Selecting the right process—CNC machining or EDM—is crucial. A poor choice can result in design limitations, tolerance errors, and added costs.
CNC machining is a subtractive process that cuts material with rotating tools. EDM (Electrical Discharge Machining) uses electrical sparks to erode material. Both are precise, but suited for different applications.

At Allied Metal, we focus on precision manufacturing. While my background is in CNC machining, I’ve always admired the power of other advanced methods. For engineers like David, understanding all available tools is a big advantage. CNC and EDM are both precise, but they meet different needs. CNC is faster and more flexible for most materials, while EDM is better for complex shapes or very hard, conductive materials. The right choice depends on your part’s specific requirements.
What Is CNC Machining?
You know, CNC is a core manufacturing process. But what is the fundamental definition of CNC machining, and what makes it so versatile and widely used?
CNC machining is a subtractive manufacturing process that uses computer-controlled cutting tools to remove material from a workpiece, shaping it into a precise, custom-designed part from materials like metal or plastic.
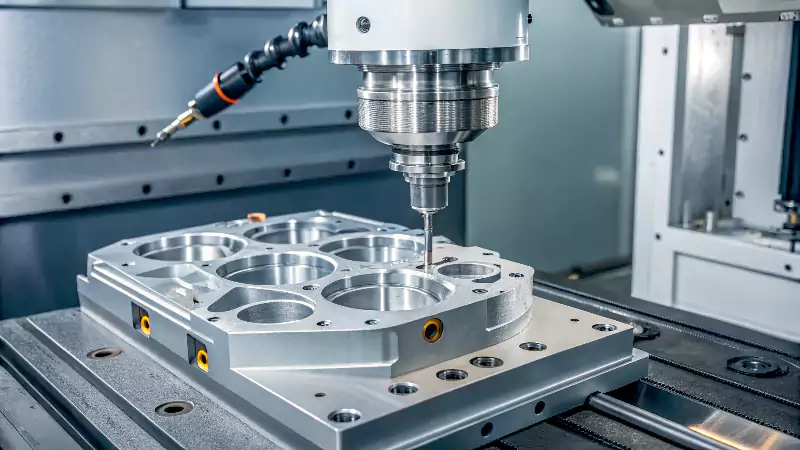
Explore CNC Machining
CNC machining is the workhorse of modern manufacturing and a process I've dedicated my life to. At its heart, it is a subtractive process. This means we start with a solid block or piece of raw material (the workpiece) and strategically cut away material to reveal the final part.
The "CNC" part stands for Computer Numerical Control. This is the brain of the operation. Instead of a machinist manually turning wheels and levers, a computer program dictates every movement. Here’s a simple breakdown of the process:
- Design: An engineer like David creates a 3D model of the part using CAD (Computer-Aided Design) software.
- Programming: This digital file is loaded into CAM (Computer-Aided Manufacturing) software. A programmer plots the path for the cutting tools and sets parameters like speed and feed rate. This generates a machine code (G-code).
- Machining: The G-code is sent to the CNC machine. The machine then automatically executes the commands, using rotating cutting tools (like end mills, drills, and turning tools) to precisely remove material from the workpiece.
This method is incredibly versatile. We use custom CNC machining for everything from simple brackets to highly complex aerospace components. It can be applied to a vast range of materials, including aluminum, steel, stainless steel, titanium, and all types of engineering plastics. The main types of CNC machining are milling (rotating tool, stationary part) and turning (rotating part, stationary tool), which together can create almost any geometry.
What Is EDM, and What Makes It Unique?
You've heard of CNC machining, but what is EDM? What is this process that can cut hard metals with such high precision using electricity?
EDM, or Electrical Discharge Machining, is a non-contact thermal process. It uses controlled electrical sparks between an electrode and a conductive workpiece to precisely erode material, creating complex shapes.
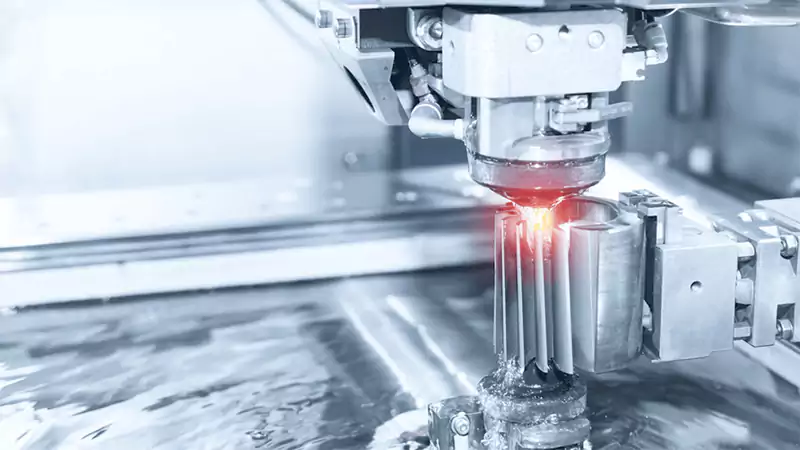
In-depth study of Electrical Discharge Machining (EDM)
EDM machining, which stands for Electrical Discharge Machining, is a fascinating and highly specialized manufacturing process. Unlike conventional CNC machining that uses physical force to shear away material with a cutting tool, EDM is a non-contact thermal erosion process1. It's sometimes called "spark machining" or "spark eroding," which gives a good clue as to how it works.
The fundamental principle relies on electricity:
- The Setup: The workpiece and an electrode tool are submerged in a dielectric fluid2 (a non-conductive liquid, usually deionized water or oil). The workpiece and the electrode are separated by a tiny gap.
- The Spark: A powerful electrical voltage is applied, creating an intense electric field in the gap. This field breaks down the dielectric fluid, allowing a controlled electrical spark to jump from the electrode to the workpiece.
- The Erosion: This spark is incredibly hot (reaching thousands of degrees Celsius), instantly melting and vaporizing a microscopic particle of the workpiece material.
- The Flush: The flowing dielectric fluid immediately cools the area and flushes away the eroded particle (the "chip").
- The Repetition: This process is repeated thousands of times per second, with each spark removing another tiny particle of material. The computer-controlled (CNC) movement of the electrode allows these sparks to precisely erode the workpiece into the desired shape.
The key takeaway is that EDM machining doesn't involve any physical cutting force. This makes it unique and gives it capabilities that traditional CNC machining cannot match, especially when working with extremely hard materials.
What Are the Two Main Types of EDM Machines?
If EDM uses electrical sparks, how is that applied? What are the primary machine types and methods used in EDM machining to create different kinds of parts?
The two main types of EDM machining are Wire EDM, which uses a thin wire as the electrode to make precise 2D cuts, and Sinker EDM, which uses a custom-shaped electrode to "sink" impressions into a workpiece.
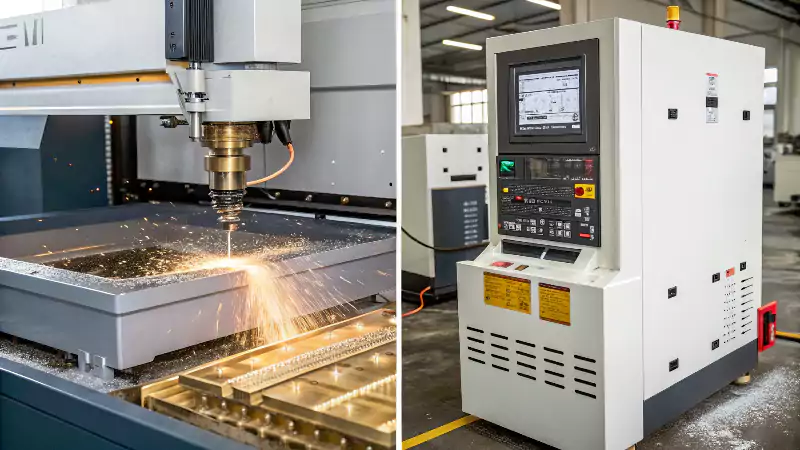
Diving Deeper into Wire and Sinker EDM
While the principle of spark erosion is the same, EDM machining is generally performed using two distinct types of machines, each designed for different kinds of applications. For David, knowing which type is used helps in understanding the geometric possibilities.
1. Wire EDM (Wire-Cut EDM)
- How it Works: In Wire EDM, the electrode is a very thin, continuously spooling metallic wire (often brass, copper, or tungsten), typically between 0.004" and 0.012" (0.1mm to 0.3mm) in diameter. This energized wire is fed through the workpiece, and the sparks jump from the wire to the part, eroding a very narrow path or "kerf." The path of the wire is controlled by a CNC system, much like a bandsaw cutting a shape out of wood, but with extreme precision and no cutting force.
- What it's Used For: Wire EDM is used to cut intricate 2D profiles, contours, and shapes completely through a workpiece. It is excellent for creating punches and dies for tool making, extrusion dies, precision gears, and any part that requires sharp internal corners that a CNC machining end mill cannot create. The top and bottom wire guides can move independently, allowing for the creation of tapered shapes.
2. Sinker EDM (also called Ram EDM, Die Sinking, or Cavity-Type EDM)
- How it Works: In Sinker EDM, the electrode is a custom-machined 3D shape, typically made of graphite or copper. This shaped electrode is the "positive" of the cavity to be created. The electrode is slowly lowered or "sunk" into the workpiece, and sparks erode the material to form a "negative" impression of the electrode's shape.
- What it's Used For: Sinker EDM is used to create complex 3D cavities, blind pockets (pockets that don't go all the way through), intricate details, and sharp internal features. It is heavily used in the manufacturing of molds for plastic injection molding, forging dies, and creating features that are impossible to reach with traditional cutting tools used in precision CNC machining.
These two methods give EDM machining incredible flexibility for creating highly complex and precise components.
When Does EDM Provide Better Results Than Conventional Machining?
Both CNC machining and EDM are precise. So, in what specific situations would an engineer choose EDM, even if a part could technically be machined?
EDM provides better results for machining extremely hard materials, creating very sharp internal corners, deep and narrow ribs or slots, and producing complex internal shapes that traditional cutting tools cannot reach.
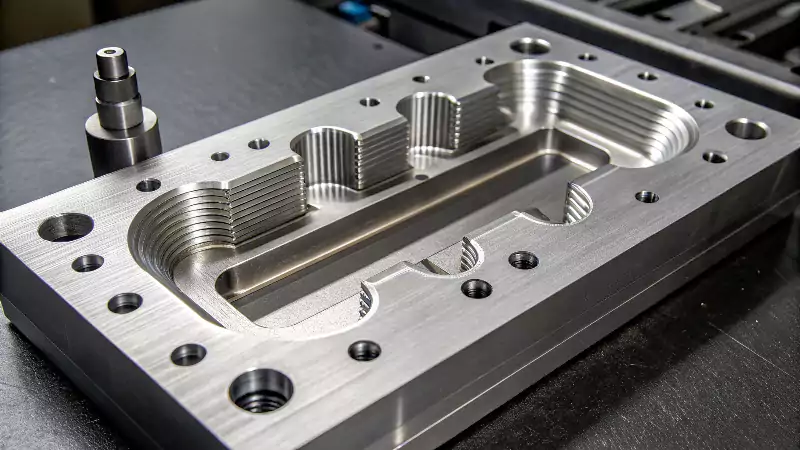
Understanding the Benefits of EDM
While CNC machining is the more common and often faster process, there are specific scenarios where EDM machining is not just a better choice, but the only viable choice. An experienced engineer like David knows to consider EDM when faced with certain design challenges.
Here are the situations where EDM excels:
-
Machining Extremely Hard Materials:
- Conventional CNC machining struggles with materials that are harder than the cutting tool itself, such as hardened tool steels, carbide, titanium, and exotic superalloys. Machining these materials is slow, causes rapid tool wear, and can be very difficult.
- Because EDM machining is a non-contact process that relies on thermal energy, it doesn't care how hard the workpiece is, as long as it's electrically conductive. It can easily and precisely machine materials that are too hard or tough for milling or turning.
-
Creating Sharp Internal Corners:
- A CNC machining process using a rotating end mill will always leave a radius in an internal corner, equal to the radius of the tool. Achieving a perfectly sharp square internal corner is physically impossible with a round, rotating tool.
- Wire EDM can produce extremely sharp internal corners, often with a radius as small as the wire itself plus the spark gap (e.g., under 0.006"). Sinker EDM can also produce sharp corners based on the electrode's shape.
-
Complex or Delicate Geometries:
- Deep, Narrow Ribs or Slots: Machining very deep and narrow features with a long, thin end mill is very difficult due to tool deflection and breakage. Wire EDM or Sinker EDM can create these features with ease and no mechanical stress.
- Thin Walls: The high cutting forces of CNC machining can deform or break delicate, thin-walled parts. EDM exerts no mechanical force, making it ideal for such applications.
- Complex Internal Cavities: Sinker EDM can create intricate internal shapes that are impossible to reach with any rotating tool.
My experience shows that while CNC machining services cover most needs, knowing when to switch to EDM machining for these specific challenges is what separates a good machine shop from a great one.
CNC Machining VS EDM Machining
For a direct comparison, what are the key pros and cons of CNC machining versus EDM machining? How do their processes and applications stack up?
CNC machining is faster and works on any material but is limited by tool geometry and hardness. EDM is slower but excels at hard materials, sharp corners, and complex internal shapes.
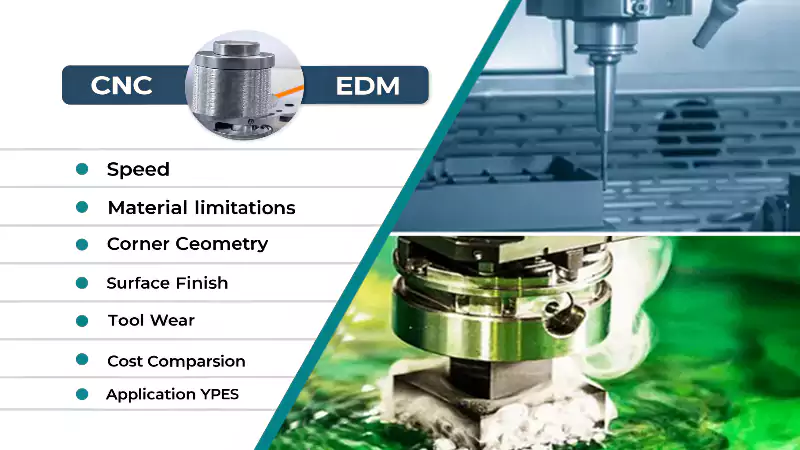
Diving Deeper into a Head-to-Head Comparison
To help David and other engineers make an informed choice, it's useful to directly compare CNC machining and EDM machining across several key areas.
Feature | CNC Machining | EDM (Electrical Discharge Machining) |
---|---|---|
Process | Subtractive (Mechanical): A rotating tool physically cuts and shears material. | Thermal Erosion: Electrical sparks melt and vaporize material without contact. |
Advantages | - Very fast material removal rates. - Works on any machinable material (metals, plastics, wood). - Lower cost for general geometries. - Highly versatile for a wide range of parts. |
- Can machine extremely hard materials. - Creates sharp internal corners. - No mechanical stress on the part. - Can produce very complex internal shapes. - Excellent surface finish possible. |
Disadvantages | - Struggles with very hard materials. - Cannot create sharp internal corners. - Cutting forces can affect delicate parts. - Limited by tool access and geometry. |
- Slower process, longer cycle times. - Only works on electrically conductive materials. - Higher operational cost for some jobs. - Electrode wear must be managed (Sinker EDM). |
Materials | All metals, plastics, composites, wood. | Only electrically conductive materials (steels, titanium, copper, carbide, aluminum, etc.). |
Typical Applications | Housings, brackets, shafts, plates, prototypes, general fabrication. | Injection molds, dies, hardened steel tools, medical implants, turbine blades. |
Key Capability | Versatility and speed for a wide range of parts and materials. | Precision on hard materials and complex/internal geometries. |
In Summary:
If your part is made from a standard material like aluminum or mild steel and has features that can be reached with standard cutting tools, custom CNC machining is almost always the faster, more cost-effective choice. It's the workhorse for prototypes and production runs.
However, if you are designing a part from hardened tool steel, require perfectly sharp internal corners for a die, or need a complex blind cavity for an injection mold, EDM machining becomes the essential technology. It solves problems that conventional CNC machining simply cannot.
What does EDM stand for in CNC?
You see "CNC" paired with both milling and EDM. What exactly is the relationship? What does EDM mean in the context of CNC?
EDM stands for Electrical Discharge Machining. In the context of CNC, it means the EDM process (wire or sinker) is controlled by a Computer Numerical Control system for precise, automated movement.
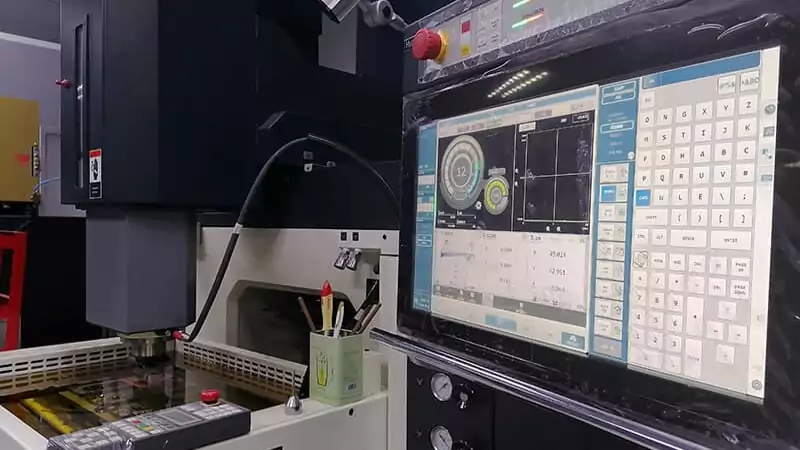
Relationship between CNC and EDM
This is a common point of confusion, so it's a great question to clarify. "EDM" does not stand for anything within the term "CNC." Rather, CNC and EDM are two distinct concepts that work together to create a modern manufacturing process.
Let's break it down:
- CNC (Computer Numerical Control): As we've discussed, this is the control system. It is the brain that reads a digital program (G-code) and translates it into precise mechanical movements. CNC systems are used to automate a huge variety of machines, not just mills and lathes.
- EDM (Electrical Discharge Machining): This is the physical process of removing material. It is the method of using electrical sparks to erode a conductive workpiece.
So, when we talk about a "CNC EDM machine3," we mean:
An EDM machine (that uses the spark erosion process) which is controlled by a CNC system (the computer brain).
The relationship is the same as it is for CNC machining:
- A CNC Milling Machine = A Milling Machine + A CNC Control System.
- A CNC Lathe = A Lathe + A CNC Control System.
- A CNC Wire EDM Machine = A Wire EDM Machine + A CNC Control System.
The CNC controller is what tells the Wire EDM machine exactly what path the wire should follow to cut a complex shape. It tells the Sinker EDM machine how to precisely lower the electrode into the workpiece. Without the CNC component, EDM would be a very limited, manual process. The CNC system is what makes modern EDM machining so incredibly precise, repeatable, and capable of creating the complex geometries that engineers like David design. They are two separate technologies that combine to make a powerful manufacturing tool.
Which material cannot be machined by EDM?
EDM seems very powerful, but it must have limitations. What types of materials are completely unsuitable for any kind of EDM machining process?
EDM machining cannot be used on any material that is not electrically conductive. This includes plastics, ceramics, glass, composites, wood, and most pure forms of stone or diamond.

Material Limitations for EDM
The greatest strength of EDM machining — its ability to cut regardless of material hardness—is also directly linked to its single biggest limitation: the workpiece material must be electrically conductive4.
The entire EDM machining process is based on creating a controlled electrical spark between an electrode and the workpiece. If the workpiece cannot conduct electricity, there is no path for the spark to form, and no erosion can take place. It's a fundamental requirement of the physics involved.
Materials That CANNOT Be Machined by EDM:
- All Plastics: Polymers like ABS, Polycarbonate, Nylon, Delrin (Acetal), PEEK, and Acrylic are electrical insulators.
- Most Ceramics: Materials like Alumina, Zirconia, and Silicon Nitride are excellent insulators and cannot be machined by EDM. (Note: Some special "conductive ceramics" do exist but are rare).
- Glass: A classic electrical insulator.
- Wood: An organic insulator.
- Composites: Most common composites, like carbon fiber reinforced polymer (CFRP) or fiberglass, are not suitable because the polymer matrix is non-conductive.
- Diamond: While very hard, natural diamond is typically a very poor electrical conductor.
What does this mean for engineers?
For an engineer like David, this is a clear dividing line. If he is designing a part from an engineering plastic like Delrin or a ceramic component for high-temperature insulation, EDM machining is not an option. He would need to rely entirely on conventional CNC machining processes like milling or turning for those materials.
This limitation is why machine shops like Allied Metal offer a range of services. We use our precision CNC machining centers for plastics, composites, and standard metals, and would look to specialized processes like EDM only when the combination of material (conductive and very hard) and geometry (complex, sharp corners) demands it. It highlights why having knowledge of multiple manufacturing methods is so important.
Can aluminum be EDM machined?
Aluminum is a common material for CNC machining. But since it's conductive, is it a good candidate for EDM machining, and when would you use it?
Yes, aluminum can be EDM machined because it is electrically conductive. However, since aluminum is also very easy to machine with conventional CNC machining, EDM is typically only used for creating specific features.
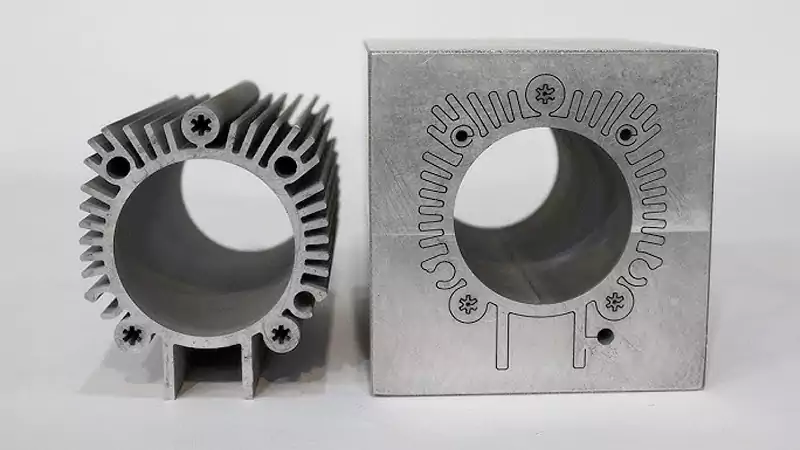
Understanding EDM and Aluminum
This is an excellent practical question. The short answer is yes, absolutely. Aluminum and its alloys are electrically conductive, which is the primary requirement for a material to be suitable for EDM machining.
However, the more important question is should you use EDM on aluminum? The answer depends entirely on the part's geometry.
Why CNC Machining is Usually Preferred for Aluminum:
Aluminum is one of the easiest and fastest materials to machine using conventional CNC machining.
- High Speeds: It can be cut at very high speeds and feed rates.
- Excellent Machinability: It produces good surface finishes and puts relatively little wear on cutting tools.
- Cost-Effective: Because it can be machined so quickly, the cost of CNC machining aluminum is generally very low compared to other metals.
For 99% of aluminum parts, precision CNC machining (milling or turning) is the faster, more economical, and logical choice. There would be no reason to use the much slower EDM machining process for standard features like pockets, holes, or profiles.
When Would You Use EDM on Aluminum?
Despite aluminum's excellent machinability, there are a few specific situations where an engineer like David would need to specify EDM machining for an aluminum part:
- Sharp Internal Corners: This is the most common reason. If a design requires perfectly sharp internal corners that a rotating end mill cannot produce, Wire EDM is the only way to achieve them. For example, creating a square or hexagonal hole through an aluminum extrusion.
- Extremely Thin Walls or Delicate Features: If a part has features so thin and delicate that the physical force of a CNC machining tool would risk deforming or breaking them, the non-contact nature of EDM makes it a viable solution.
- Deep, Narrow Slots: If a slot is too deep and narrow for a standard end mill to reach without breaking (due to a poor length-to-diameter ratio), Wire EDM can cut it cleanly and precisely.
- Complex Blind Cavities: For certain mold applications or fluidic components made of aluminum, Sinker EDM might be needed to create internal shapes that are impossible to reach with any cutting tool.
So, while it's entirely possible, using EDM machining on aluminum is a specialized choice driven by specific geometric requirements that CNC machining cannot meet.
Conclusion
CNC machining offers speed and versatility, while EDM provides precision for hard materials and complex shapes. Choosing the right process is key to optimizing manufacturing efficiency and part quality.
-
Understanding this process is crucial for grasping how EDM machining differs from traditional methods, enhancing your knowledge in manufacturing techniques. ↩
-
Learning about dielectric fluid is essential for understanding the EDM process, as it significantly impacts the efficiency and effectiveness of machining operations. ↩
-
Learn about CNC EDM machines to understand their role in precision manufacturing and automation. ↩
-
Understanding electrically conductive materials is crucial for effective EDM machining. Explore this link to learn more about suitable materials. ↩