Ever struggled with material selection for custom components? PVC plastic solves machining headaches with unbeatable versatility. I've seen it transform prototyping and production across industries since my CNC shop days.
PVC (Polyvinyl Chloride) is a versatile and cost-effective thermoplastic. It is widely used for custom CNC machined parts due to its excellent chemical resistance, durability, and ease of machining.
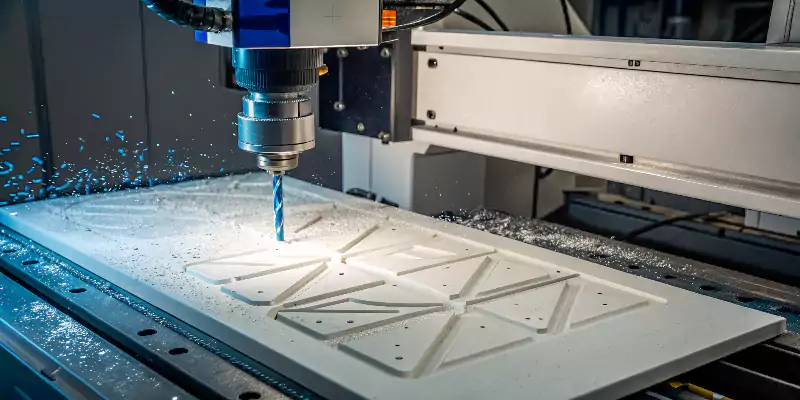
After working with hundreds of different plastic materials over my years at Allied Metal, I've seen firsthand how the right material choice can make or break a project. PVC consistently delivers results that exceed expectations. Let me share what I've learned about this remarkable plastic and why it might be perfect for your next project.
What Is PVC Plastic?
You've probably heard of PVC pipes. But what is this material from a technical standpoint, and what makes it so useful for more than just plumbing?
PVC, or Polyvinyl Chloride, is a high-strength thermoplastic polymer. It is one of the most widely produced synthetic plastics, known for its durability, chemical resistance, and versatility in both rigid and flexible forms.
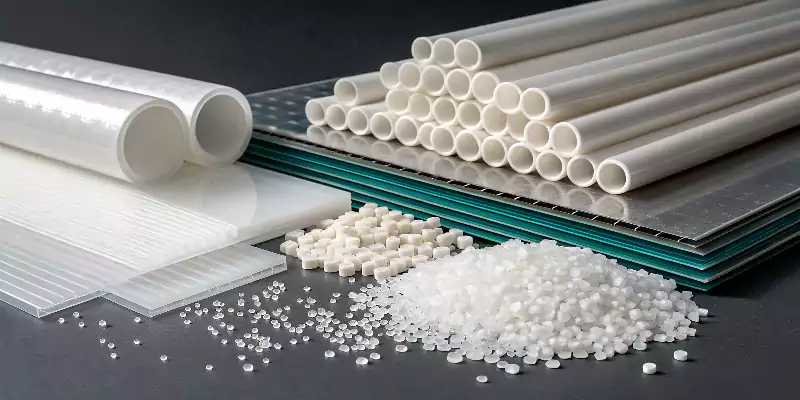
Diving Deeper into Polyvinyl Chloride
PVC (Polyvinyl Chloride) is one of the most commonly used thermoplastics, valued for its low cost, chemical resistance, and excellent machinability. Because it can be reheated and reshaped without losing its integrity, PVC is ideal for a wide range of manufacturing methods—including extrusion, injection molding, and, most importantly for our purposes, CNC machining.
There are two main types of PVC:
-
Rigid PVC (uPVC or RPVC)1:
Strong, stiff, and dimensionally stable, this is the preferred type for CNC machining. It's commonly used for pipes, electrical housings, window frames, and custom precision parts. -
Flexible PVC (fPVC)2:
Made pliable with plasticizers, it’s used in products like cable insulation, flooring, and medical tubing. While it can be machined, it's less stable and more difficult to handle than rigid PVC.
Why PVC Machines Well
PVC’s molecular structure—built from carbon, hydrogen, and chlorine—gives it flame resistance and mechanical strength. In practice, rigid PVC cuts cleanly, holds tight tolerances, and produces minimal waste.
For most custom-machined components, engineers choose rigid PVC due to its durability, precision, and cost-effectiveness. It’s a reliable material for both prototypes and production runs across various industries.
What Are the Key Properties of PVC Plastic?
What makes PVC plastic suitable for industrial parts? What are its key mechanical, thermal, and chemical properties that an engineer needs to know when designing components?
PVC plastic is defined by its high hardness and durability, excellent electrical insulation, and broad chemical resistance. However, it has a relatively low melting point compared to other engineering plastics.
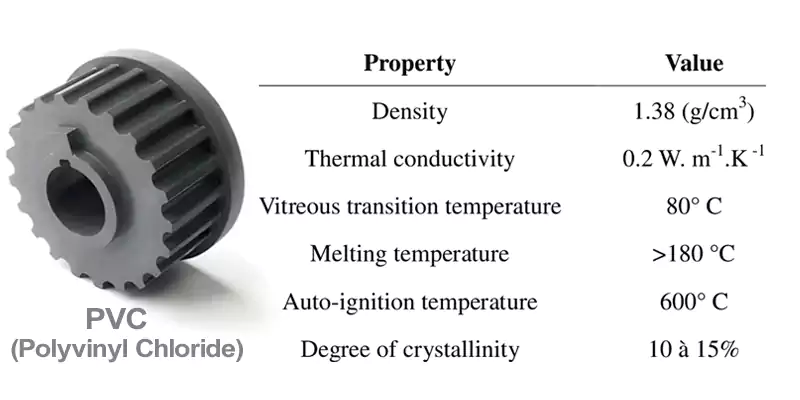
Diving Deeper into PVC's Characteristics
For an engineer like David to confidently specify PVC plastic for a project, he needs to understand its key properties. These characteristics determine its suitability for different applications and environments.
Here's a summary of the most important properties of rigid PVC (Type I):
Property | Description | Implication for Design |
---|---|---|
Mechanical Strength | Possesses good tensile strength, stiffness, and hardness. It is very durable and resistant to abrasion. | Excellent for structural components, housings, and parts that need to be durable. |
Chemical Resistance | Highly resistant to a wide range of acids, alkalis, salts, and oils. | Ideal for parts used in chemical processing, storage tanks, valves, and fittings. |
Electrical Insulation | An excellent electrical insulator, meaning it does not conduct electricity. | Widely used for electrical enclosures, insulators, cable holders, and conduit. |
Dimensional Stability | Absorbs very little moisture and has a low coefficient of thermal expansion, so it holds its shape and size well. | Great for precision machined parts that require tight tolerances to be maintained. |
Low Flammability | It is inherently flame-retardant and self-extinguishing. It will not continue to burn once the flame source is removed. | Adds a layer of safety for applications in construction and electrical installations. |
Low Temperature Limit | Has a relatively low continuous service temperature, typically around 140°F (60°C). It can become brittle at low temperatures. | Not suitable for high-temperature applications. CPVC is an alternative for higher heat. |
These properties, especially the combination of chemical resistance, dimensional stability, and electrical insulation, make PVC plastic a highly versatile and reliable choice for a huge number of machined parts in industrial settings.
What Are the Advantages and Disadvantages of PVC Plastic?
Seeing engineers overlook PVC’s cost benefits surprises me. A solar equipment manufacturer reduced part costs by 35% after my material recommendation.
PVC advantages include low cost ($1.5-3/kg), easy machining, and electrical safety. Disadvantages involve limited temperature tolerance and environmental concerns during disposal. It outperforms metals in corrosion resistance but can’t match PEEK’s heat resistance.
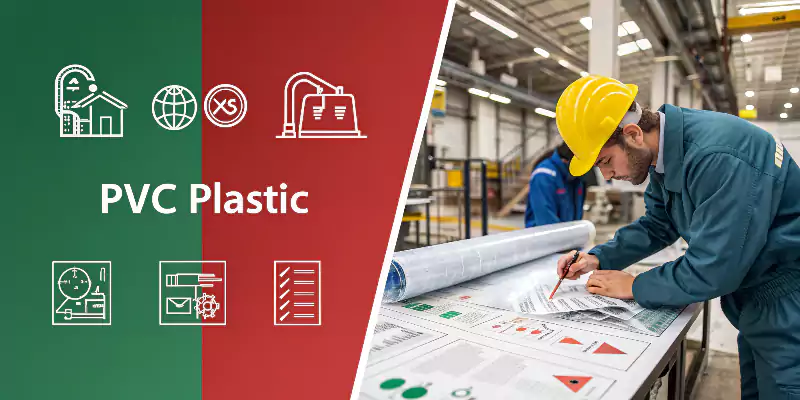
When to Choose PVC
- Best for: Chemical tanks, electrical insulators, food processing fixtures
- Avoid when: Continuous >80°C exposure occurs or extreme impact resistance is critical
Sustainability Considerations
Modern PVC recycling programs now reclaim 30%+ of production waste. I advise clients to specify phthalate-free formulations for medical applications. Though production involves chlorine, PVC’s 50-year service life often offsets its footprint. For enclosures, it beats aluminum in energy-efficient manufacturing.
What Are the Common Types of Machined PVC Plastic?
Is all rigid PVC the same? What different grades or types of PVC plastic are available as stock material for CNC machining applications?
The most common type for machining is Type I Rigid PVC. Other available types include Type II for higher impact strength and CPVC for higher temperature resistance.
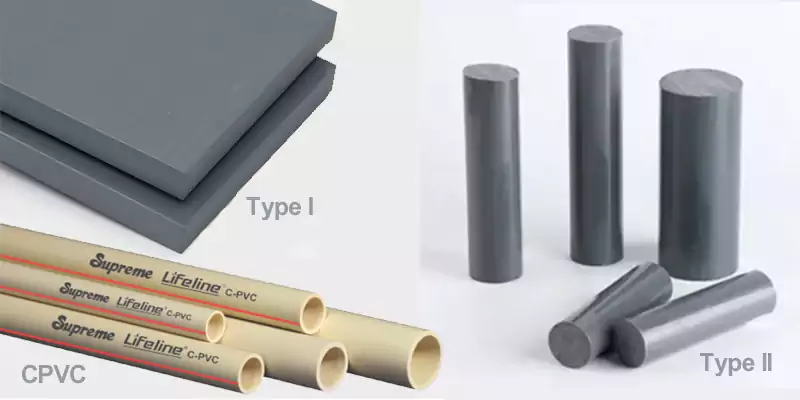
Diving Deeper into PVC Grades for Machining
When an engineer like David specifies a PVC part, he may also need to specify a particular grade or type based on the application's demands. While they are all based on Polyvinyl Chloride, different formulations offer enhanced properties.
Here are the most common types of PVC available in stock shapes (like sheets, rods, and tubes) for CNC machining:
PVC Type I (Rigid PVC)
- Description: This is the most common, versatile, and cost-effective grade of PVC. It is unplasticized and unmodified.
- Key Properties: Excellent chemical and corrosion resistance, high strength and rigidity, strong electrical and thermal insulation, and good dimensional stability.
- Common Uses: This is the default choice for a huge range of machined parts, including chemical tanks, electrical insulators, valves, fittings, and machine housings. When someone just says "PVC" in a machining context, they are usually referring to Type I.
PVC Type II (High Impact PVC)
- Description: This is a modified version of PVC that has been formulated to provide much higher impact strength and durability than Type I.
- Key Properties: It retains good chemical and corrosion resistance but sacrifices some tensile strength and temperature resistance to gain its high impact toughness.
- Common Uses: Used for applications where parts may be subject to impact, shock, or vibration. Examples include machine guards, durable housings, and components that need to resist cracking.
CPVC (Chlorinated Polyvinyl Chloride)
- Description: As the name suggests, this grade has extra chlorine atoms in its structure.
- Key Properties: The key advantage of CPVC is its significantly higher temperature resistance. It can handle continuous service temperatures up to around 200°F (93°C), much higher than standard PVC. It also maintains excellent chemical and corrosion resistance.
- Common Uses: CPVC is the material of choice for applications involving hot corrosive liquids. It's widely used for hot water plumbing, industrial liquid handling systems, and components in chemical processing plants that operate at elevated temperatures.
Choosing the right type is a critical design step. For general-purpose parts, Type I is perfect. If impact is a concern, Type II is better. And if heat is involved, CPVC is the necessary upgrade.
How Do You CNC Machine PVC?
What are the best practices for CNC machining PVC plastic? What tools, speeds, and techniques should be used to get a clean, accurate cut?
To CNC machine PVC, use very sharp cutting tools (HSS or carbide), high spindle speeds, and fast feed rates. Proper chip and dust extraction is critical for a good finish and operator safety.
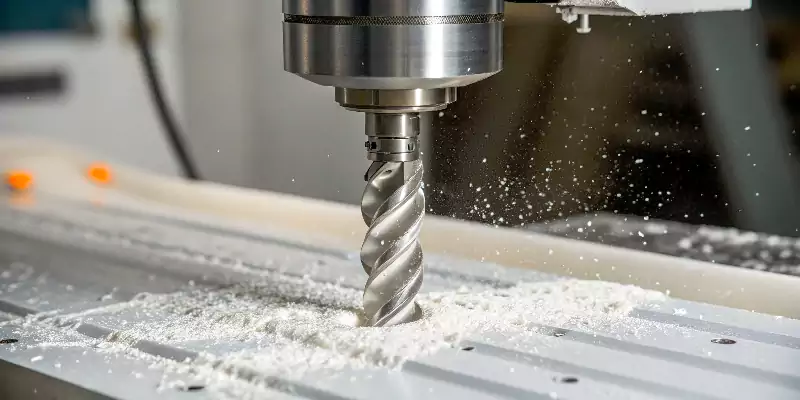
Explore practical PVC processing techniques
Based on my years of machining experience at Allied Metal, PVC is relatively easy to machine, but it still takes the right technique to get a clean, accurate finish. Unlike metal, PVC reacts differently during the cutting process, so understanding these details helps engineers design efficient, cost-effective parts.
Here are the key considerations for CNC machining PVC:
Cutting Tools
- Sharpness is Key: The single most important factor is to use extremely sharp cutting tools. A dull tool will not shear the plastic cleanly; it will tend to melt, push, or tear it, resulting in a poor surface finish and burrs.
- Tool Material: Both High-Speed Steel (HSS) and uncoated carbide tools work very well. Carbide tools will stay sharp longer, making them better for production runs. Coated tools are generally not necessary.
- Tool Geometry: Tools with a high positive rake angle and high relief angle work best. These geometries provide a sharp edge that cleanly "slices" the plastic and helps evacuate chips. For milling, end mills with fewer flutes (e.g., 1 or 2 flutes) are often preferred as they provide more room for chip evacuation.
Speeds and Feeds
- High Spindle Speeds: PVC can be cut at very high spindle speeds (RPM). Higher speeds help ensure the tool is shearing the material rather than rubbing against it.
- Fast Feed Rates: It is crucial to maintain a fast feed rate. If the tool spins in one place for too long or moves too slowly, it will generate friction and heat, which can melt the PVC and cause it to gum up on the tool. You want to get the chip out of the way as quickly as possible. The goal is to produce distinct chips, not a melted mess.
Chip and Dust Management
- Chip Evacuation: As mentioned, clearing chips is critical to prevent melting. For milling and routing, a good dust collection system or a directed air blast is essential. For drilling, it's important to "peck" drill (periodically retract the drill) to clear chips from the hole.
- Health and Safety: PVC dust can be an irritant, so proper ventilation and dust extraction are important for the machine operator's safety.
By following these practices, we can achieve an excellent, clean surface finish on machined PVC parts with high accuracy and efficiency.
What Kind of Surface Finishes Can Be Achieved on PVC?
A client rejected matte-finish control panels last year. Now I specify finishes based on both function and aesthetics.
PVC accepts all standard finishes: as-machined (Ra 3.2μm), bead blasted (matte texture), polished (mirror), and painted. Chemical smoothing removes tool marks without affecting dimensions, ideal for medical components.
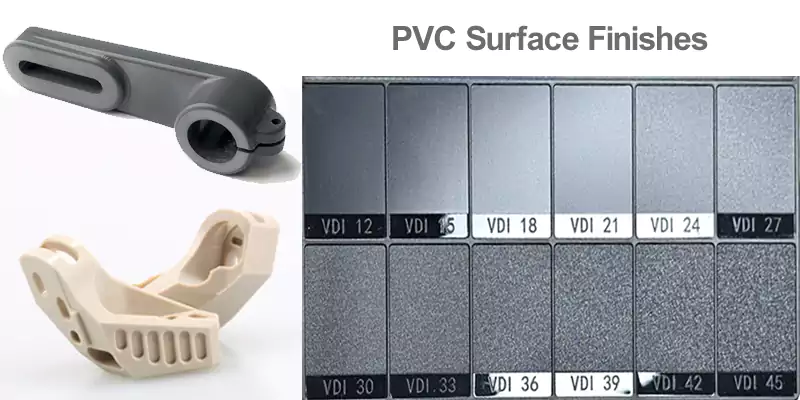
Functional vs Cosmetic Finishes
- Functional: Grit-blasting improves adhesive bonding for composite assemblies
- Cosmetic: High-gloss polishing (up to Ra 0.4μm) for consumer products
Specialty Treatments
Electroplating creates conductive surfaces for EMI shielding - we plate sensor mounts for automotive clients. Laser etching3 adds permanent identifiers without compromising chemical resistance. For outdoor use, UV-resistant clear coats prevent yellowing. One aerospace client saved weight using textured PVC instead of painted aluminum.
What Industries Use PVC Machined Parts?
Understanding where PVC parts are used helps appreciate the material's versatility and importance.
PVC machined parts serve critical roles in chemical processing, medical devices, electrical equipment, automotive components, and architectural applications. The material's chemical resistance, electrical insulation properties, and cost-effectiveness make it indispensable across these industries.
Over the years, I've machined PVC parts for an incredibly diverse range of applications. Each industry leverages different aspects of PVC's property profile. Understanding these applications helps identify opportunities for your own projects.
Chemical Processing Industry
Chemical processing represents one of PVC's largest application areas. I've manufactured valve bodies, pump components, tank fittings, and process equipment housings for chemical plants. The material's resistance to acids, alkalis, and many organic solvents makes it ideal for these demanding environments.
Corrosion resistance provides significant cost advantages over metal alternatives. A chemical processing client reported that PVC valve bodies lasted three times longer than stainless steel equivalents in their chlorine handling system. This durability translates to reduced maintenance costs and improved process reliability.
Medical and Laboratory Equipment
Medical device applications leverage PVC's biocompatibility4 and sterilization capability. I've machined components for analytical instruments, laboratory equipment, and medical device housings. The material can withstand common sterilization methods including gamma radiation and ethylene oxide treatment.
Clean machining characteristics make PVC suitable for medical applications. The material doesn't outgas significantly and can be cleaned to very high standards. Parts maintain their properties after repeated sterilization cycles, making them suitable for reusable medical equipment.
Electrical and Electronics Applications
PVC's electrical insulation properties and flame resistance make it valuable for electrical applications. I've produced electrical enclosures, connector housings, and cable management components. The material's UL rating for flame resistance satisfies safety requirements in many electrical applications.
Self-extinguishing properties provide critical safety benefits. PVC components won't contribute to fire spread in electrical systems. This characteristic has made it the preferred choice for electrical enclosures in commercial buildings and industrial equipment.
Emerging Uses
3D-printed PVC molds now accelerate injection molding prototyping. We’re developing glass-filled PVC for load-bearing robotic joints. Recent projects include drone battery casings (lightweight insulation) and renewable energy converter housings.
The widespread use of custom machined PVC parts across these sectors highlights its proven value as a reliable and cost-effective engineering material.
Get expert PVC CNC machining services from Allied Metal!
Why struggle with material selection and machining challenges when expert help is available?
Allied Metal offers comprehensive PVC machining services with over 20 years of experience, state-of-the-art CNC equipment, and proven expertise in delivering precision components. Our team understands PVC's unique characteristics and can optimize your design for manufacturability and cost-effectiveness.
Choosing the right manufacturing partner makes all the difference in project success. At Allied Metal, we've built our reputation on delivering quality PVC components that meet or exceed specifications. Our experience spans multiple industries and applications, giving us unique insights into PVC machining best practices.
Our Capabilities
- Materials: All PVC grades including colored and FDA-compliant
- Equipment: 25 CNC mills with high-speed spindles
- Quality: ISO 9001-certified, full CMM inspection
Client Success Example
A robotics startup needed 200 sensor mounts in 10 days. We machined Type 2 PVC parts in 7 days with chemical-resistant plating, saving 40% versus PEEK. Their production runs now use our just-in-time delivery.
Conclusion
PVC plastic strikes an ideal balance between cost, durability, and chemical resistance, making it a smart choice for a wide range of custom CNC machined parts. With its reliable performance and ease of machining, it's a material engineers can count on for both prototypes and production runs.
-
Discover the advantages of Rigid PVC in various applications, especially in CNC machining, to enhance your knowledge. ↩
-
Learn about the diverse uses of Flexible PVC and its significance in products like cable insulation and medical tubing. ↩
-
Discover how laser etching provides permanent identifiers while maintaining chemical resistance, a valuable technique in various industries. ↩
-
Exploring biocompatibility will enhance your knowledge of material selection in medical devices, ensuring safety and effectiveness. ↩