Table of Contents:
AI in CNC Machining: Smart Manufacturing & Future Innovations
- March 24, 2025
- Tony
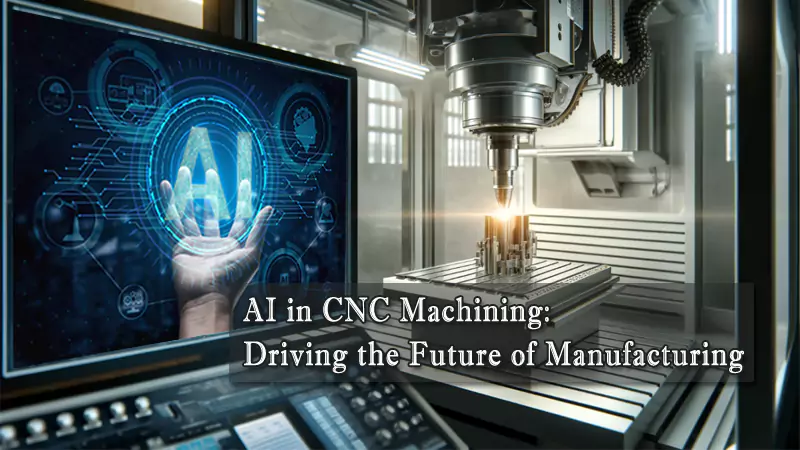
AI in CNC machining has transformed the field from basic mechanical operations to modern intelligent production. With continuous technological advances and the integration of AI, CNC machining now achieves unparalleled precision and efficiency, driving a shift toward smart manufacturing.
1. The Rise of AI in CNC Machining
1.1 Impact of AI on CNC Manufacturing
In the CNC manufacturing process, AI(Artificial Intelligence) is promoting the transition from traditional mechanical operations to intelligent manufacturing. Through real-time data acquisition and analysis, AI improves machining accuracy and productivity, while optimizing the entire manufacturing process and helping companies achieve digital upgrading.
1.2 How AI improves CNC machining?
Driven by Industry 4.0 and digital transformation, traditional CNC machining equipment is moving from single mechanical operation to intelligent management.
- CNC machines are deeply integrated with AI (Artificial Intelligence) technology to realize real-time data collection and online monitoring.
- Data-driven decision-making enables enterprises to rapidly optimize the production process and improve processing accuracy and efficiency.
1.3 AI-driven CNC tools and machines
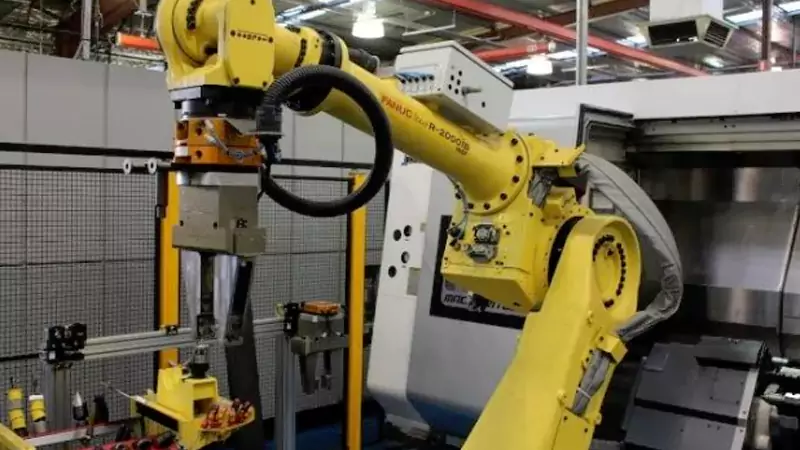
CNC tools and machines are intelligently upgraded using AI and machine learning technologies. Through automatic adjustment of machining parameters and predictive maintenance, machine performance and machining accuracy are significantly improved, ensuring a more efficient and stable production process.
Automation and digital management
Utilizing big data and machine learning algorithms, the equipment can automatically adjust the processing parameters during operation to achieve optimal working conditions.
System optimization and energy consumption reduction
Through intelligent monitoring and optimization control, enterprises can reduce energy consumption and operating costs to achieve green manufacturing.
2. Intelligent Algorithms for Optimizing CNC Programming and Tool Paths
2.1 AI in CNC machining programs
AI has changed the traditional CNC programming model:
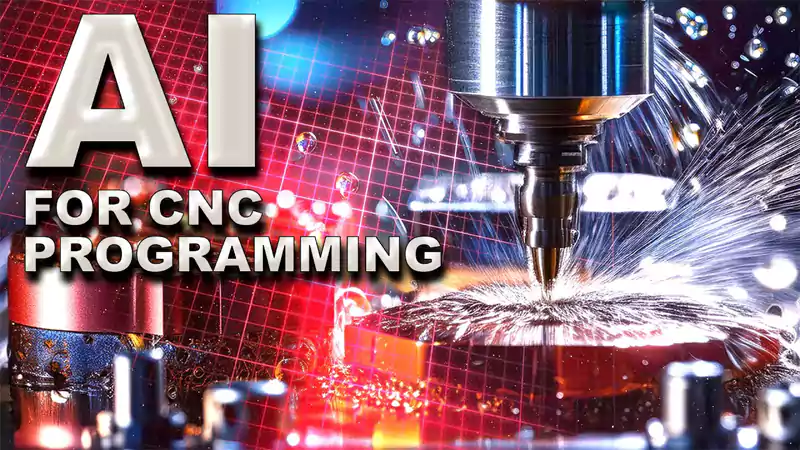
- Intelligent assisted programming:
With the help of AI tools, the system automatically generates and optimizes G-code, significantly reducing human error and debugging time. - Adaptive learning system:
Through the continuous accumulation of historical machining data, the intelligent system can optimize the programming strategy to meet the needs of diverse parts machining.
2.2 Automatic tool path planning
- Machine learning algorithm application:
Deep learning technology enables the system to automatically plan the optimal tool path according to process parameters. - Efficient and precise machining:
Automatic path planning not only improves machining accuracy, but also provides flexible and customized solutions for complex parts machining.
3. Quality monitoring and predictive maintenance
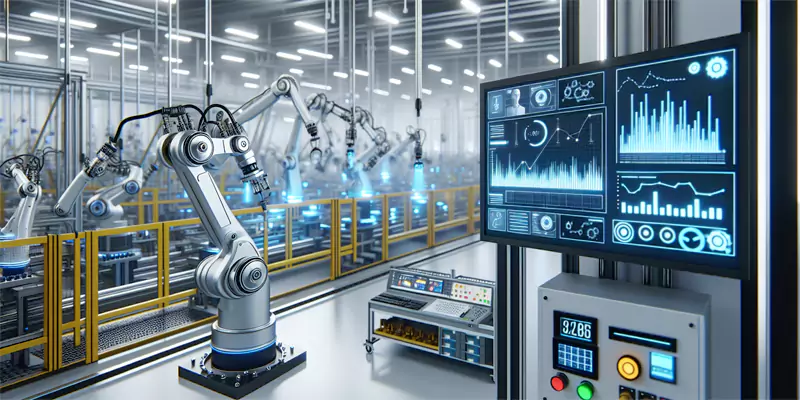
3.1 Real-time quality inspection system
Machine vision and sensing technology
High-definition cameras and sensors capture processing details in real time, accurately detecting minute deviations in products.
Data-driven quality control
Real-time data comparison and correction to ensure the stability and consistency of each batch of products.
3.2 AI-driven Predictive Maintenance
Early warning and risk control
Based on the historical operating data of the equipment, the intelligent system recognizes potential failures in advance and provides early warning.
Reduce Maintenance Costs and Downtime Risks
Predictive maintenance strategy effectively reduces sudden failures and production interruptions, and extends equipment life.
4. AI in CNC Machine Shops
Intelligent workshop management and production process innovation.
4.1 Application of AI in CNC Machine Shop
Robot arm and automated handling
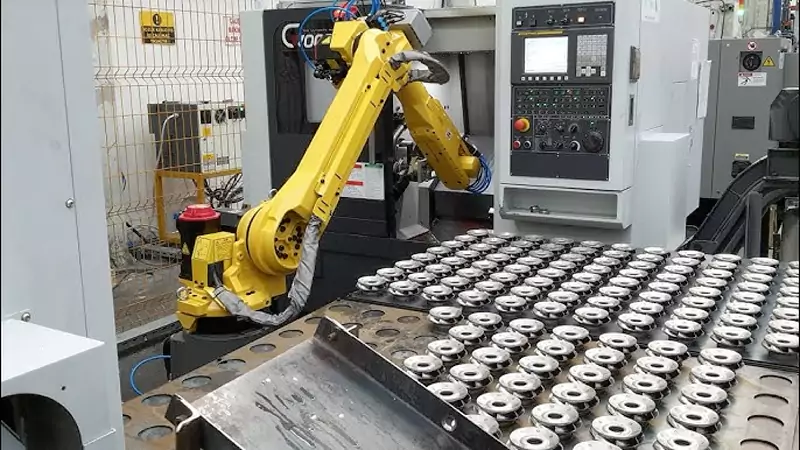
For example, AI-driven robot arms can automatically carry raw materials to designated locations, reducing manual intervention and improving logistics efficiency.
CNC Lathe and Intelligent Machining
CNC lathes utilize AI to adjust tool paths and machining parameters in real time, ensuring high-precision machining and significantly reducing production errors.
Automated Inspection System
Inspection equipment integrated with AI can monitor processing quality in real time, automatically identify and correct potential problems, and ensure product consistency.
4.2 Production efficiency and process optimization
Through real-time monitoring and dynamic scheduling, combined with the intelligent scheduling system, resource allocation and processing flow are effectively optimized, and production efficiency is improved.
4.3 Cost Control and Energy Consumption Management

Utilizing data-driven management, it realizes accurate scheduling of manpower, materials and energy, reduces resource wastage and operating costs, and promotes green manufacturing at the same time.
5. Big data and AI reshape supply chain decision-making

Full Process Data Monitoring
- Closed-loop supply chain management:
From the procurement of raw materials to the release of products from the warehouse, the whole chain of data monitoring to realize the transparent management of the supply chain. - Real-time data feedback and adjustment:
Real-time data collection enables enterprises to quickly adjust production plans and improve the overall efficiency of the supply chain.
Intelligent Inventory and Logistics Management
- Demand prediction and inventory optimization:
AI algorithm accurately predicts market demand, dynamically adjusts inventory levels, and reduces storage costs. - Intelligent Logistics Scheduling:
Data analysis helps enterprises optimize logistics paths and distribution plans, realizing the intelligence of the entire supply chain.
6. Service Upgrade: Intelligent Transformation of CNC Machining Enterprises
6.1 Customized machining and automatic quotation
Personalized machining program development
According to customer needs and historical data, the intelligent system quickly generates customized machining solutions.
Automated Quotation System
Based on real-time data and intelligent algorithms, the quotation is automatically generated to improve response speed and service quality.
6.2 Market Competitiveness and New Service Models
Reshaping the Competitive Pattern of Traditional Manufacturing
Intelligent transformation improves product quality and shortens delivery cycle, giving enterprises an edge in competition.
Open up new value-added services
The application of digital management and intelligent tools provides enterprises with a more flexible and efficient service model.
7. Benefits of AI for the Machining Industry
Artificial Intelligence technology brings a number of significant benefits to CNC machining and the manufacturing industry as a whole:
Increased Machining Efficiency
AI automated programming and path planning dramatically reduce cycle time and increase productivity.
Improved Product Quality
Through accurate real-time monitoring and data analysis, product quality is more consistent and error rates are dramatically reduced.
Reduced Operating Costs
Predictive maintenance, intelligent scheduling, and optimized management reduce equipment failures and energy waste, significantly lowering costs.
Enhance market competitiveness
Customized services and automatic quotation system help enterprises respond quickly to market demand and develop new business models.
Promoting Green Manufacturing
High-efficiency, low-energy intelligent manufacturing model helps enterprises realize sustainable development and promote the concept of green environmental protection.
8. Future Outlook: AI leads intelligent manufacturing in CNC machining
In the future, AI will play a greater role in CNC machining to achieve intelligent manufacturing upgrades. AI will be deeply integrated with CAD/CAM software to optimize tool paths and machining strategies in real-time to ensure machining accuracy.
In addition, the AI system can automatically detect the machining results and optimize the design parameters based on the data feedback to improve product quality and production efficiency, accelerating the manufacturing industry to the direction of intelligence and automation.
9. Summary
The deep integration of AI and CNC machining is driving the manufacturing industry toward efficiency, precision, and intelligence. Enterprises can not only reduce costs and improve competitiveness, but also realize green and sustainable production.
Although there are still certain challenges, the advantages brought by AI and machine learning are huge. Partnering with a professional CNC machining service provider will enable you to apply smart technology faster, optimize your production process, and seize the future opportunities of smart manufacturing.
FAQ | AI in CNC machining
AI is transforming CNC machining, with applications including: intelligent programming, toolpath optimization, predictive maintenance, quality monitoring, and smart shop floor management. These innovations help CNC machining service providers deliver high-efficiency, precision, and customization.
By integrating intelligent CAD/CAM programming with adaptive toolpath optimization, AI generates optimal G-codes automatically. This enhances custom parts machining accuracy, reduces programming time, and minimizes human intervention, making CNC machining more efficient.
Yes, AI helps CNC machining companies detect failures in advance, reduce unplanned downtime, and improve the stability of CNC machining lines through predictive maintenance via big data analysis and equipment health monitoring.
AI recognizes machining errors through real-time monitoring and adaptive adjustment and makes automatic corrections to ensure stable quality of CNC precision parts machining, reduce the rate of defective products, and improve the production qualification rate of CNC machining service providers.
Through sensor data collection and machine learning algorithms, AI can analyze equipment operating conditions, identify anomalies in advance, and notify operators to perform preventive maintenance, thus reducing equipment failures and ensuring the continuous operation of CNC manufacturing lines.
Intelligent CNC machining will combine the Industrial Internet of Things (IIoT), automated robots, and smart supply chains to help CNC machining companies realize a more efficient and environmentally friendly production model.
In the customer service of CNC machining service providers, AI can be used for: intelligent quotation system, order management automation, customized machining program recommendation and intelligent customer service.
AI is primarily used to assist with CNC machine operations and improve part machining efficiency, not to completely replace operators. Skilled CNC technicians still play an important role in machine maintenance, process optimization, and complex tasks.