What is Grooving Machining: Processes, types, tools, materials and main challenges
- March 21, 2025
- Tony
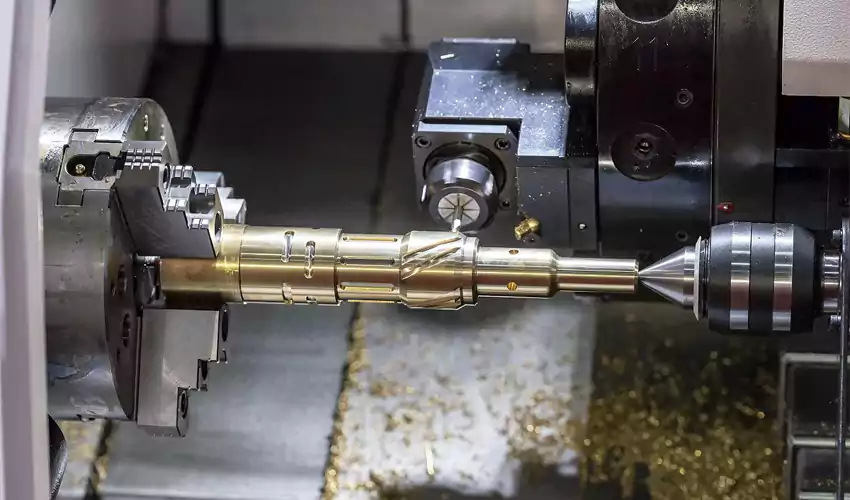
1. What is grooving machining?
What is grooving machining?
Grooving machining is a machining process that utilizes a cutting tool on a CNC lathe to groove a workpiece to achieve preset groove widths, depths and shapes.
Machining process
Roughing stage:
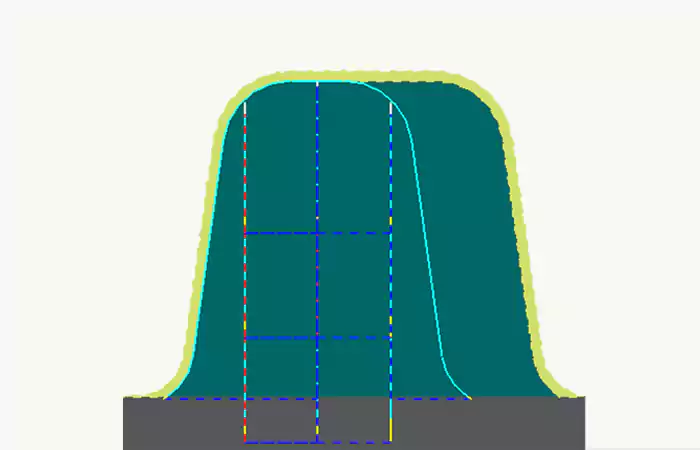
The grooving tool has a sharp cutting edge and a strong body during roughing to efficiently remove a large amount of material and quickly cut the workpiece into approximate shapes and sizes.
Finishing stage:
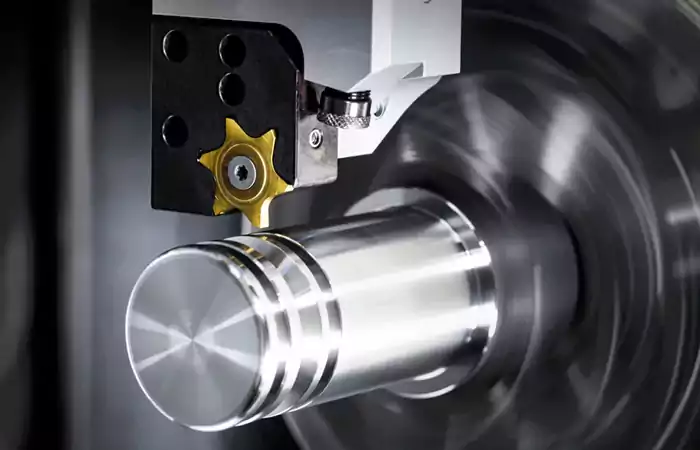
During the finishing process, grooving tools rely on precise cutting edges and a stable structure to achieve high-precision cutting, thus ensuring the final dimensions and excellent surface quality of the workpiece.
Areas of application
Grooving is widely used in the fields of machining, automobile manufacturing, bearing processing, electronic manufacturing, etc. It is especially suitable for the processing of oil grooves, water grooves and other groove structures in various mechanical parts.
Examples of application of grooving machining
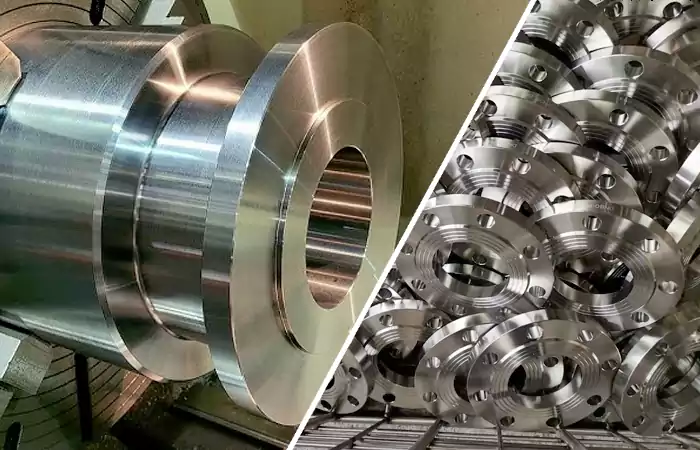
For example, in automobile manufacturing, groove-cutting processing is commonly used for precise processing of key components such as engines. By adopting high-precision cutting technology, we ensure that the groove machining of mounting holes and other parts meets the requirements, thus ensuring the stable assembly and normal operation of each part.
2. Different types of grooving machining
Various grooving techniques
Straight Turning
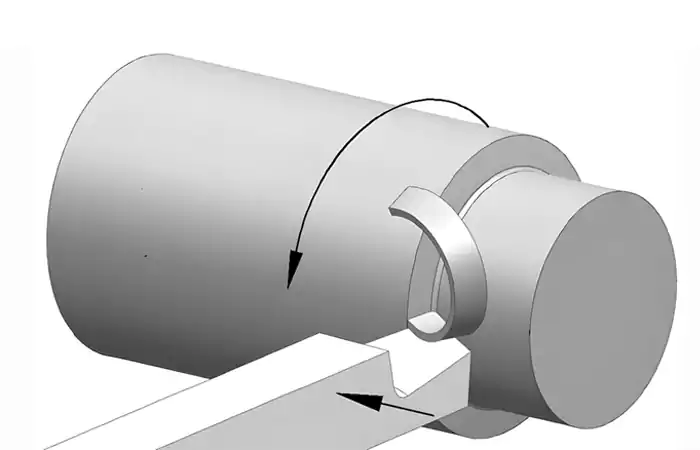
Utilizing CNC lathe for straight line cutting of workpiece is the most basic groove processing method. It is suitable for processing simple straight line grooves and has the advantages of stable processing and convenient operation.
- Ideal for machining straight, symmetrical grooves on cylindrical parts like shafts and rods.
- Ensures precise groove width and depth in high-precision applications.
- Works with various materials, from soft metals to hard alloys.
- Performed on a CNC lathe for accuracy and repeatability.
End face grooving

The groove is formed by cutting on the end face of the workpiece. This method is often used in applications where precision grooves and holes need to be machined on the end of the workpiece to ensure end face machining accuracy and surface quality.
- Ideal for machining round grooves on flat surfaces, crucial for seals and precise face contact.
- Commonly used for O-rings and sealing surfaces requiring exact groove depth.
- Performed on a CNC lathe for high accuracy and repeatability.
- Proper tool selection prevents deflection and ensures efficient chip control.
- Stable cutting tools minimize vibration for a smooth surface finish.
Contour grooving

Grooving is performed according to the curve of the workpiece shape or a preset contour. By controlling the tool trajectory through CNC programming, it can realize the precise machining of complex curves or non-standard grooves to meet the special structural requirements.
- Ideal for machining curved or variable-width grooves in workpieces.
- Widely used in automotive and aerospace industries for specialized parts.
- Creates complex profiles like tapered or stepped grooves.
- Requires advanced CNC programming for precise path control.
- Essential for designs where straight grooves are insufficient.
Bore grooving

Slotting is performed on the inner hole of the workpiece, and the desired slot structure is formed by cutting inside the inner hole. It is suitable for precision machining of bore grooves for shaft parts and seals to ensure the accuracy of bore size and groove shape.
- Ideal for machining recesses in bores like pipes, hydraulic cylinders, and other cylindrical parts.
- Uses long-reach cutting tools that maintain rigidity to prevent deflection.
- Tool selection depends on hole diameter and recess size for proper fit and clearance.
- Common in automotive, aerospace, and hydraulic industries for precise internal grooving.
- Effective chip removal is crucial to prevent tool wear, poor surface finish, and dimensional errors.
- Advanced machining centers with coolant systems enhance cooling and chip evacuation.
Multiple grooving

Multiple parallel or staggered grooves are formed on the same workpiece by continuous or segmented machining. This technology improves machining efficiency and is suitable for complex parts that require multiple functional grooves.
- Ideal for cutting multiple grooves in one cycle, reducing production time.
- Used for creating complex groove structures to meet various process needs.
- Requires precise CNC programming and tool control for accuracy.
- Supports continuous or segmented machining based on workpiece and material.
- Frequent tool wear demands close monitoring and regular maintenance.
Cylindrical grooving
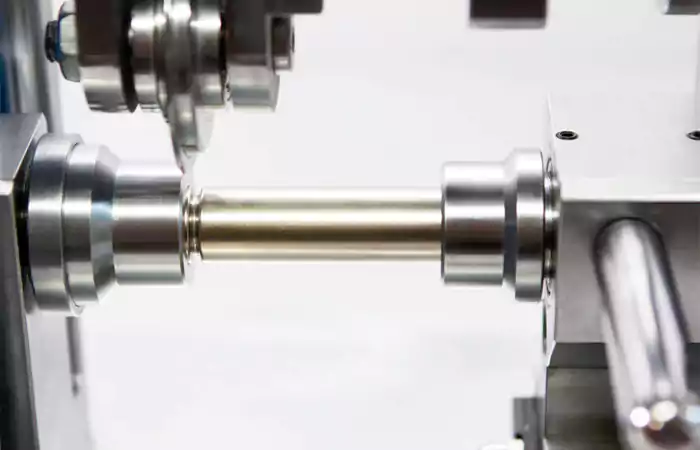
Grooving is mainly performed on the outer surface of the workpiece, and is usually used for machining transmis.
- Ideal for machining symmetrical annular grooves around the workpiece.
- Commonly used for circlips, sealing grooves, and other functional rings.
- Ensures precise and consistent groove width and depth.
- Suitable for various materials, including aluminum, steel, stainless steel, and high-strength alloys.
- Typically performed on CNC lathes for high accuracy and repeatability.
Types of machining technology
In order to realize the different types of grooving, the following technologies are often used in machining:
Milling Grooving
Uses CNC machining to create precise slots with end mills or specialized cutters.
Turning Grooving
Applied in lathe machining to cut grooves on cylindrical parts, often for sealing or assembly purposes.
Grinding Grooving
Utilizes grinding wheels to produce high-precision grooves, mainly for hardened materials.
Wire Cutting and Electric Discharge Machining (EDM)
Ideal for intricate groove shapes in hard metals.
Laser and Plasma Cutting
Best suited for non-contact, high-precision grooving on metal and non-metal materials.
Common groove types
Common groove types can be broadly categorized into the following categories based on cross-sectional shape and application scenarios:
Straight groove
The most common type of groove, with a regular rectangular cross-section, is widely used in transmission, sealing and other structures.
Chamfered groove
Chamfering the corners on the basis of straight grooves not only eliminates sharp edges, but also effectively disperses stress and improves assembly safety.
U-shaped groove
The bottom of the groove is in U-shape, suitable for occasions that require larger load transfer or improved lubrication effect, such as guide grooves, guide rails and so on.
V-groove
With V-shaped cross-section, commonly used in positioning, guiding and clamping devices to ensure the precision of workpiece assembly and movement.
Semi-circular groove
The grooves are in the form of smooth semi-circular arcs, suitable for parts with high requirements for surface transition and aesthetics.
Special shaped grooves
Grooves customized for specific functions and design requirements, such as complex curves or composite cross sections, usually rely on high-precision CNC machining technology.
3. Commonly used tools for Grooving Machining
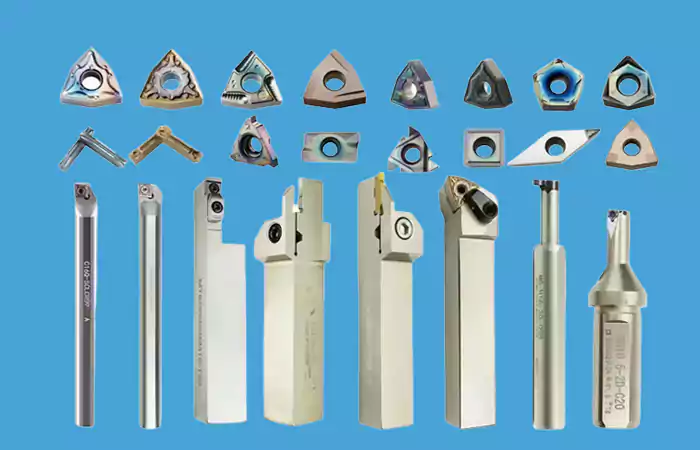
- Milling Tools:
End mills, T-cutters, and dovetail cutters are commonly used in CNC machining for groove creation. - Turning Tools:
Specialized inserts and grooving tools designed for high-speed lathe operations. - Grinding Tools:
Selection of grinding wheels based on material hardness and groove specifications. - Non-Contact Machining Tools:
Laser and EDM tools enable precision cutting without mechanical force.
4. Materials suitable for grooving processing
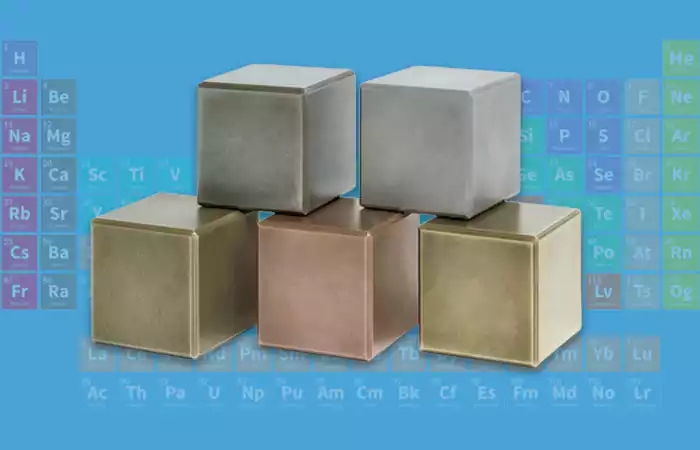
Metals
Common choices include aluminum alloys, stainless steel, and titanium alloys, all of which require precise grooving techniques for optimal results.
Plastics & Composites
These materials demand careful machining to avoid deformation or heat-induced damage.
High-Hardness Materials
Ceramics and hardened steel present significant machining challenges, necessitating the use of specialized cutting tools and techniques.
5. Key factors affecting the quality of grooving machining
Tool Selection & Cutting Parameters
Selecting the appropriate tool, cutting speed, and feed rate is crucial for achieving high precision and surface quality.
Material Properties
The machinability of different materials influences groove accuracy, tool wear, and overall process stability.
CNC Programming & Automation
Well-optimized CNC programs enhance machining accuracy, consistency, and repeatability.
Cooling & Chip Management
Effective cooling and efficient chip removal prevent overheating, improve surface finish, and extend tool life.
6. Major challenges of grooving and strategies
Precision & Surface Finish:
Achieving tight tolerances and superior surface quality requires high-quality tools and optimized machining parameters.
Tool Wear & Maintenance:
Implementing regular monitoring and timely replacement strategies helps extend tool life and maintain machining consistency.
Complex Groove Shapes:
Advanced CNC techniques and multi-axis machining enhance accuracy for intricate groove designs.
Cost & Efficiency:
Partnering with a reliable CNC machining service provider ensures cost-effective production without compromising quality.
7. Summary
Grooving machining plays a critical role in manufacturing by enabling precise slot creation in various materials. Future advancements in smart manufacturing and automation will further enhance efficiency. Choosing an experienced CNC machining service provider is key to achieving high-quality machined parts with optimized costs and lead times.