Need threaded holes in your parts but worried about quality? A poorly tapped hole can lead to stripped threads, failed assemblies, and scrapped components, wasting time and money.
Tapping is the machining process of cutting internal threads into a pre-drilled hole. It uses a tool called a tap to create the helical grooves for screws, bolts, or studs.

In my years of running CNC machining operations at Allied Metal, I’ve seen how even the smallest features can make or break a part. Threaded holes are a perfect example. For engineers like David, who design complex assemblies, the integrity of every connection is vital. Tapping is a small step in CNC machining, but it has a big impact on thread quality. It’s more than just twisting a tool into a hole; it’s a precision process. Choosing the right process and parameters is key to getting accurate, durable threads. Understanding the fundamentals of tapping is essential for designing parts that assemble correctly and perform reliably.
What Is Tapping? (Definition, Process, Types, Purpose, Tools)?
You know tapping creates threads, but what does that entail? What is the process, what are the tools, and what is the ultimate goal of this fundamental machining operation?
Tapping is the process of cutting internal threads in a hole using a cutting tool called a tap. Its purpose is to create a functional, threaded connection for fasteners like screws and bolts.
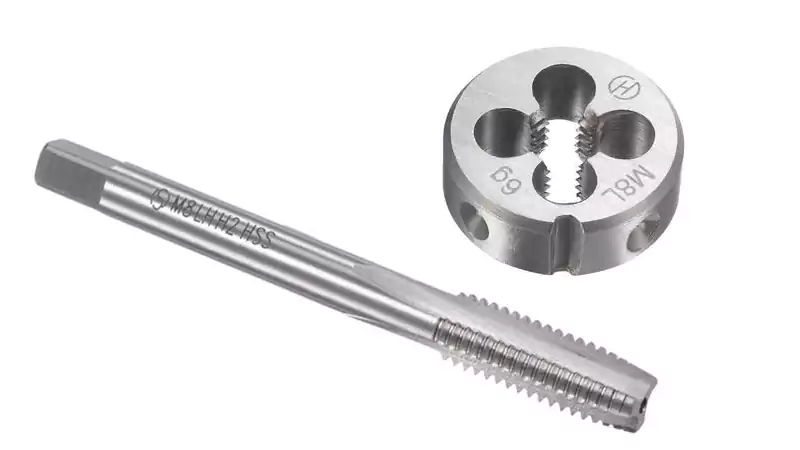
Overview of Tapping
Tapping is a core machining process, and understanding its different facets is key for any engineer or designer. It seems simple, but there's a lot of detail involved in getting it right. Let's break it down.
Definition and Purpose
The formal definition of tapping is the creation of internal (female) threads inside a hole. The primary purpose is to allow a fastener, like a bolt or screw, to be securely threaded into the part, creating a strong and reliable mechanical joint.
The Tapping Process
The process follows a clear sequence:
- Drilling: A hole must first be drilled to a specific size, known as the "tap drill size1." This hole is slightly larger than the minor diameter of the thread but smaller than the major diameter.
- Chamfering: A small chamfer or countersink2 is often added to the top of the hole. This helps the tap start straight and prevents the first thread from pulling up.
- Tapping: The tap is then driven into the hole. As it rotates, its cutting edges shear material from the wall of the hole, forming the helical threads.
- Retraction: The tap is retracted from the hole, leaving behind clean, finished threads.
Types of Tapping
- Hand Tapping: Done manually using a set of taps (taper, plug, and bottoming) and a tap wrench. It's slow and used for one-offs, repairs, or when machine access is limited.
- Machine Tapping: Performed on a drill press or, most commonly, a CNC machine. It's fast, highly accurate, and repeatable.
Tools Used
The primary tool is the tap. Taps come in many forms:
- Straight Flute Taps: For general purpose use.
- Spiral Point Taps (Gun Taps)3: Push chips forward, good for through-holes.
- Spiral Flute Taps4: Pull chips backward out of the hole, ideal for blind holes.
- Form Taps (Roll Taps)5: These don't cut material; they displace or "form" it to create stronger threads, but only work on ductile materials.
What Is Tapping in Engineering?
From a design and function perspective, what does tapping mean? Why is this process so fundamental in mechanical engineering for creating functional products?
In engineering, tapping is the specified process for creating reliable, load-bearing internal threads in a component, enabling mechanical assembly and force transmission through fasteners.
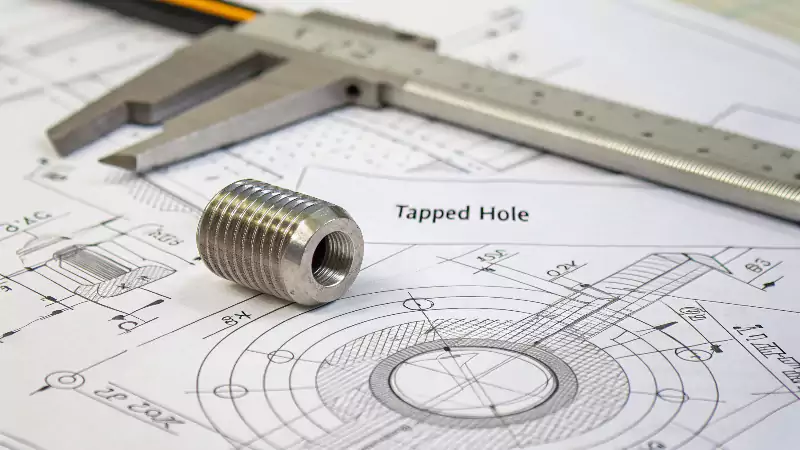
Significance of tapping in engineering
From an engineering standpoint, tapping is far more than just a cutting operation; it is a fundamental process for enabling robust mechanical design and assembly. For a Lead Mechanical Engineer like David, a tapped hole is a critical functional feature that dictates how parts connect, bear loads, and maintain integrity.
The significance of tapping in engineering can be understood in a few key areas:
-
Creating Mechanical Joints: The most basic purpose is to create a location for a fastener. Tapping allows engineers to design assemblies where parts can be securely joined together with standard bolts and screws. This is essential for everything from simple enclosures to complex industrial machinery. It also allows for disassembly and reassembly for maintenance or repair.
-
Load Bearing and Force Transmission: A properly specified and executed tapped hole is designed to withstand specific loads. The geometry of the thread (the flank angles, pitch, and depth) creates a large surface area that distributes the tensile force from a tightened bolt into the body of the component. The "thread engagement length" (how many threads are in contact) is a critical design parameter calculated to ensure the connection is strong enough and won't strip under load.
-
Precision Alignment and Positioning: In many designs, fasteners do more than just clamp. The threads can also serve as a precision adjustment mechanism. Think of a fine-threaded adjustment screw used for calibration. The quality and accuracy of the tapped hole directly relate to the precision of the adjustment.
-
Design for Manufacturability (DFM): An engineer must also consider the manufacturing reality. Specifying a standard thread size (e.g., M6x1.0 or 1/4"-20) is much more cost-effective than a custom size. They must also ensure the design provides adequate wall thickness around the tapped hole and specifies a material that is suitable for tapping to the required strength. This intersection of design requirements and manufacturing capability is where tapping becomes a key engineering consideration.
How Is Tapping Different From Threading?
The terms "tapping" and "threading" are often used together. Are they the same thing, or do they describe different operations in machining?
Tapping specifically refers to cutting internal (female) threads inside a hole. Threading is a broader term that includes tapping, as well as cutting external (male) threads on a rod or shaft.
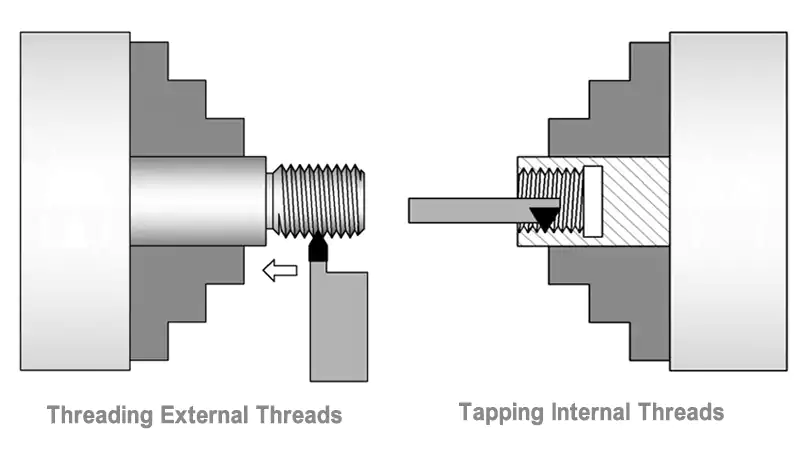
Diving Deeper into the Tapping vs. Threading Distinction
This is a common point of confusion, but the distinction is simple and important for clear communication in a manufacturing environment. For David, using the correct term on a drawing or in a request for quotation is essential.
Threading6 is the general, umbrella term for the process of creating a helical groove, or a "thread," on a workpiece. This can be done either on an internal surface or an external surface.
Tapping is the specific process used to create internal threads7 (female threads), like those inside a nut or a hole in a metal block. The tool used is always a tap.
Let's look at the different types of threading to see where tapping fits in:
Process Category | Specific Operation | What It Does | Tool Used |
---|---|---|---|
Internal Threading | Tapping | Creates threads inside a pre-drilled hole. | Tap Tool |
Thread Milling | Uses a rotating mill cutter to create threads inside a hole. An alternative to tapping. | Thread Mill | |
External Threading | Die Cutting | Creates threads on the outside of a rod or cylinder (manual). | Threading Die |
Lathe Threading (Single-Point Threading) | Uses a single-point tool on a lathe to cut threads on the outside of a rotating part. | Single-Point Threading Tool |
The Easiest Way to Remember:
- If you are creating threads for a bolt to screw into, you are tapping a hole.
- If you are creating threads on the bolt itself, you are performing an external threading operation.
So, all tapping is a form of threading, but not all threading is tapping. When a machinist or engineer says they need to "thread a hole," they almost always mean they need to tap it. When they say they need to "thread a rod," they mean they need to cut external threads. Using the specific term "tapping" removes any ambiguity and clearly communicates that an internal thread is required.
Which Materials Are Suitable for Tapping?
Can you tap threads into any material? What makes a material easy or difficult to tap, and what are some common examples of materials used?
Most metals and many rigid plastics are suitable for tapping. Good machinability is key. Soft metals like aluminum are easy, while hard materials like stainless steel or titanium are more challenging.

Considerations for selecting materials
The suitability of a material for tapping depends heavily on its mechanical properties, such as hardness, ductility, and machinability. A good material allows the tap to shear clean threads without excessive tool wear, binding, or breakage. For David, selecting a material often involves balancing its functional properties with its manufacturability.
Here's a look at some common materials and how they behave during tapping:
-
**Aluminum Alloys (e.g., 6061, 7075):**
- Suitability: Excellent. Aluminum is soft, has good machinability, and produces low cutting forces.
- Considerations: It can be "gummy" and chips can sometimes stick to the tap. Using a lubricant specifically for aluminum and a tap with a polished surface or special coating is highly recommended to prevent this. Form taps work very well on softer aluminum alloys.
-
Carbon and Alloy Steels (e.g., 1018, 4140):
- Suitability: Generally very good. These are some of the most commonly tapped materials.
- Considerations: Hardness can vary greatly. Softer low-carbon steels are easy to tap. Harder alloy steels require slower cutting speeds, more robust taps (like those with a TiN or TiAlN coating), and high-quality cutting fluid.
-
Stainless Steels (e.g., 304, 316):
- Suitability: Challenging but very common.
- Considerations: Stainless steels are known for being "gummy" and for work-hardening. This means as the tap cuts, the material right in front of the cutting edge can become harder, which increases tool wear. Using sharp taps, a rich cutting fluid, and a consistent, non-stop cutting motion is crucial. Spiral flute taps or form taps are often preferred.
-
- Suitability: Very challenging.
- Considerations: Titanium has poor thermal conductivity, meaning heat concentrates at the cutting edge, leading to rapid tool wear. It also has a tendency to gall. Very slow cutting speeds, extremely sharp tools, and a high-volume, high-pressure coolant supply are necessary.
-
Plastics (e.g., Delrin®, Nylon, Acrylic):
- Suitability: Good, but with special considerations.
- Considerations: Plastics can be abrasive to tools and have a tendency to melt if heat builds up. Very sharp taps are needed to shear the material cleanly rather than melt or push it. Often, tapping is done without liquid coolant to avoid thermal shock, relying on air blast instead. Special taps designed for plastics are available.
The key is to always match the tap type, geometry, and cutting parameters to the specific material being worked on.
Tapping vs Milling vs Drilling?
These three operations all happen on a CNC machine, often on the same hole. What is the distinct role of each process: tapping, milling, and drilling?
Drilling creates the initial hole. Tapping cuts internal threads into that hole. Milling is a broader process that can create complex shapes, slots, surfaces, or even threads via thread milling.
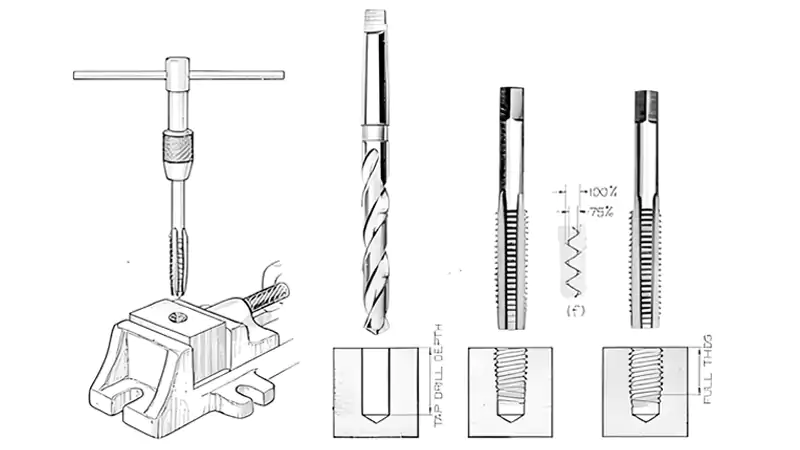
Diving Deeper into Three Distinct Hole Operations
While drilling, milling, and tapping are all common CNC machining processes, they serve fundamentally different purposes, though they are often used in sequence on the same part feature. Understanding the role of each is essential for any engineer like David.
Drilling
- Purpose: The primary and sole purpose of drilling is to create a round hole in a workpiece.
- Process: A rotating cutting tool with two cutting edges (a drill bit) is plunged along its axis into the material to create a hole.
- Role in Tapping: Drilling is the mandatory first step for tapping. It creates the specific "tap drill size" hole that the tap will then thread. The quality of the drilled hole (its straightness and diameter) directly impacts the quality of the final tapped thread.
Tapping
- Purpose: As we've discussed, the purpose of tapping is to create internal threads within a pre-existing hole.
- Process: A tap tool, which has cutting edges in the shape of the desired thread, is driven into the drilled hole to cut the threads.
- Relationship: Tapping is a secondary operation that modifies a drilled hole. It does not create the hole itself.
Milling
- Purpose: Milling is a highly versatile process used to create a wide variety of shapes and features by removing material with a rotating multi-point cutting tool (an end mill).
- Role in Hole Making/Threading:
- Milling can create large holes through a process called "helical interpolation," where an end mill moves in a circular path.
- Milling can also create threads through a process called Thread Milling. In thread milling, a rotating "thread mill" cutter moves in a helical path inside a hole to cut the threads. This is an alternative to tapping, offering more control over thread size and being suitable for large or unusual threads.
Here is a simple summary table:
Operation | Primary Function | Tool Used | Creates Hole? | Creates Threads? |
---|---|---|---|---|
Drilling | Create a simple round hole. | Drill Bit | Yes | No |
Tapping | Add internal threads to an existing hole. | Tap Tool | No | Yes |
Milling | Create complex shapes, surfaces, slots, etc. | End Mill, Face Mill, etc. | Can (large holes) | Can (thread milling) |
For a standard threaded hole, the sequence is always: 1. Drill, 2. Tap.
What are the main parameters of the tapping?
To ensure a successful tapping operation, what are the key parameters a machinist must control? What settings are critical for creating strong, accurate threads?
The main parameters for tapping are selecting the correct tap drill size, setting the proper cutting speed and feed rate, and using adequate lubrication. These control thread quality and tool life.
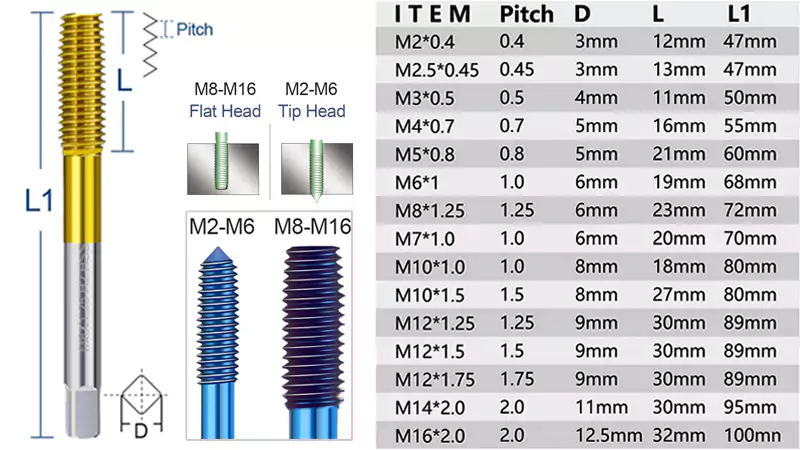
Understanding Key Tapping Parameters
Achieving a perfect tapped hole requires careful control over several key machining parameters. For David, specifying a thread on a drawing implicitly requires the machinist to manage these parameters correctly. A failure in any one of these can lead to a broken tap, a common and frustrating problem in any machine shop.
1. Tap Drill Size
- What it is: This is the diameter of the hole that is drilled before tapping. This is arguably the most critical parameter.
- Why it's important:
- If the hole is too small, the tap has to remove too much material. This dramatically increases the torque required, which will almost certainly break the tap.
- If the hole is too large, there won't be enough material for the tap to cut a full-depth thread, resulting in a weak and shallow thread that will easily strip.
- How it's chosen: Standardized charts provide the exact tap drill size required for every thread size (e.g., a 1/4"-20 thread requires a #7 drill). These charts calculate the size needed to achieve a standard thread engagement, typically around 75%.
2. Cutting Speed
- What it is: The rotational speed of the tap, measured in RPM (Revolutions Per Minute) or Surface Feet per Minute (SFM).
- Why it's important: The correct speed depends almost entirely on the material being tapped.
- Too fast: Generates excessive heat, leading to rapid tool wear and potential failure, especially in tough materials like stainless steel.
- Too slow: Can be inefficient and, in some materials, can increase the risk of work hardening.
- How it's chosen: Based on the tap manufacturer's recommendations for the specific material. Harder materials require slower speeds.
3. Feed Rate (for Rigid Tapping)
- What it is: The rate at which the tap is fed down into the hole.
- Why it's important: In modern CNC machines using "rigid tapping," the feed rate must be perfectly synchronized with the spindle speed. The feed per revolution must be exactly equal to the pitch of the thread. For example, for an M6x1.0 thread (with a 1.0mm pitch), the tap must advance exactly 1.0mm for every full revolution.
- How it's chosen: It's a direct calculation: Feed Rate (mm/min) = RPM x Pitch (mm). Any error in this synchronization will break the tap or strip the threads.
4. Lubrication / Coolant
- What it is: The use of a cutting fluid during the tapping process.
- Why it's important: Lubrication reduces friction, which lowers the required torque and helps prevent chips from welding to the tap. It also helps cool the tool and workpiece, extending tool life. It also aids in flushing chips out of the hole. The type of fluid used (e.g., oil, synthetic coolant) depends on the material.
Getting all these parameters right is what makes tapping a consistent and reliable process in a professional CNC environment.
Conclusion
Tapping is a precision machining process vital for creating internal threads. Correct tool selection, material consideration, and process parameters are crucial for strong, reliable mechanical assemblies.
-
Understanding tap drill size is crucial for successful tapping, ensuring threads are formed correctly and efficiently. ↩
-
Learning about countersinks can improve your drilling techniques and ensure better thread formation in your projects. ↩
-
Explore this link to understand the unique benefits and applications of Spiral Point Taps in various machining processes. ↩
-
Discover the functionality of Spiral Flute Taps and their ideal applications for blind holes in machining. ↩
-
Learn about Form Taps and their advantages in creating stronger threads without cutting material, perfect for ductile materials. ↩
-
Understanding Threading is crucial for effective communication in manufacturing, ensuring precision in designs and requests. ↩
-
Learning about internal threads will deepen your understanding of their applications and importance in various mechanical designs. ↩