Plastic parts machining
Allied Metal – Your trusted partner for precision plastic parts machining, combining cutting-edge technology with expert craftsmanship.
- Source Factory
- Reasonable price
- Certified Materials
- Timely delivery
Plastic parts machining - A Comprehensive Guide
Plastic parts machining is becoming increasingly important in modern manufacturing.
Plastic materials are used in a wide range of industries because they are not only lightweight but also have good corrosion resistance, insulation and molding capabilities.
Common Plastic Processing Materials
Name | Properties | Applications | |
![]() | ABS | High strength, impact-resistant | Automotive interiors, consumer electronics housings, medical device casings |
![]() | PC (Polycarbonate) | Excellent transparency, high temperature resistance | Aerospace windows, automotive dashboards, optical lenses |
![]() | PA (Nylon) | Excellent wear resistance and toughness | Industrial gears, automotive bearings, aerospace fasteners |
![]() | PMMA (Acrylic) | High transparency, UV resistance | Display screens, aircraft and automotive light covers |
![]() | POM (Acetal) | Excellent mechanical properties, wear resistance | Industrial pulleys, motorcycle guides, precision gears |
![]() | PET | Chemical resistance, stability | Automotive components, medical device housings, food packaging |
![]() | PTFE (Teflon) | Low friction, high temperature resistance | Aerospace seals, industrial valves, chemical processing equipment |
![]() | PS (Polystyrene) | Low cost, easy to process | Medical instrument housings, industrial packaging materials |
![]() | PVC | Chemical resistance, good insulation | Automotive pipes, construction materials, cable sheathing |
![]() | TPU (Thermoplastic Polyurethane) | Good elasticity, strong wear resistance | Phone cases, automotive protective covers, sports equipment |
![]() | FEP (Fluorinated ethylene propylene) | Excellent chemical resistance, high temperature resistance | Aerospace cable sheathing, automotive fuel system components, industrial piping |
What is Plastic Parts Machining?
Plastic parts machining is the process of transforming plastic materials into a desired shape and function using different machining techniques. These machining techniques include CNC turning, CNC milling, 3D printing, investment casting, etc. When choosing a machining process, you need to weigh factors such as the part’s shape, size, accuracy requirements, and material properties.

Benefits of Choosing Plastic Machined Parts:
- Lightweight:
Plastics are lighter as compared to metal materials, which helps in reducing the overall weight of the product. - Corrosion resistance:
Plastics are highly resistant to a wide range of chemicals. - Insulation:
The good insulating properties of plastic materials make them suitable for electrical and electronic products. - Molding Flexibility:
Plastics can be easily molded through a variety of processing methods to accommodate different design needs.
- Lightweight:
How to choose the right plastic material for processing?
Choosing the right material is crucial in the plastic parts machining process. The right material not only enhances product performance, but also reduces production costs and improves processing efficiency. In order to ensure the science and economy of material selection, we need to consider from a number of aspects.
Evaluate the environment and functional requirements of the part. Is the part exposed to high temperatures, chemicals or stress? Different application scenarios will have a direct impact on material selection.
Select materials based on properties such as strength, toughness, temperature resistance, and chemical resistance. Ensure that the material maintains its functionality and stability under various conditions of use.
Different processing methods have different requirements for materials, ensure that the selected material is suitable for the planned processing methods, such as CNC machining, casting or 3D printing.
Consider the recyclability and environmental friendliness of the material. Choosing environmentally friendly materials not only contributes to the brand image, but is also in line with the trend of sustainable development.
By taking into account application requirements, material performance, cost, processing feasibility and environmental considerations, you can make the optimal material choice to ensure your products are competitive in the marketplace. If you have any questions or need expert advice, the Allied Metal team is here to support you.
Plastic Machining Methods Comparison:
Name | Principle | Advantages | Suitable Batches | Requires Mold | Manufacturing Cycle | Precision | Surface Roughness | Cost Analysis |
CNC Turning | Cutting material with rotating tools | High efficiency, ideal for cylindrical parts | Mass production | ❌ | Medium | ±0.01 mm | Smooth | Moderate unit cost, limited to simple shapes |
CNC Milling | Material removal using multi-axis milling machines | High flexibility, suitable for precision parts | Small to medium batches | ❌ | Medium | ±0.01 mm | Smooth | Higher cost, good for precision, no molds |
Laser Cutting | Cutting using a focused laser beam | Fast processing, ideal for thin sheet metal | Small to medium batches | ❌ | Short | ±0.05 mm | Smooth | Low initial cost, higher unit cost for custom production |
Sheet Metal | Bending, stamping, and welding metal sheets | Cost-effective, high material efficiency | Mass production | ✔ | Medium | ±0.01 mm | Variable | Low cost, suitable for large batches, mold costs are higher |
Investment Casting | Casting complex metal parts using wax molds | Ideal for complex structures, low unit cost for large batches | Mass production | ✔ | Long | ±0.1 mm | Smooth | Mold required initially, cost-effective for large production |
3D Printing | Layer-by-layer material addition | No molds required, flexible for complex shapes and prototyping | Small batches and rapid prototypes | ❌ | Short | ±0.1 mm | Variable | Higher cost, ideal for prototyping and customization |
Rapid Prototyping | Using various rapid prototyping technologies (e.g., SLA, SLS) | Fast sample creation, ideal for design validation | Small batch production | ✔ | Medium to Long | ±0.1 mm | Variable | Low cost, short production cycle, suitable for small batch production |
PS: Mold Manufacturing Impact
- Initial Cost: Manufacturing a mold increases initial cost, especially in investment casting and injection molding.
- Economy: The cost of the mold is spread out over a large production run, which can significantly reduce the cost per part.
- Overall Consideration: The choice of whether or not to manufacture a mold needs to be considered in conjunction with the scale of production and the complexity of the part.
Why choose Allied Metal for custom Plastic parts machining?

We have an experienced team that can provide professional material and machining suggestions.

Using the latest machining equipment to ensure high precision and quality parts.
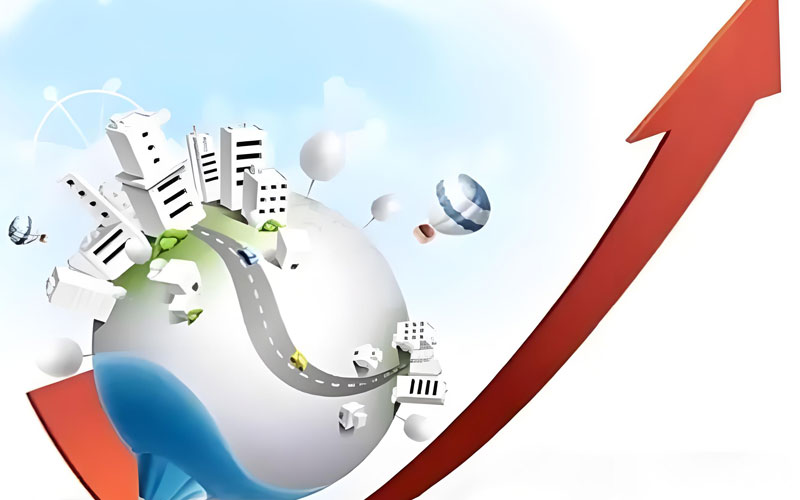
We provide a full range of customized services from design to production to meet your different needs.
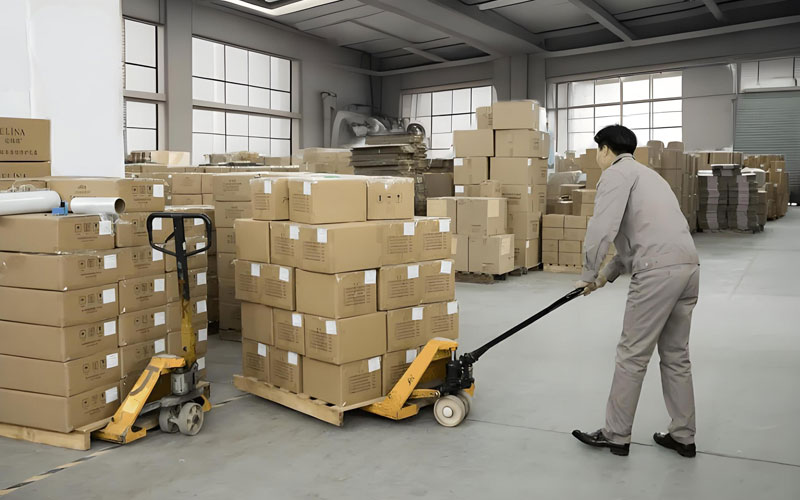
We value every project and ensure on-time delivery to help you move forward smoothly.
FAQ
Material selection depends on the purpose of the part, environmental requirements (e.g., temperature, chemical exposure, etc.), and budget. Common materials such as ABS, polypropylene and nylon each have their own advantages. We can recommend the right material for your specific needs.
Accuracy varies with different machining methods. Typically, CNC machining can achieve an accuracy of ±0.01mm, while 3D printing is slightly less accurate. We will choose the appropriate process according to your requirements to ensure that the part meets the design specifications.
The lead time depends on the complexity of the process, the number of parts, and the machining method chosen; 3D printing is usually the fastest, while complex molds or investment casting may take longer. We can provide a specific time estimate at the start of the project.
Costs are primarily influenced by volume, part complexity, and the machining method chosen. For small quantities and complex parts, 3D printing and rapid prototyping are more economical, while for larger quantities, CNC machining or investment casting are more cost effective.
No, but we can guarantee that you will get the highest quality and accuracy plastic parts from us for the same price.
Surface treatments for plastic parts include polishing, painting, plating and laser engraving. Depending on the nature of the material and the needs of the customer, we offer a variety of surface treatment options to enhance the appearance and functionality of the part.
We have a rigorous quality control process that monitors the entire process, from material selection and machining processes to finished product inspection. We also offer sample testing and third-party quality inspections to ensure that each batch of parts meets your standards and industry specifications.