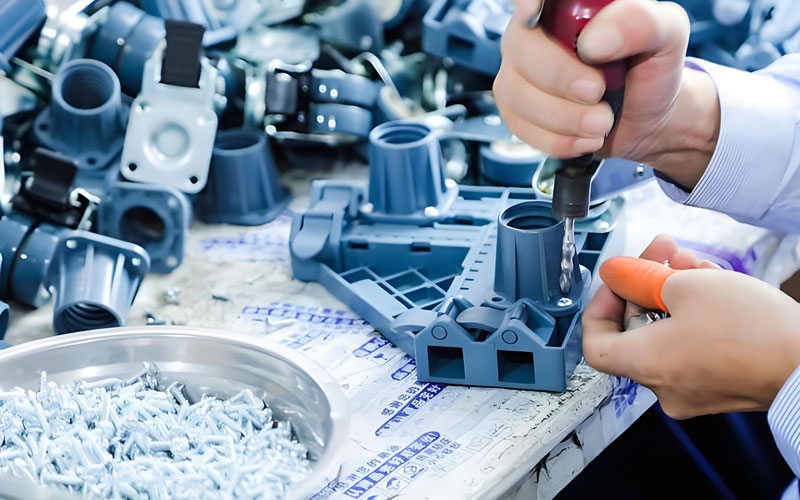
Plastics
Lightweight and flexible, used in a wide range of industries.
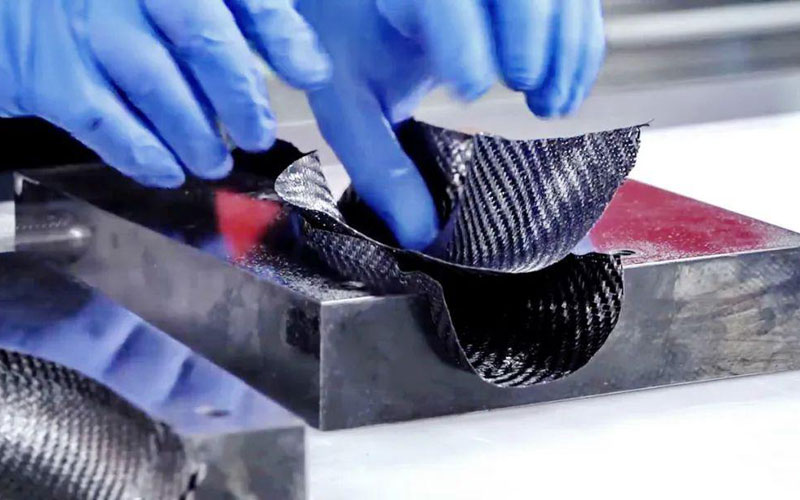
Composites
High-performance materials that combine strength and lightweight.
Why choose Allied Metal for cast iron parts machining?
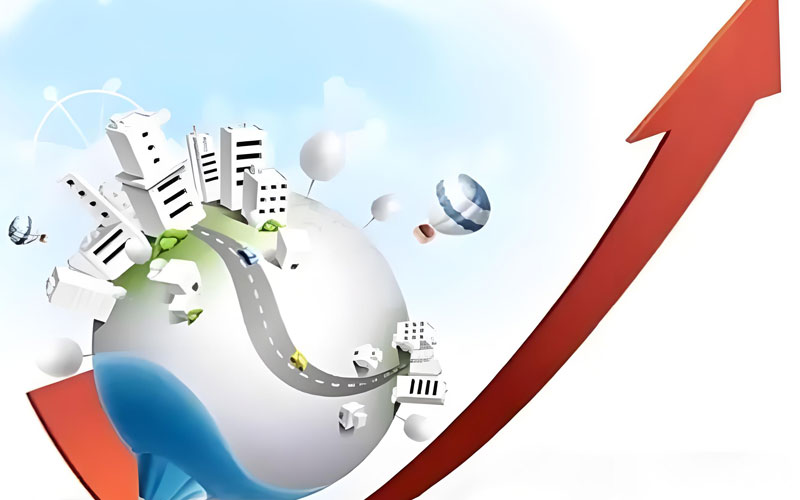
Professional technical support is available at every step from design to production to ensure smooth processing.

Equipped with advanced CNC machine tools and other equipment for cast iron parts of various complex shapes and accuracy requirements.

We leverage a robust supply chain and global partnerships to provide high-quality, customized materials for all projects.

We tailor processes to optimize cost, materials, and performance, ensuring efficient, high-quality delivery for any batch size.
FAQ
Consider factors like strength, corrosion resistance, weight, and cost. We can help guide you based on your specific requirements.
Reduce cracks by controlling cutting parameters and using high quality coolant.
Improve surface finish by using proper machining methods and tool selection.
Cast iron is hard and easy to wear tools, but we use advanced equipment and appropriate tools to ensure quality.
Depending on the complexity of the part, our efficient process ensures timely delivery.
Post-treatments such as deburring and grinding are usually required to improve durability and finish.