Sandblasting is a common method for aggressive surface cleaning, but using the wrong finish can damage precision parts. If the process is too harsh, it may harm the surface; if too mild, it may not clean or prepare it properly.
Sandblasting is an aggressive abrasive method for heavy cleaning or creating a rough texture. Glass bead blasting is a gentler process that cleans and produces a smooth, satin finish without damaging the surface.

Here at Allied Metal, once we've completed the CNC machining on a component, the job often isn't finished. The part's surface finish is critical for its final look and function. This is where processes like sandblasting and glass bead blasting come in. For an engineer like David, specifying the correct surface treatment is a crucial part of the design process. Both sandblasting and glass bead blasting are abrasive blasting techniques used for surface treatment. They use compressed air to propel media at a part, but that's where the similarities end. It's important to understand that glass bead blasting provides a smoother, more polished finish and is better suited for precision parts or surfaces that require a finer touch. Choosing the right one depends entirely on the intended purpose of the part.
What Exactly Is Sandblasting and How Does It Work?
You've heard of sandblasting for tough cleaning jobs. But what is this process, and how does it achieve such an aggressive cleaning and texturing effect?
Sandblasting is a surface treatment process that forcibly propels a stream of abrasive media, traditionally sand, against a surface under high pressure to clean, etch, or prep it.
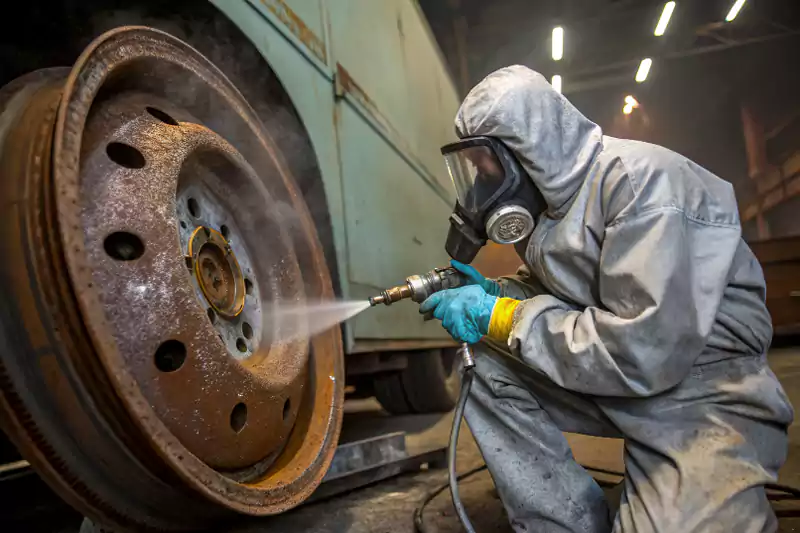
In-depth understanding of the sandblasting process
Sandblasting is a type of abrasive blasting known for its aggressive and effective cleaning power. The core principle involves using a high-pressure stream of compressed air to propel granular abrasive media at a very high velocity onto a surface. This high-speed impact forcefully removes contaminants and a microscopic layer of the base material itself.
The Abrasive Media
While the name implies sand, modern sandblasting services use a variety of media depending on the application.
- Silica Sand1: The original medium, though its use is now highly regulated in many areas due to health concerns (silicosis).
- Aluminum Oxide2: A very hard, sharp, and reusable abrasive. It cuts quickly and is excellent for creating a deep anchor pattern for coatings.
- Steel Grit / Steel Shot: Very aggressive and durable media used for heavy-duty sandblasting metal applications, like preparing structural steel.
- Garnet: A good all-around abrasive that is fast-cutting and produces less dust than sand.
The Action on the Surface
The key effect of sandblasting is etching3. The sharp, angular particles act like tiny chisels, chipping away at the surface. This creates a rough, textured profile often called an "anchor pattern." This process is extremely effective for:
- Heavy-Duty Cleaning: Removing thick rust, scale, and heavy corrosion.
- Coating and Paint Removal: Stripping old paint, powder coating, or other coatings down to the bare substrate.
- Surface Preparation: Creating a rough sandblasted surface profile that gives paint, epoxy, and other coatings something to "bite" into, ensuring excellent adhesion.
Because sandblasting removes base material and alters the surface texture, it's generally not used on precision-machined parts where maintaining tight tolerances is critical. It is a preparatory process, not a final cosmetic finish.
What Is Glass Bead Blasting and What Makes It Different?
If sandblasting is aggressive, what is the alternative for more delicate parts? What is glass bead blasting, and how does it clean without damaging the surface?
Glass bead blasting is a gentler abrasive blasting technique. It uses fine, spherical glass beads to clean, deburr, and impart a smooth, satin finish without significantly removing base material.
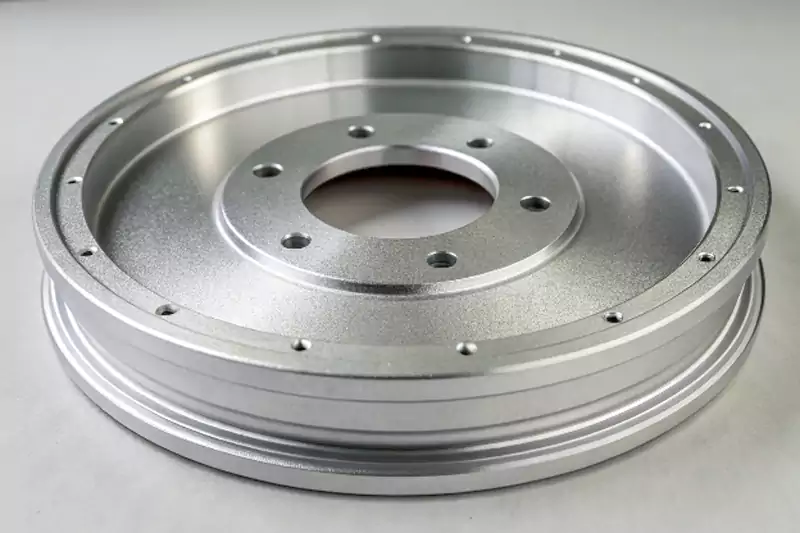
Understanding Glass Bead Blasting
Glass bead blasting is another form of abrasive blasting, but its mechanism and results are fundamentally different from sandblasting. As the name suggests, this process uses tiny spherical beads made of high-quality glass as the blasting medium. These beads are propelled by compressed air, just like in other blasting processes.
The Abrasive Media
The key is the media itself: spherical glass beads. Unlike the sharp, angular particles used in sandblasting, glass beads are round and smooth. They are available in various sizes, from very coarse to extremely fine, allowing for precise control over the resulting finish.
The Action on the Surface
The crucial difference is that glass bead blasting has a peening action rather than an etching action. When the round beads strike the surface, they don't dig in and remove material in the same way. Instead, they gently pound or "peen" the surface. This process:
- Cleans Effectively: It removes surface contaminants like light rust, scale, carbon deposits, and discoloration without damaging the underlying material.
- Creates a Uniform Finish: It produces a very clean, bright, satin, or matte bead blasting finish. The finish is uniform and non-directional, which is often aesthetically desirable.
- Deburrs Parts: It's effective at removing small burrs from machined parts without altering critical dimensions.
- Preserves Dimensions: Because it's a non-etching process, glass bead blasting does not significantly change the dimensions of a part. This makes it ideal for precision-machined components with tight tolerances. This is a key point from my experience—it's the go-to for a fine touch.
Glass bead blasting aluminum, for example, is a very common way to clean and create a beautiful, uniform satin finish on machined aluminum parts without profiling the soft metal. It is considered a finishing process, not just a preparatory one.
Sandblasting vs. Glass Bead Blasting: What Are the Core Differences?
Both processes use propelled media to treat a surface. But what are the key distinctions between sandblasting vs bead blasting that engineers must understand?
The core differences lie in the media, surface impact, and purpose. Sandblasting uses sharp media to aggressively etch a surface for prep. Glass bead blasting uses round beads to gently peen and polish a surface for a final finish.
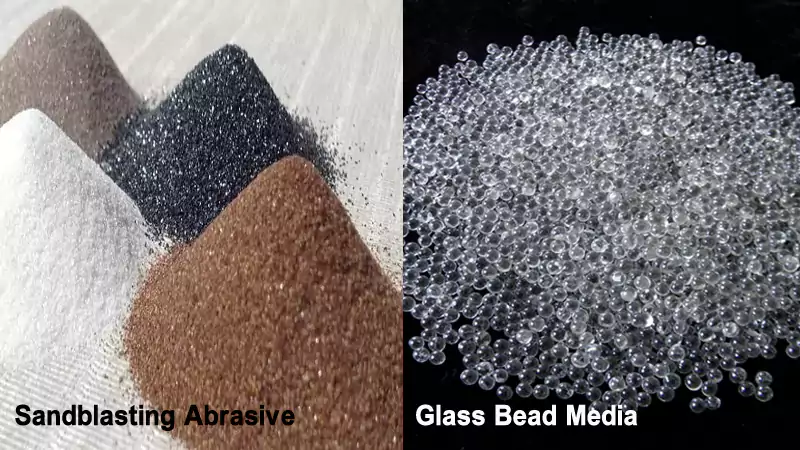
Diving Deeper into the Head-to-Head Comparison
For an engineer, choosing between sandblasting services and glass bead blasting services requires a clear understanding of their fundamental differences. The choice directly impacts the part's final dimensions, appearance, and suitability for subsequent processes like coating. My insight about glass bead blasting providing a smoother finish is rooted in these core distinctions.
Here is a direct comparison:
Feature | Sandblasting | Glass Bead Blasting |
---|---|---|
Abrasive Media | Sharp, angular particles (sand, aluminum oxide, steel grit). | Round, spherical glass beads. |
Action on Surface | Etching / Cutting: Acts like millions of tiny chisels, cutting into the surface. | Peening / Polishing: Acts like millions of tiny ball-peen hammers, impacting the surface. |
Material Removal | Yes. Removes surface material (rust, scale) and some base material. | Minimal to None. Does not significantly remove base material or alter dimensions. |
Resulting Surface Finish | Rough, matte, textured. Creates an "anchor profile." | Smooth, bright, satin, or polished. A bead blasting finish is uniform. |
Primary Purpose | Aggressive cleaning, stripping coatings, preparing a surface for painting/bonding. | Final finishing, light cleaning, deburring, cosmetic enhancement, stress relief. |
Typical Applications | Structural steel, rusted parts, old equipment restoration, paint prep. | Precision machined parts, molds, automotive components, glass bead blasting aluminum. |
Effect on Tolerances | Will alter part dimensions and tolerances. | Preserves critical dimensions and tight tolerances. |
Key Takeaway:
The sandblasting vs. glass bead blasting debate comes down to one question: Are you preparing a surface for something else, or are you creating the final surface?
- To prepare a surface for paint or another coating, you need the rough profile created by sandblasting.
- To create a beautiful, clean, final cosmetic finish on a precision part, you need the gentle peening action of glass bead blasting.
Which Process Creates a Better Surface Finish: Sandblasting or Glass Bead Blasting?
When the look and feel of a part matter, which method delivers a superior finish? Is a rough sandblasted surface ever better than a smooth bead blasting finish?
"Better" depends on the goal. For a final, smooth, aesthetic finish, glass bead blasting is superior. For preparing a surface for paint or coatings, a rough sandblasted surface is better.
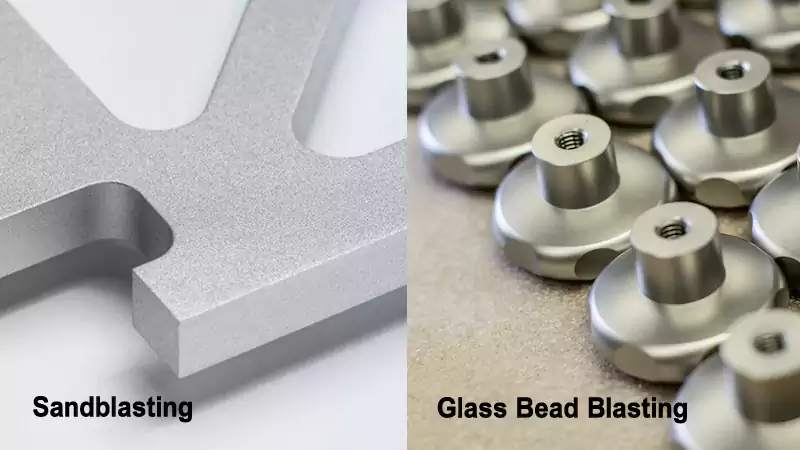
An In-Depth Look at Surface Finish Quality
The concept of a "better" surface finish is entirely dependent on the part's application. What is ideal for one purpose can be completely wrong for another. As an experienced machinist, I know that the specified finish is a critical engineering requirement.
The Sandblasted Surface: Engineered Roughness
A finish from sandblasting is uniformly rough and matte. The surface is covered in microscopic peaks and valleys, which is known as an "anchor pattern" or "surface profile."
- When is this "better"? This rough texture is ideal when the part is going to be coated. The increased surface area and texture give paint, powder coating, epoxy, or thermal spray coatings a much stronger mechanical bond. The coating can physically lock into the profile, making it far more durable and resistant to chipping or peeling.
- Appearance: A sandblasted surface has a non-reflective, flat, and often dark gray appearance on metal. It is not considered a cosmetic finish. The main goal of a sandblasting finish is functional adhesion.
The Bead Blasting Finish: Cosmetic Smoothness
A finish from glass bead blasting is smooth to the touch, non-porous, and can range from a soft satin luster to a brighter, more polished look depending on the bead size and air pressure used.
- When is this "better"? This is the superior choice when the blasted surface is the final, visible finish of the part. It's used for cosmetic purposes, cleaning without damage, and creating a pleasing, uniform texture. As my insight states, it's perfect for a "smoother, more polished finish."
- Functionality: Beyond looks, the peening action of glass bead blasting can also impart compressive stress on the surface, which can improve fatigue resistance in some parts. Because it doesn't remove material, it's the only safe choice for finishing parts with critical tolerances, such as molds, turbine blades, or precision machined aluminum components.
So, for David's parts, if a component needs to be painted, sandblasting is the better prep. If a part, like a visible aluminum housing, needs a clean, uniform, and attractive final finish, glass bead blasting is unquestionably the better choice.
How Do You Choose Between Sandblasting and Glass Bead Blasting Services?
Your part needs a blasted finish. How do you make the right call between sandblasting and glass bead blasting? What questions should you ask to ensure the best outcome?
Choose based on your goal. Need aggressive cleaning or paint prep? Use sandblasting. Need a fine cosmetic finish or to preserve tolerances on a precision part? Use glass bead blasting.
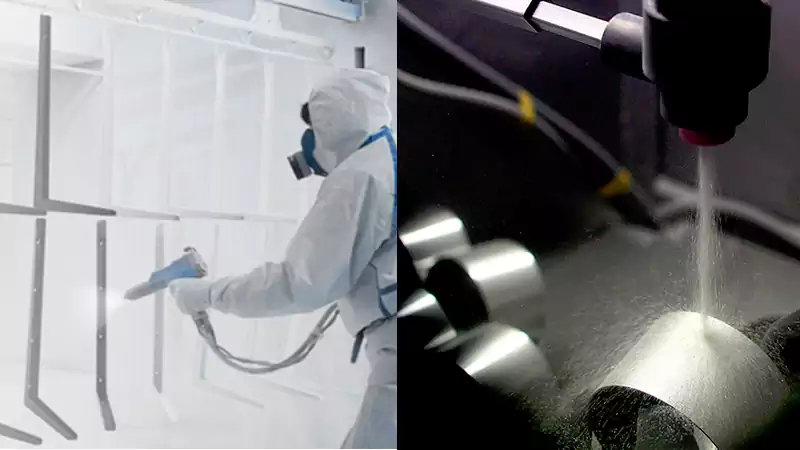
Decision-Making Uncovered
For an engineer like David, making the correct choice between sandblasting and glass bead blasting services is a critical step in the manufacturing process. A wrong decision can compromise the part's function, appearance, or dimensional integrity. Here’s a simple framework based on a few key questions to guide the decision.
1. What is the primary objective of the blasting process?
- "I need to remove heavy rust, thick paint, or corrosion." -> Choose Sandblasting. Its aggressive cutting action is required for this.
- "I need a beautiful, uniform cosmetic finish on the final part." -> Choose Glass Bead Blasting. It provides a smooth, satin finish.
- "I need to clean the part lightly and remove discoloration or small burrs." -> Choose Glass Bead Blasting. It cleans without damaging the surface.
- "I need to prepare the surface for a strong bond with paint or powder coating." -> Choose Sandblasting. The anchor profile it creates is essential for adhesion.
2. What is the workpiece material and is it delicate?
- "The part is made of structural steel or thick cast iron." -> Sandblasting is generally safe and effective.
- "The part is made of softer metal like aluminum, brass, or copper, or it's a thin-walled component." -> Glass Bead Blasting is the much safer option to prevent warping, erosion, or surface damage.
3. Are dimensional tolerances4 critical?
- "Yes, this is a precision-machined part with tight tolerances that must be maintained." -> You must choose Glass Bead Blasting. Sandblasting will remove base material and alter the part's dimensions. This is a non-negotiable point I always stress with my clients.
4. What is the next step in the manufacturing process?
- "Blasting is the final step before assembly." -> Almost certainly requires Glass Bead Blasting for a clean, finished appearance.
- "The part will go to the paint shop or for another coating process after blasting." -> Sandblasting is the standard preparation method.
By answering these questions, David can confidently specify the correct abrasive blasting process, ensuring the final part meets all of his functional and aesthetic requirements. At Allied Metal, we always consult with our clients to make sure the chosen finishing process is perfectly aligned with their goals.
Contact Allied Metal for Premium Sandblasting Services
Allied Metal is your one-stop solution for high-quality CNC machining and surface preparation services, including sandblasting and glass bead blasting. With over 20 years of industry experience, we specialize in machining complex, custom parts with precision and consistency.
Whether you need advanced CNC solutions or expert metal finishing, we've got you covered.
Conclusion
Sandblasting aggressively preps surfaces for coating, while glass bead blasting provides a fine, cosmetic finish. Choosing the right method is critical for part integrity, function, and appearance.
-
Exploring the health risks of Silica Sand can help you make informed decisions about safety in sandblasting operations. ↩
-
Learn why Aluminum Oxide is favored in sandblasting for its efficiency and effectiveness in surface preparation. ↩
-
Understanding etching can enhance your knowledge of surface preparation techniques and their importance in various industries. ↩
-
Understanding dimensional tolerances is crucial for maintaining precision in manufacturing, ensuring parts fit and function correctly. ↩