Struggling with materials that are too hard to machine or form? Brittle metals can crack under stress, leading to wasted effort and compromised part integrity.
Annealing is a heat treatment process that alters a metal's microstructure to make it softer, more ductile, and easier to work with. It involves heating, soaking, and slow cooling.

Over my years running Allied Metal and working hands-on with CNC machining, I've seen countless situations where the condition of the raw material makes all the difference. You can have the most advanced machines, but if your metal is too hard or full of internal stresses, you're in for a tough time. That's where processes like annealing become so important. My insight is that annealing is a fundamental heat treatment that softens metal, making it easier to work with and improving its overall ductility. For engineers like David, understanding this process is key. In my experience, knowing when and how to anneal, or specify annealed material, can significantly enhance the quality and longevity of metal components, not to mention making our job as machinists a lot smoother. Let's take a closer look at this essential metalworking technique.
What Is Annealing in Metalworking, Really?
You've likely heard the term "annealing" in relation to metals, but what does it actually involve? Why is this process so fundamental in metalworking and manufacturing?
Annealing is a heat treatment process that changes a material's internal structure by heating it to a specific temperature and then slowly cooling it, primarily to soften it.
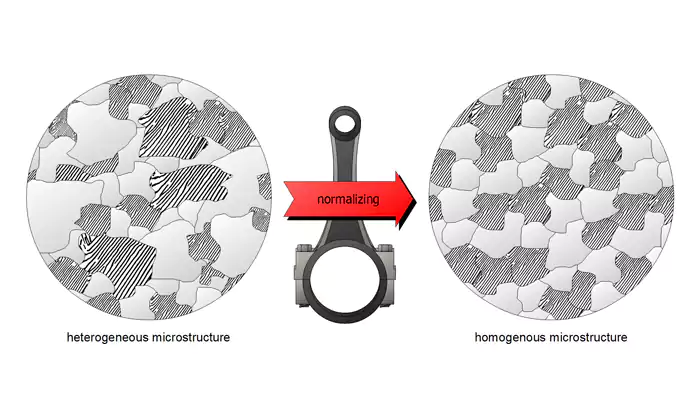
Diving Deeper into the Definition of Annealing
Annealing, at its core, is a type of heat treatment applied to metals and some other materials like glass. Its main purpose is to alter the physical and sometimes chemical properties of the material to achieve a desired outcome. Most commonly, especially in metalworking, annealing is used to make the material softer and more ductile1 (meaning it can be stretched or drawn out without breaking easily).
When a metal is worked – for example, by rolling, drawing, or even heavy machining – it can become harder, more brittle, and develop internal stresses. Annealing essentially reverses these effects. It involves heating the metal to a carefully controlled temperature, holding it there for a specific duration (this is called soaking), and then cooling it down slowly. This controlled thermal cycle allows the material’s microstructure to change. New, stress-free grains can form, and existing grains can grow, leading to a softer, more uniform internal structure.
As my insight suggests, it's a fundamental process for making metal easier to work with. For David, specifying an annealed condition for a material before complex machining can mean better tool life, improved surface finish on the final part, and reduced risk of unexpected material behavior during fabrication. It's about preparing the material for subsequent operations.
How Does the Annealing Process Actually Work?
We know annealing involves heating and slow cooling, but what's happening inside the metal? Understanding the mechanism helps appreciate why it changes material properties so effectively.
Annealing works by heating metal above its recrystallization temperature, allowing new, strain-free grains to form. Slow cooling prevents re-hardening, resulting in a softer, more ductile structure.
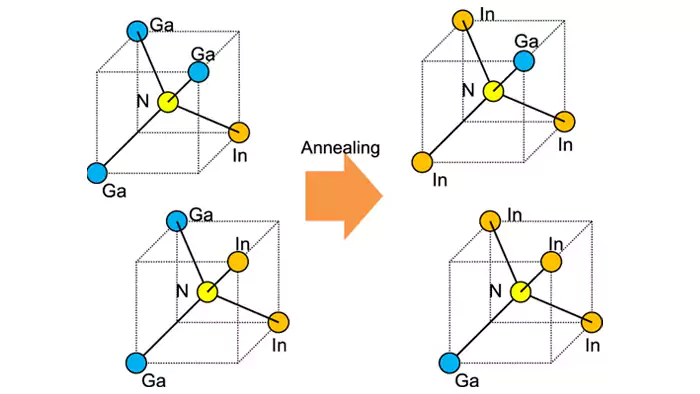
Diving Deeper into the Science of Annealing
The magic of annealing lies in how it manipulates the microstructure of the metal at an atomic level. When a metal is cold-worked (deformed at a temperature below its recrystallization point), its internal crystal structure becomes distorted. The tiny crystals, or grains, get elongated, and the number of imperfections, called dislocations, increases dramatically. These dislocations hinder further movement within the crystal lattice, which is why the metal becomes harder and more brittle.
Annealing addresses this through a few key stages:
-
Recovery: As the metal is first heated, some internal stresses are relieved. The dislocations begin to move and arrange themselves into lower-energy configurations. The material might become slightly softer, but the main grain structure hasn't changed much yet.
-
Recrystallization2: This is the most crucial stage. As the temperature continues to rise above the material's specific recrystallization temperature, new, small, strain-free grains start to form within the heavily deformed structure. These new grains grow and eventually consume the old, distorted grains. The density of dislocations drops significantly.
-
Grain Growth3: If the metal is held at the annealing temperature for too long, or if the temperature is too high, these new, stress-free grains can continue to grow larger. While this further softens the material, excessively large grains can sometimes be undesirable as they might lead to a rough surface finish after forming operations (known as an "orange peel" effect).
The slow cooling part is vital. If the metal were cooled too quickly (quenched), it could re-harden, especially for steels. Slow cooling allows the microstructure to stabilize in its softest, most ductile state, preventing the formation of harder phases. This controlled thermal cycle essentially gives the metal a "reset," relieving stresses and restoring its workability.
Is Annealing Considered a Hardening or Softening Process?
With various heat treatments available, it's easy to get confused. Is annealing aimed at making metals harder and stronger, or does it achieve the opposite effect?
Annealing is fundamentally a softening process. Its primary aim is to reduce hardness, increase ductility, and relieve internal stresses, making the metal easier to work with.
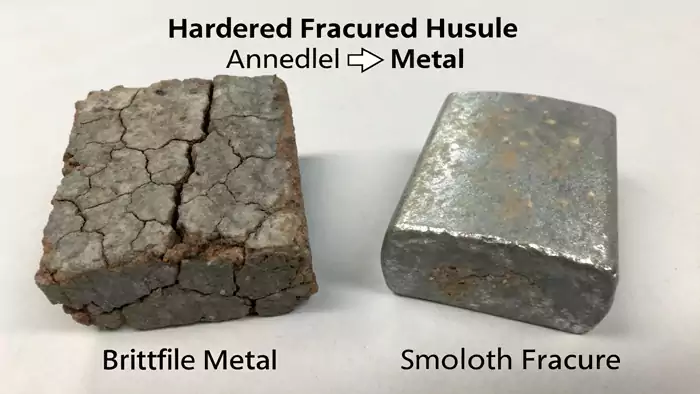
Diving Deeper into Annealing's Effect on Hardness
This is a very straightforward distinction: annealing is almost always a softening process. Its entire purpose revolves around making a metal less hard, more ductile (easier to deform without fracturing), and relieving internal stresses. My insight directly points this out – it softens metal.
To understand why it's a softening process, we need to contrast it briefly with hardening processes, particularly for steels:
- Hardening: This process involves heating steel to a high temperature (austenitizing temperature) and then cooling it very rapidly (quenching) in a medium like water or oil. This rapid cooling traps carbon in a highly stressed, distorted crystal structure called martensite, which is very hard and brittle.
- Annealing: This process also involves heating, often to a similar or slightly different temperature range depending on the specific annealing type and material. However, the key difference is the slow cooling rate. By cooling slowly, the atoms have time to arrange themselves into a more stable, lower-energy, and less stressed configuration, resulting in softer microstructures like ferrite and pearlite in steels.
So, while both involve heating, the cooling rate is the critical differentiator that determines whether you get a hard or a soft material. If David specifies a material for a part that needs to undergo significant bending or forming before final machining, he would want it in an annealed (soft) condition. If the final part needs to be very hard and wear-resistant, a hardening (and subsequent tempering) process would be specified after most of the shaping is done. There's no ambiguity here; annealing is for softening and improving workability.
What Are the Main Purposes and Benefits of Annealing?
Why go through the trouble of annealing metal? This heat treatment offers several crucial advantages that can significantly improve material properties and manufacturability for various applications.
Annealing relieves internal stresses, softens metals, increases ductility and toughness, refines grain structure, and improves machinability. This leads to better forming, reduced cracking, and enhanced part quality.
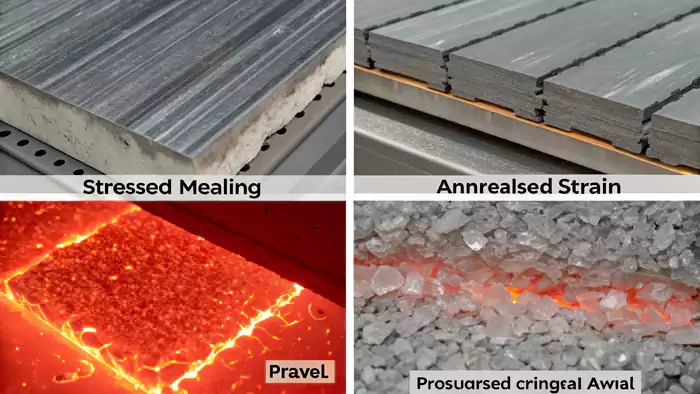
Diving Deeper into Annealing's Advantages
Annealing is a versatile heat treatment process employed for several important reasons, all contributing to improved material characteristics and easier downstream processing. As I mentioned in my insights, understanding these benefits can really enhance the quality and longevity of components.
Key Purposes and Benefits:
-
Stress Relief:
- Purpose: To reduce or eliminate internal stresses that may have been induced by processes like cold working (rolling, drawing, bending), welding, casting, or even heavy machining.
- Benefit: Relieving these stresses prevents unwanted dimensional changes (warping) during subsequent machining or over time, reduces the risk of stress corrosion cracking, and improves the overall stability of the part.
-
Softening and Increasing Ductility:
- Purpose: To reduce hardness and increase the material's ability to deform plastically without fracturing.
- Benefit: This is crucial for making the material easier to cold work (e.g., bend, stamp, draw into wire). It allows for more extensive deformation before the material work-hardens too much and requires another annealing cycle. This directly aligns with my insight about making metal easier to work with.
-
Improving Machinability:
- Purpose: To alter the microstructure to one that is more favorable for cutting operations.
- Benefit: Softer, more uniform materials generally machine more easily, leading to better tool life, faster machining speeds, improved surface finish, and reduced cutting forces. For a CNC machining shop like Allied Metal, this is a huge plus.
-
Refining Grain Structure:
- Purpose: To create a more uniform and finer grain size, or sometimes a specific desired grain structure.
- Benefit: A refined grain structure typically improves toughness and can enhance the consistency of mechanical properties throughout the material.
-
Improving Toughness:
- Purpose: While primarily a softening process, certain annealing cycles can improve a material's toughness (its ability to absorb energy and deform before fracturing).
-
Homogenizing Microstructure:
- Purpose: To eliminate chemical segregation or non-uniformities in the microstructure that may have occurred during casting or other processes.
- Benefit: Results in more consistent properties throughout the material.
For an engineer like David, specifying annealing where appropriate means he can design parts that are not only manufacturable but also possess the desired final properties for their intended service conditions.
What Is the Typical Process of Annealing Metal?
We know annealing involves heating and slow cooling, but what are the distinct stages? Understanding the step-by-step process highlights the control needed for effective results.
The annealing process consists of three main stages: heating the metal slowly to a specific temperature, soaking (holding) it at that temperature, and then cooling it slowly.
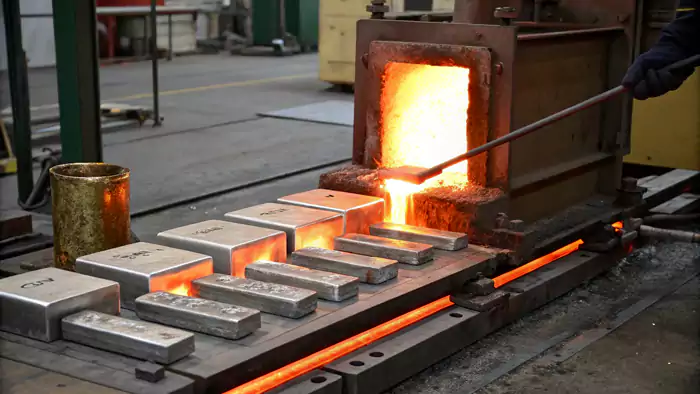
Diving Deeper into the Annealing Cycle
The annealing process, while varying in specific temperatures and times depending on the metal or alloy, generally follows a well-defined three-stage cycle. Getting each stage right is critical to achieving the desired properties.
-
Heating (Recovery and Recrystallization Stage Start):
- The metal is heated slowly and uniformly to the predetermined annealing temperature. The rate of heating is important; heating too quickly can cause thermal stresses and potential warping, especially in large or complex parts.
- The target temperature is critical. It must be high enough to allow the desired microstructural changes (like recrystallization) to occur. For many steels, this is above their upper critical temperature (A₃ or Acm) for full annealing, or between the lower (A₁) and upper critical temperatures for processes like spheroidizing or process annealing. For non-ferrous metals, it's above their specific recrystallization temperature.
-
Soaking (Holding at Temperature / Recrystallization Completion and Grain Growth Stage):
- Once the entire mass of the metal has reached the desired annealing temperature, it is held (or "soaked") at that temperature for a specific period.
- The purpose of soaking is to ensure that the temperature is uniform throughout the part and to allow sufficient time for the necessary metallurgical transformations to complete. This includes the completion of recrystallization (formation of new, strain-free grains) and, in some cases, the dissolution of certain phases or homogenization of the structure.
- Soaking time depends on factors like the material type, the thickness of the part, and the specific type of annealing being performed. Too short a soak may result in an incomplete anneal.
-
Cooling (Transformation Stage):
- This is arguably the most defining stage for annealing. After soaking, the metal is cooled slowly back to room temperature.
- The slow cooling rate is essential to allow the microstructure to transform into its softest, most stable state. For many annealing processes, especially full annealing of steel, this means cooling the part down within the furnace itself after it has been turned off. Other methods include burying the hot part in an insulating material like sand, ash, or vermiculite.
- Rapid cooling (quenching) would generally lead to hardening, which is the opposite of annealing's goal.
Careful control over each of these stages – heating rate, target temperature, soaking time, and cooling rate – is essential for achieving the desired annealed properties consistently.
When Should Annealing Actually Be Used in Manufacturing?
Knowing the "what" and "how" of annealing is important, but when is it practically applied? Understanding its use cases helps in planning manufacturing steps effectively.
Annealing should be used after cold working to restore ductility, before complex machining to improve machinability, to relieve stresses from welding or casting, or to ensure dimensional stability.
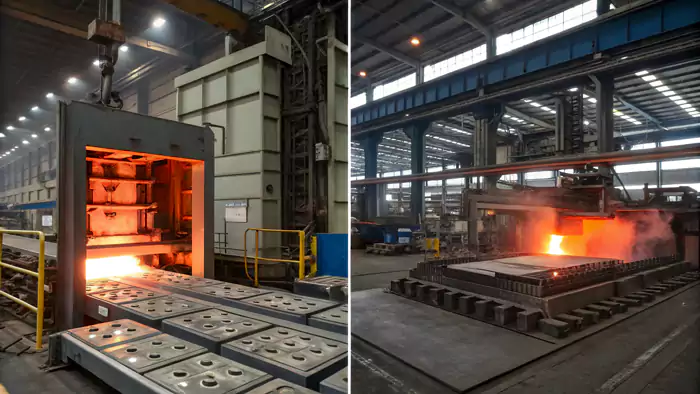
Diving Deeper into Annealing's Strategic Application
Annealing isn't just a random step; it's strategically employed at various points in the manufacturing cycle to prepare materials for subsequent operations or to impart desired final properties. Here are some common scenarios where annealing is beneficial, situations that engineers like David would consider in their design and manufacturing specifications:
-
After Cold Working:
- Metals become harder and more brittle (work-hardened or strain-hardened) when they are deformed at room temperature (e.g., through rolling, drawing, stamping, or bending). If further deformation is needed, the material might crack.
- Use Case: Annealing is performed as an intermediate step to soften the material, restore ductility, and allow for additional cold working operations without failure. This is common in wire drawing or sheet metal forming.
-
Before Machining:
- Some materials, especially certain alloy steels or tool steels, might be supplied in a relatively hard condition or might have work-hardened during previous processing.
- Use Case: Annealing (specifically types like spheroidize annealing for high-carbon steels) is used to soften the material and create a microstructure that is easier to machine. This improves tool life, reduces cutting forces, and can lead to a better surface finish. This directly relates to my insight about making metal easier to work with.
-
To Relieve Internal Stresses:
- Stresses can be introduced from casting, welding, heavy machining, or uneven cooling. These residual stresses can cause warping or distortion over time or during subsequent machining.
- Use Case: Stress relief annealing (which is often done at a lower temperature than full annealing) is used to reduce these internal stresses, thereby improving dimensional stability and reducing the risk of cracking.
-
To Improve Dimensional Stability:
- For precision components, ensuring the part remains dimensionally stable throughout its service life and during final machining is crucial.
- Use Case: Annealing can help by relieving stresses and homogenizing the microstructure, minimizing the chances of unexpected size or shape changes later.
-
To Modify Electrical or Magnetic Properties:
- For some materials, annealing can alter electrical conductivity or magnetic permeability to meet specific application requirements. For example, annealing copper can improve its conductivity.
Deciding when to anneal involves understanding the material's history, the subsequent manufacturing steps, and the final performance requirements of the part.
What Are Some Common Applications of Annealing?
Where do we see the impact of annealing in everyday products or industrial components? Knowing its applications highlights the broad utility of this fundamental heat treatment.
Annealing is used in producing sheet metal for car bodies, drawing electrical wires, manufacturing soft drink cans, preparing tool steels for machining, and treating forgings and castings.
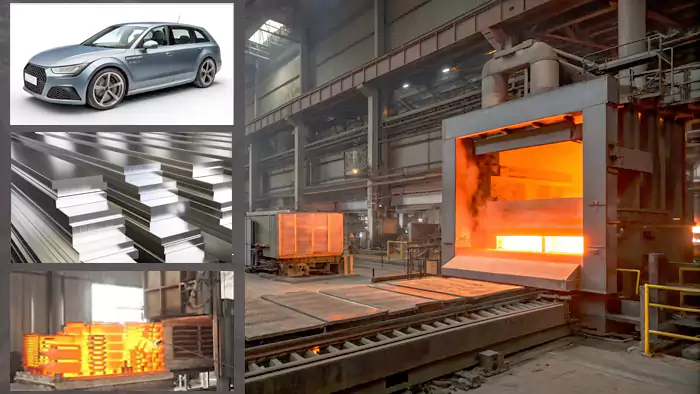
Diving Deeper into Real-World Examples
Annealing is a workhorse process in metalworking, found across a vast array of industries and applications. Its ability to soften metals and improve their workability makes it indispensable.
Here are some key application areas:
-
Sheet Metal Fabrication:
- Steel and aluminum sheets used for car bodies, appliance casings, and beverage cans undergo annealing. This makes them ductile enough to be pressed, stamped, and deep-drawn into complex shapes without cracking. Multiple annealing steps might be needed between forming operations.
-
Wire Drawing:
- To produce wires, a metal rod is pulled through successively smaller dies. This cold working process hardens the wire. Intermediate annealing is performed to soften the wire so it can be drawn further to achieve the final desired diameter. This is critical for copper electrical wires, for example.
-
Forgings and Castings:
- After metal parts are forged or cast, they often have coarse or non-uniform microstructures and significant internal stresses. Annealing is used to refine the grain structure, improve toughness, relieve stresses, and ensure the parts are suitable for subsequent machining or use.
-
Tool Steels and Alloy Steels:
- Tool steels are often supplied in an annealed condition to make them easier for toolmakers to machine into dies, punches, or cutting tools. After machining, these tools are then hardened and tempered to achieve their required service properties. For an engineer like David designing specialized tooling, this is a common cycle.
-
Piping and Tubing:
- Seamless pipes and tubes, especially those made from stainless steel or copper alloys, are often annealed to relieve stresses from manufacturing and improve their formability for bending and installation.
-
Ammunition Casings:
- Brass casings for bullets undergo several drawing and annealing steps to achieve their final shape and ensure they can withstand the pressures of firing.
-
Improving Machinability of Components:
- As I've emphasized, many components that need to be precisely machined are first annealed. This not only makes machining easier but also ensures that the material is in a stable condition, minimizing distortion during the removal of material. My shop, Allied Metal, often receives materials specified in an annealed state for this very reason.
These examples show just how vital annealing is for producing a vast range of metal goods efficiently and reliably.
Can Annealing Be Used Effectively with Metal Alloys?
We've talked about annealing metals, but what about alloys? Are these mixtures of metals also suitable for annealing, and does the process differ for them?
Yes, annealing is extensively used with almost all metal alloys, including steels, aluminum alloys, copper alloys, and titanium alloys. The specific annealing temperatures and procedures vary significantly by alloy.
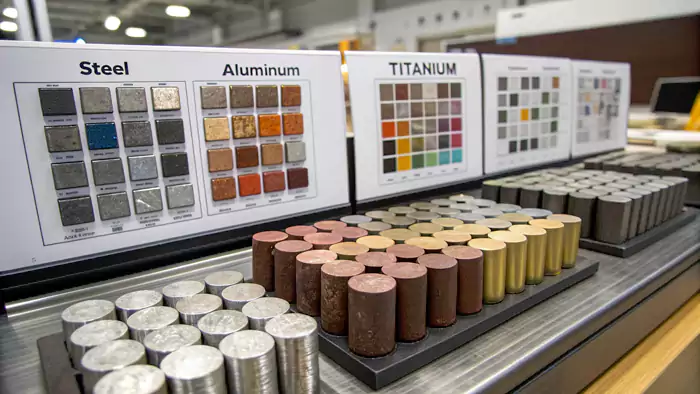
Diving Deeper into Annealing Alloys
Annealing is not just for pure metals; it's a critically important heat treatment for a vast range of metal alloys. In fact, many alloys require specific annealing treatments to optimize their properties for various applications. An alloy is a mixture of a metal with other elements (either metals or non-metals), and these additions can significantly change how the material responds to heat treatment.
Here's how annealing applies to some common alloy groups:
- Steels (Carbon and Alloy Steels): Annealing is fundamental for steels. Different types of annealing processes (full anneal, process anneal, spheroidize anneal, stress relief anneal) are used to achieve specific microstructures, softness levels for machining or forming, or to relieve stresses. The presence of alloying elements like chromium, nickel, molybdenum, etc., will influence the critical temperatures and required cooling rates.
- Aluminum Alloys: Many aluminum alloys, especially those that are work-hardenable or precipitation-hardenable, are annealed. Annealing can soften work-hardened aluminum, making it suitable for further forming. For heat-treatable aluminum alloys (like the 6000 or 7000 series David might use), annealing can dissolve precipitates and create a softer, more homogeneous structure prior to solution treatment and aging.
- Copper Alloys (Brass, Bronze): These alloys readily work-harden. Annealing is essential to restore ductility after cold working operations like drawing or stamping. The annealing temperatures are generally lower than for steels.
- Nickel Alloys: High-performance nickel superalloys used in aerospace or chemical processing often undergo complex heat treatment cycles that can include various annealing steps to control grain size, relieve stress, and optimize mechanical properties.
- Titanium Alloys: Titanium alloys also benefit from annealing to relieve stresses induced during forging or machining, to improve fracture toughness, or to stabilize the microstructure.
The key takeaway is that while the principles of annealing (heating, soaking, slow cooling) remain the same, the exact parameters – temperatures, soak times, and cooling methods – must be carefully tailored to the specific alloy composition. Using incorrect parameters can lead to undesirable microstructures or properties. This is where material science expertise really comes into play, ensuring the treatment enhances the material as intended.
Conclusion
Annealing softens metals, enhances ductility, and relieves stress through controlled heating and cooling. This vital process improves workability, quality, and component longevity in manufacturing.
-
Learning about ductility helps in understanding how materials behave under stress, which is essential for effective metalworking. ↩
-
Understanding recrystallization is essential for optimizing metal properties and improving manufacturing processes. ↩
-
Exploring grain growth helps in understanding its impact on material strength and surface finish, crucial for engineering applications. ↩