I’ve spent over 20 years in CNC machining, often making custom fasteners. Fasteners may be small, but picking the wrong one can cause huge problems in your design or assembly process.
The 7 common types of fasteners are screws, bolts, nuts, rivets, washers, nails, and anchors, each serving different mechanical or structural needs.

When I first started my CNC machining business, I thought fasteners were just simple hardware. Boy, was I wrong. These small components make the difference between a successful product and a complete failure. Let me walk you through each type and share what I've learned from years of manufacturing custom fasteners for clients worldwide.
What Are Fasteners?
Loose parts cause dangerous failures. Your assembly could literally fall apart. Fasteners solve this by joining materials securely.
A fastener is a hardware device that mechanically joins or affixes two or more objects together. They create non-permanent or permanent joints, essential for assembly in nearly all industries.
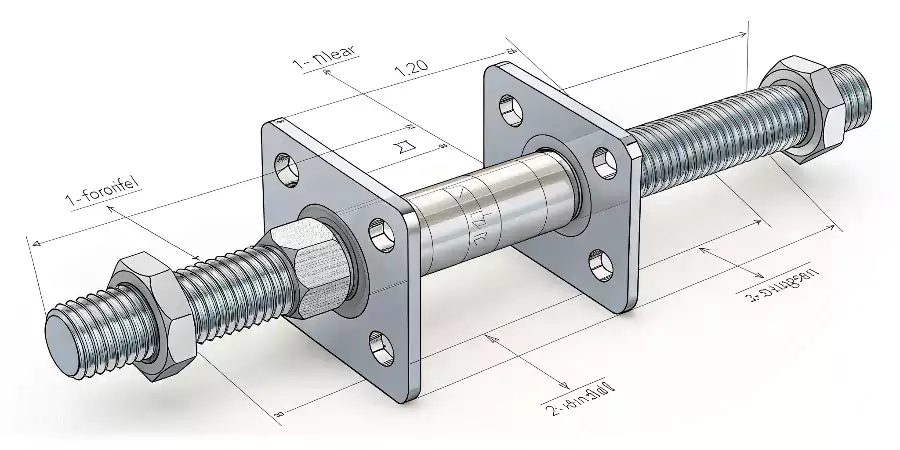
Functions and Materials
Fasteners can be threaded or non-threaded, depending on how they work. Some allow for removal and reuse, while others create a permanent joint. They are made from materials like steel, stainless steel, brass, titanium, or nylon, based on strength, corrosion resistance, and environment.
Fastener Type | Temporary or Permanent | Common Materials |
---|---|---|
Screw | Temporary | Steel, Stainless Steel |
Bolt | Temporary | Steel, Alloy Steel |
Nut | Temporary | Brass, Stainless Steel |
Rivet | Permanent | Aluminum, Steel |
Washer | Temporary | Stainless Steel, Nylon |
Nail | Permanent | Steel, Galvanized Steel |
Anchor | Temporary | Zinc, Plastic, Nylon |
Understanding Fastener Basics
Fasteners work through various mechanisms. Some use threading to create mechanical advantage. Others rely on friction, compression, or material deformation. The key is matching the fastener type to your specific application needs.
I remember working on a project for an aerospace client who needed fasteners that could withstand extreme temperatures. Regular hardware store fasteners simply wouldn't cut it. We had to machine custom titanium fasteners1 with precise tolerances. This experience taught me that not all fasteners are created equal.
The material selection matters enormously. Steel fasteners offer strength and durability. Stainless steel provides corrosion resistance. Aluminum fasteners reduce weight. Titanium delivers exceptional strength-to-weight ratios. Each material serves different purposes based on environmental conditions and load requirements.
Material | Strength | Weight | Corrosion Resistance | Cost |
---|---|---|---|---|
Steel | High | Heavy | Low | Low |
Stainless Steel | High | Heavy | High | Medium |
Aluminum | Medium | Light | Medium | Medium |
Titanium | Very High | Light | Very High | High |
What Are the Different Types of Fastening?
We know fasteners join things together. But is that the only way? What are the different methods of fastening used in engineering and manufacturing?
The main types of fastening are mechanical fastening (using fasteners like bolts), welding or soldering (creating a metallurgical bond), and adhesive bonding (using glues or epoxies).
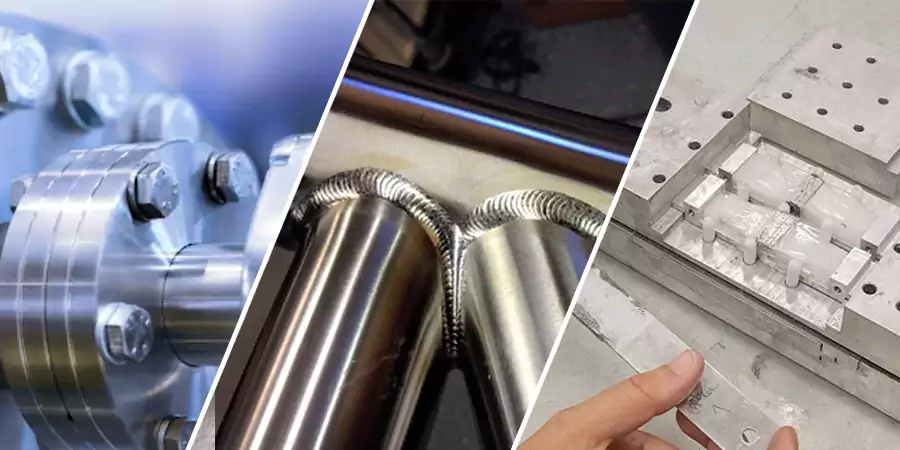
Diving Deeper into Fastening Methods
While this article focuses on mechanical fasteners, it's important for an engineer like David to understand that fastening—the act of joining objects—can be achieved in several different ways. The method chosen depends on factors like the materials being joined, the required strength, whether the joint needs to be permanent, and cost.
Here are the main categories of fastening:
1. Mechanical Fastening2
- Description: This method uses physical hardware (fasteners) to create a joint. The parts are typically held together by clamping force or an interlocking physical shape.
- Examples: Using bolts and nuts, screws, rivets, or clips.
- Advantages: Usually allows for disassembly (non-permanent), does not damage materials with heat, and provides reliable and predictable strength. This is the category our 7 main types of fasteners fall into.
2. Welding, Brazing, and Soldering
- Description: These methods join materials, typically metals, by melting them together. A filler material is often used to create a strong, permanent metallurgical bond.
- Examples: MIG welding steel frames, soldering electronic components to a circuit board.
- Advantages: Creates very strong, permanent, and often seamless joints. It's excellent for creating large, unified structures.
3. Adhesive Bonding
- Description: This method uses chemical adhesives, like glues or epoxies, to bond two surfaces together.
- Examples: Gluing wood in furniture making, bonding composite panels on an aircraft, or using threadlocker on a screw.
- Advantages: Can join dissimilar materials, distributes stress over a wide area, and can provide a clean, invisible joint.
Each method has its place. However, mechanical fastening with devices like screws, bolts, and nuts remains the most common and versatile method for assembling mechanical products, from consumer electronics to large-scale industrial machinery.
What Are the Different Types of Fasteners Used in Manufacturing?
What are the foundational hardware components that hold our machines and structures together? What are the main categories every engineer and machinist should know?
The manufacturing industry makes extensive use of all fastener types. Screws lead in electronic assembly. Bolts lead in structural framing. Nails are used in wood construction. Anchors secure heavy machinery bases. Each serves a unique purpose in creating strong and reliable mechanical joints.
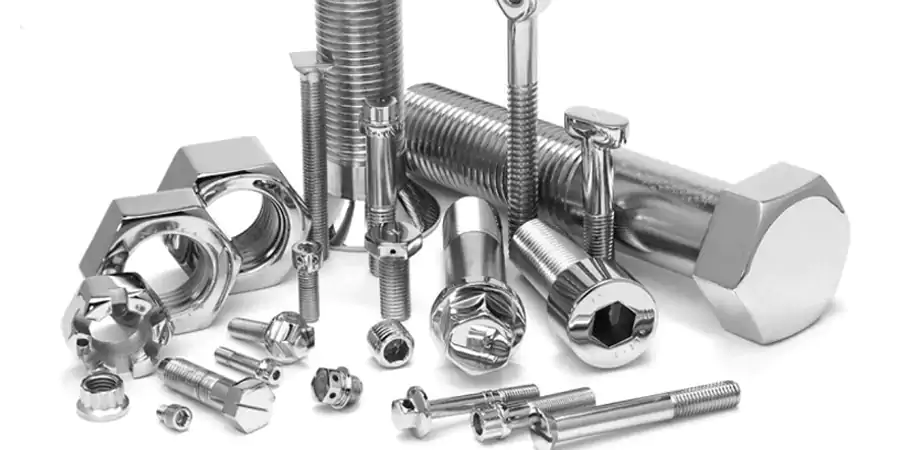
Diving Deeper into the 7 Main Fastener Types
These seven categories cover the vast majority of fasteners used in manufacturing and construction. Understanding the specific role of each is critical for a designer like David.
-
Screws:
- A screw is a fastener with a threaded shaft that is designed to cut its own thread into a material as it is turned. They are used to join objects together when you only have access to one side, or when joining into a soft material like wood or plastic.
-
Bolts:
- A bolt is a fastener with a threaded shaft that is designed to be used with a nut. It does not cut its own thread. Instead, it passes through unthreaded holes in two or more parts and is secured by tightening a nut, which creates a clamping force.
-
Nuts:
- A nut is a fastener with a threaded hole. It is almost always used in conjunction with a matching bolt to fasten multiple parts together. The nut's internal threads mate with the bolt's external threads.
-
Washers:
- A washer is typically a thin, flat disc with a hole in the middle. It is not a fastener on its own but is a critical companion component. Its main purpose is to distribute the load of a threaded fastener, preventing damage to the surface of the part being joined. Lock washers also help prevent a nut or bolt from loosening due to vibration.
-
Rivets:
- A rivet is a permanent mechanical fastener. It consists of a smooth cylindrical shaft with a head on one end. To install it, the plain end is passed through holes in two parts, and then that end is upset, or "bucked," to form a second head, permanently clamping the parts together.
-
Nails:
- A nail is a pin-shaped fastener, typically made of steel, used in woodworking and construction. It is driven into the workpiece with a hammer or nail gun and holds parts together primarily through friction and shear strength.
-
Anchors:
- An anchor is a type of fastener designed to be inserted into a material like concrete or drywall, where a standard screw would not hold. The anchor expands inside the material to create a secure mounting point for a screw.
What Are Some Common Metal Fasteners?
What materials are most fasteners made from? When you need a metal fastener, what are the common options and what are their different strengths?
Common metal fasteners include steel screws, stainless steel bolts, aluminum rivets, brass screws, and titanium fasteners. Each metal offers specific advantages like corrosion resistance, strength, or weight reduction for different applications.
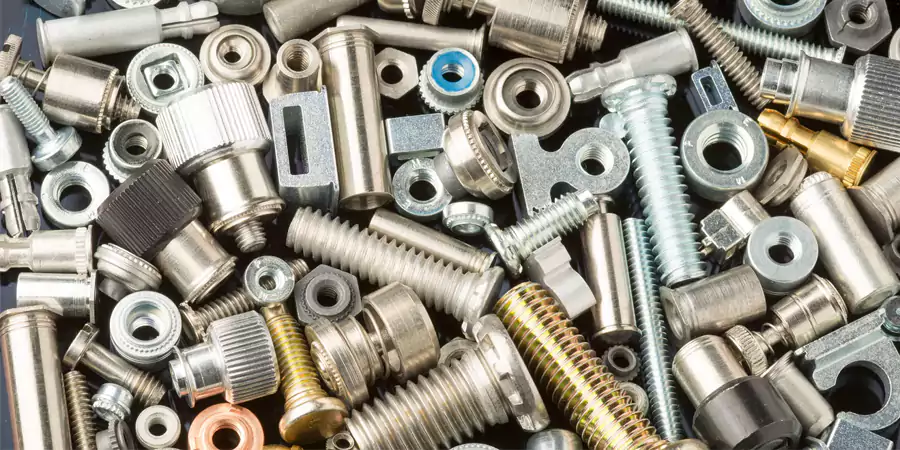
Diving Deeper into Metal Fastener Materials
The material of a fastener is just as important as its shape. It dictates the fastener's strength, durability, and suitability for different environments. For an engineer like David working on industrial automation, choosing the right material is critical for long-term reliability.
Here are some of the most common metals used:
-
- Description: This is by far the most common material for fasteners due to its excellent strength and low cost. Steel fasteners are often coated with zinc, chrome, or another finish to improve corrosion resistance.
- Grades: They come in different strength grades (like Grade 2, 5, 8 in the SAE system, or Class 8.8, 10.9 in metric). Higher grades mean higher tensile strength.
- Use: General-purpose construction, automotive, and machinery assembly.
-
- Description: A steel alloy containing chromium, which gives it excellent corrosion resistance without needing a coating.
- Grades: The most common grades are 18-8 (which includes 304) for general use, and 316 for marine or chemically harsh environments.
- Use: Used in food processing equipment, marine applications, medical devices, and anywhere that resistance to rust is critical.
-
- Description: A lightweight metal with good corrosion resistance. It is not as strong as steel.
- Use: Chosen when weight is a primary concern, such as in aerospace, and for fastening other aluminum parts to prevent galvanic corrosion. It's common in aircraft, race cars, and electronics.
-
Titanium:
- Description: An exceptional material with the strength of steel but at a much lighter weight. It also has outstanding corrosion resistance.
- Use: A high-performance material used in aerospace, racing, and medical implants where a high strength-to-weight ratio is essential. It is significantly more expensive than other materials.
-
Brass and Bronze:
- Description: Copper alloys known for their corrosion resistance and electrical conductivity.
- Use: Often used in electrical applications, plumbing, and marine environments for their resistance to saltwater corrosion.
The choice always involves a trade-off between strength, weight, corrosion resistance, and cost.
Corrosion Resistance vs. Strength
Stainless steel resists rust but is softer than alloy steel. For outdoor use, I always go with stainless. For structural use, hardened carbon steel gives the best strength-to-weight ratio.
Cost vs. Performance
Brass fasteners are great for electrical applications due to conductivity but cost more. Zinc-coated fasteners are budget-friendly and good enough for general use, unless there’s extreme humidity or salt exposure.
What Is the Strongest Special Fastener?
When standard bolts are not enough, what's next? What defines the "strongest" special fastener, and what are some examples of high-strength options?
No single "strongest" fastener exists—it depends on load type. Top contenders include high-strength steel bolts (Like Grade 8/Class 12.9), aerospace titanium rivets, and custom threaded inserts. Material (steel/titanium) and engineering determine ultimate strength.
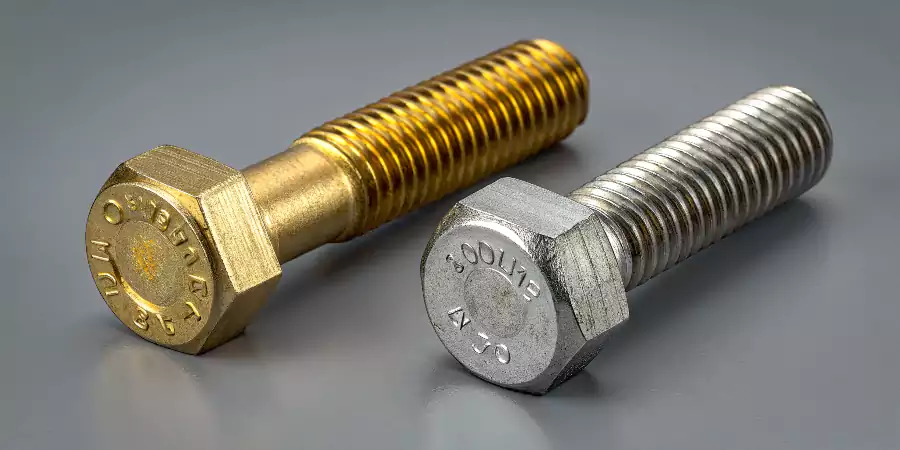
High-Strength Fasteners Explained
The question of the "strongest" fastener is one I hear often. The answer isn't a specific product name but a category of fasteners designed and manufactured to handle extreme loads. For a lead engineer like David, "strength" needs to be defined by the application.
Defining "Strength"
- Tensile Strength: The ability of a fastener to resist being pulled apart. This is the most common measure of bolt strength.
- Shear Strength: The ability to resist forces that are trying to slice the fastener in half, perpendicular to its length.
- Fatigue Strength: The ability to withstand repeated cycles of loading and unloading without failing.
Common High-Strength Steel Bolts
For most industrial and automotive applications, strength is defined by the material grade.
- SAE Grading (US): Standard hardware store bolts are often Grade 2. A Grade 8 bolt is made from quenched and tempered medium carbon alloy steel and is significantly stronger, identifiable by 6 radial lines on the head. This is a common choice for high-stress applications.
- Metric Grading: Standard bolts are often Class 8.8. A Class 10.9 or Class 12.9 bolt offers much higher tensile strength. Class 12.9 is roughly equivalent to or slightly stronger than a Grade 8 bolt3.
Special and Aerospace Fasteners
When you move into the realm of aerospace, you find truly "special" fasteners where performance and reliability are absolute.
- Superalloys: Fasteners can be made from superalloys like Inconel or MP35N, which retain their strength at extremely high temperatures.
- Proprietary Designs: Companies like SPS Technologies create proprietary fasteners (e.g., bolts with multi-phase materials or advanced thread designs) that are engineered for specific, critical applications like holding jet engines together. These are among the strongest fasteners in the world, but they are also incredibly expensive and designed for a single purpose.
So, while a Class 12.9 bolt is one of the strongest commonly available fasteners, the "strongest" fastener is always the one specifically engineered for the most demanding application.
Precision-Machined Fasteners
In custom projects, we often request fasteners made to exact tolerances, especially when they form part of a critical load-bearing assembly. A poorly machined thread can compromise an entire structure.
Extreme environment solutions
Consider these for demanding conditions:
- Inconel bolts: Resist 2000°F temperatures + chemical corrosion
- Huck bolts: Vibration-proof permanent aircraft fasteners
- Hydraulic tensioners: Achieve perfect preload in large diameters
Verification and testing
Proof testing confirms strength claims. Ultrasonic measurement verifies installed tension. Always require certified mill test reports for structural fasteners. Third-party inspection catches material defects early.
How to Obtain a Custom Fastener for Your Applications?
Off-the-shelf fasteners often compromise designs. Ill-fitting parts reduce performance and safety. Custom solutions eliminate these trade-offs.
Submit CAD drawings to CNC machining specialists. Specify materials, tolerances, and quantities. Reputable shops provide DFM feedback and deliver precision fasteners in 2-5 weeks.
Prototyping to production workflow
Follow these steps for custom fasteners:
- Concept validation: 3D printed prototypes test fit/function
- Material testing: Verify strength/compatibility with your components
- Pre-production batch: Test under real operating conditions
- Volume scaling: CNC machining for high precision + consistency
Cost optimization strategies
Reduce expenses without sacrificing quality:
- Standardize thread types: Avoid special tooling charges
- Batch orders: Combine multiple projects
- Secondary ops: Request in-house heat treatment/coating
Conclusion
Fasteners are the essential hardware that joins mechanical parts. Understanding the main types, from screws and bolts to custom-machined variants, is key to successful engineering design and assembly.
-
Explore the advantages of titanium fasteners, including their strength-to-weight ratio and resistance to extreme conditions, ideal for specialized applications. ↩
-
Explore this link to understand the benefits and applications of mechanical fastening in various engineering fields. ↩
-
Explore the specifications of Grade 8 bolts to understand their applications and advantages in high-stress environments. ↩