You need functional prototypes fast without breaking the bank. Time-consuming machining delays projects. FDM 3D printing solves this with quick, affordable plastic parts.
Fused Deposition Modeling (FDM) melts thermoplastic filament layer-by-layer to build objects. It’s also called Fused Filament Fabrication (FFF). This method creates prototypes, tools, and basic end-use parts cheaply and quickly.

The beauty of FDM technology lies in its simplicity and reliability. After working with countless prototyping projects, I've seen how this method bridges the gap between initial design concepts and final CNC machined parts. Let me walk you through everything you need to know about this game-changing technology.
What Is Fused Deposition Modeling (FDM)?
The complexity of modern manufacturing often intimidates newcomers, but FDM breaks down those barriers with its straightforward approach.
FDM, also called Fused Filament Fabrication (FFF), uses a heated nozzle to melt plastic filament and deposit it in precise patterns to create three-dimensional objects from digital designs.
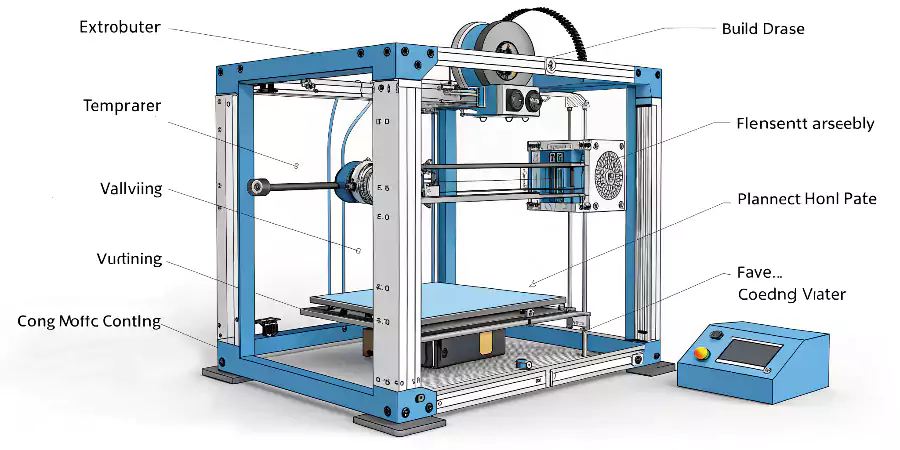
Understanding FDM starts with recognizing its core principle: controlled material deposition1. The process relies on thermoplastic materials that become moldable when heated and solidify when cooled. This fundamental characteristic makes FDM incredibly versatile for prototyping applications.
Core Principles Explained
FDM relies on three key components working together:
- Filament Spool: Plastic feedstock (like PLA or ABS) feeds into the extruder
- Heated Extruder: Melts filament (typically 180-260°C) and controls material flow
- Build Platform: Moves in X/Y/Z axes to position each layer accurately
Material properties change during printing: | Stage | Temperature | Behavior |
---|---|---|---|
Solid Filament | Room temp | Rigid, stable | |
Melted State | 180-260°C | Viscous, flowable | |
Re-solidified | Cooling phase | Bonds to previous layer |
I’ve seen countless engineers underestimate layer adhesion challenges. One client’s drone mount failed because layer bonds couldn’t handle vibration stress. Always consider interlayer strength2 when designing load-bearing FDM parts. Print orientation matters too—vertical builds show weaker layer bonds than horizontal ones.
How Does FDM 3D Printing Work?
From a digital file to a physical object, what are the actual steps? How does an FDM 3D printer translate a computer model into a solid part?
An FDM 3D printer works by feeding a plastic filament through a heated nozzle, melting it, and extruding it onto a build plate. The nozzle moves in a computer-controlled path to build the object layer by layer.

The FDM 3D printing process is a logical workflow that transforms a digital design into a physical object. For an engineer like David who is proficient with CAD, the process is intuitive and easy to integrate into his work.
Step-by-Step Process Breakdown
-
Creating a 3D Model:
- Design a 3D model using CAD software and save it as an STL or STEP file.
-
Slicing the Model:
- Use slicing software to cut the model into thin layers and generate G-code with toolpaths and supports.
-
Printing the Object:
- The printer melts filament and extrudes it layer by layer, moving the nozzle to build each layer.
-
Cooling and Fusing:
- Each layer cools and bonds to the previous one, often helped by cooling fans, until the object is complete.
Once the print is finished and the part has cooled, it can be removed from the build plate. This straightforward method makes FDM 3D printing a fast and effective way to create prototypes.
I once printed a gear assembly at three different speeds. The slowest version meshed perfectly while faster prints jammed. For moving parts, always prioritize precision over speed.
What are the characteristics of FDM 3D printing?
Every manufacturing process has its own unique traits. What are the key characteristics—both good and bad—that define parts made using Fused Deposition Modeling?
The key characteristics of FDM 3D printing are its speed for prototyping, affordability, and wide material choice. However, it has lower dimensional accuracy and visible layer lines compared to other methods.

Understanding the inherent characteristics of FDM 3D printing is crucial for an engineer like David to decide if it's the right process for his project. It's a technology defined by its trade-offs between speed, cost, and quality.
Advantages and Limitations
Key Benefits:
- Cost Efficiency: Machines cost 90% less than industrial 3D printers
- Material Variety: Supports plastics, composites, and flexible filaments
- Ease of Use: Minimal training required for operation
Common Drawbacks:
- Anisotropic Strength: Z-axis weakness due to layer adhesion
- Surface Quality: Visible layer lines require post-processing
- Tolerance Limits: ±0.5% dimensional accuracy (lower than CNC)
For a robotics project, we used FDM for sensor mounts but switched to CNC for gear components. Match the technology to your part’s function—FDM excels when cost and speed outweigh precision needs.
What are common materials for FDM 3D printing?
What kind of plastics are used in FDM printers? What are the most common filaments, and what are their different properties and uses?
Common FDM materials include PLA for ease of use and prototyping, ABS for durability and heat resistance, PETG for a balance of strength and flexibility, and TPU for flexible, rubber-like parts.
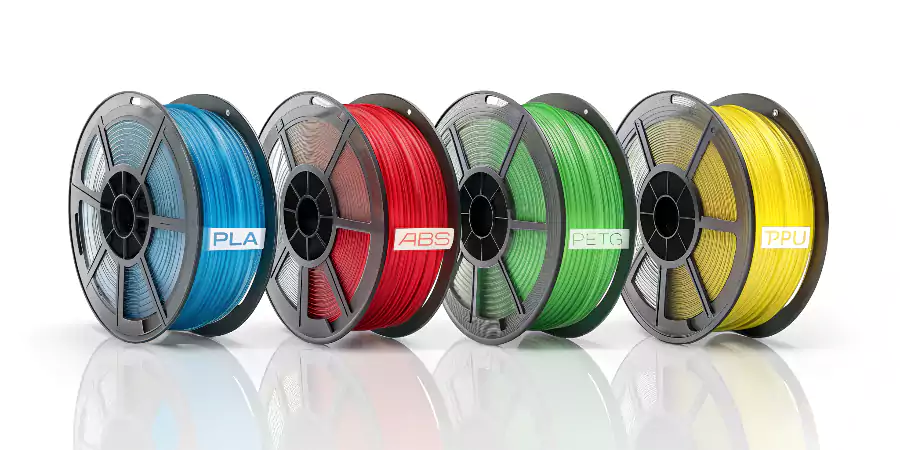
Fused Deposition Modeling becomes even more powerful thanks to the wide variety of thermoplastic filaments available. Each filament has its own strengths, making it ideal for specific use cases. For engineers like David, selecting the right material is crucial to building a functional and reliable prototype.
Material Comparison Guide
Material | Strength | Heat Resist. | Best For | Limitations |
---|---|---|---|---|
PLA | Medium | Low (60°C) | Prototypes, decorative parts, low-stress models | Brittle, low durability |
ABS | High | Medium (80°C) | Functional parts, enclosures, automotive parts | Warping, fumes when printing |
PETG | High | Medium (75°C) | Outdoor use, mechanical parts, water-resistant applications | Stringing during print |
TPU | Flexible | Medium (70°C) | Gaskets, seals, phone cases, shock-absorbing parts | Slow printing, requires tuning |
Nylon | Very High | High (100°C) | Gears, bearings, mechanical parts, hinges | Absorbs moisture, requires high temp |
PC (Polycarbonate) | Very High | Very High (110–130°C) | Structural parts, high-temperature environments, tooling | Needs high print temps, prone to warping |
HIPS | Medium | Medium (80°C) | Support material (with ABS), lightweight models | Requires dissolving agent (limonene) |
ASA | High | Medium-High (95°C) | Outdoor parts, automotive, UV-resistant products | More expensive than ABS |
PVA | Low | Low (60°C) | Water-soluble support structures | Not suitable as a main material |
Moisture is a big enemy in 3D printing—especially with engineering plastics. I always keep filaments in dry boxes to avoid weak prints and nozzle jams. For most projects, PETG is my go-to. It’s strong like ABS but much easier to print. One of my clients even cut enclosure costs by 30% after switching to PETG.
What Post-processing is Done for FDM 3D printing?
An FDM print is rarely perfect right off the printer. What are the common post-processing steps used to clean up, strengthen, or improve the appearance of FDM parts?
FDM post-processing includes support removal, surface smoothing through sanding or chemical treatment, and assembly preparation through drilling, tapping, or threaded insert installation for functional applications.
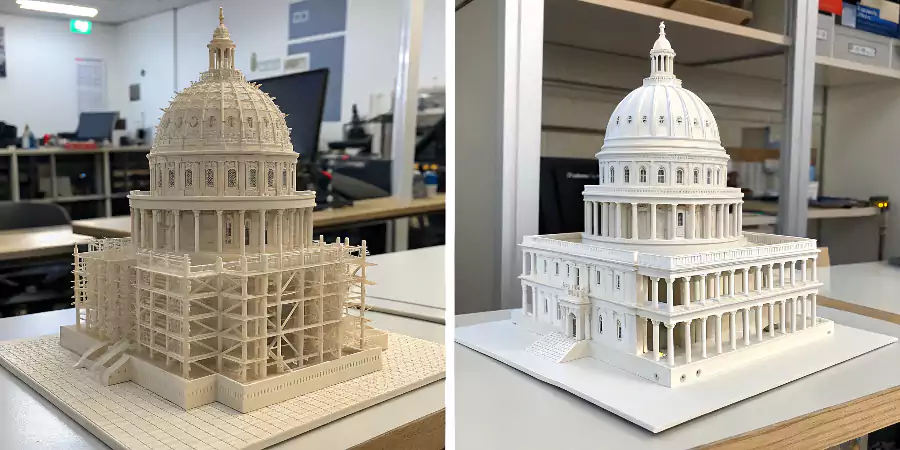
Diving Deeper into FDM Finishing Techniques
Once an FDM 3D print is finished, it often requires some post-processing work to transform it from a raw prototype into a finished-looking part suitable for presentation or functional testing. For David, knowing these techniques is useful for understanding the final quality that can be achieved.
Here are the most common post-processing steps for FDM parts:
-
Support Removal:
- This is the first and most basic step. FDM printers build support structures to hold up any overhanging features during printing. These supports must be carefully broken or cut away from the main part.
- Some printers use dissolvable supports (made from materials like PVA or HIPS), which can be dissolved in a liquid bath, leaving behind a much cleaner surface on the part.
-
Sanding and Filling:
- To get rid of the visible layer lines characteristic of FDM printing, the part can be manually sanded. This is usually done by starting with a coarse grit sandpaper and progressively moving to finer grits.
- For a perfectly smooth surface, a sandable filler primer (like that used for automotive body work) can be applied to fill in the layer lines before the final sanding.
-
Priming and Painting:
- Once the part is smooth, it can be primed and painted just like any other plastic model. This is the best way to achieve a professional, high-quality cosmetic appearance and to apply custom colors and finishes (matte, gloss, metallic).
-
- This technique is specific to certain materials. For ABS parts, exposure to acetone vapor in a controlled environment will slightly melt the surface of the print. This causes the layer lines to blend together, resulting in a very smooth, glossy, injection-molded look. This process also improves the strength of the part.
These post-processing steps can significantly improve the quality of FDM prints, elevating them from simple prototypes to presentation-quality models.
Why is FDM so cheap?
Compared to other manufacturing methods, FDM 3D printing is incredibly accessible. What are the key reasons behind the low cost of FDM machines and materials?
FDM is cheap due to the simplicity of its mechanical design, the expiration of key patents which spurred open-source development, and the low cost of producing thermoplastic filament materials at scale.
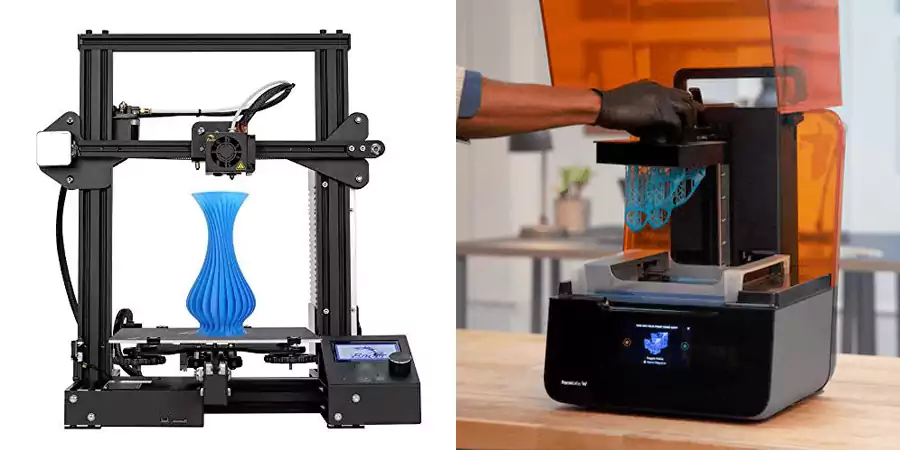
Understanding the Economics of FDM
Fused Deposition Modeling (FDM) is popular mainly because it's low-cost. Its affordability comes from three key factors:
1. Simple Hardware
FDM printers use a basic setup:
- Frame and motion system (motors, belts, rods)
- Heated nozzle (hotend) and extruder
- Build plate and basic electronics
Unlike SLA or SLS, there are no lasers, resin vats, or powder systems—making FDM machines much cheaper to produce.
2. Open-Source Origins
When key patents expired in the late 2000s, the open-source RepRap project4 led to a wave of innovation.
- Free hardware/software designs were shared globally.
- Community efforts rapidly improved printer quality and cut costs.
- This drove the rise of affordable desktop FDM printers.
3. Low Material Costs
FDM uses common thermoplastics like PLA and ABS:
- Mass-produced and inexpensive
- Easy to process into filament
Compared to resins or metal powders, FDM filament is far more affordable.
FDM Cost Breakdown
Hardware
- Minimal components
- Mass-produced parts
Operation
- Filament: $20–50/kg vs. resins at $100+/kg
- No special environment needed
- Low power use (<100W)
Market
- Open patents boost competition
- Community-driven innovation
- Global supply lowers prices
Together, simple design, open development, and cheap materials make FDM a cost-effective choice for engineers and makers alike.
Conclusion
FDM 3D printing offers a cost-effective way to produce functional prototypes quickly. With its wide material compatibility, fast turnaround, and low setup cost, it has become a vital tool for rapid iteration and early-stage product development.
-
Understanding controlled material deposition is crucial for optimizing FDM processes and improving print quality. ↩
-
Learning about interlayer strength is essential for designing robust and reliable 3D printed parts. ↩
-
Discover the benefits of chemical vapor smoothing for achieving a glossy finish and enhanced strength in your prints. ↩
-
Explore the RepRap project to understand its significant impact on 3D printing innovation and affordability. ↩